Petroleum-based plastics have become an international waste hazard. Microplastic has invaded every part of our ecosystem—even into our bodies. The search for compostable, yet usable, alternatives has not been satisfactory so far. This press release just came my way. It tells a story (unlike most publicity) about the development of compostable plastic made from agricultural waste usable in existing injection molding machinery and quickly reverts to usable compost to return to the farm. Brilliant!
The company is PlantSwitch and here is its story as told by their publicity agent.
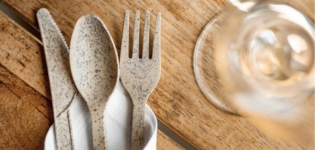
In 2019, 22-year-old Dillon Baxter was a senior at Southern Methodist University studying engineering while interning at a private equity firm when a proposal for a plastic alternative came across his desk. Although the company didn’t land an investment with the private equity firm Baxter was interning with, his interest was piqued.
One of the reasons previous plastic alternative companies hadn’t been able to take their product into the stratosphere, explains Baxter, was that they failed to entice big business because they didn’t offer a drop-in solution. “Large corporations that need to mold plastic products have already made significant investments in their existing machinery,” explains Baxter. “They were never going to embrace a plastic alternative that requires new machinery, thereby driving the costs way up and undermining corporate profits.”
He knew that if he was going to engineer a viable plastic alternative, it would have to be what he calls a “drop-in solution,” meaning his plastic alternative pellets would need to be compatible with existing plastic processing machinery.
Baxter got in touch with Maxime Blandin, a fellow SMU student with tight connections among suppliers and the two got to work. “I left my job and career track at a Private Equity Firm to set about our crazy goal of creating the world’s first environmentally sound, sustainable, scalable plastic alternative.”
After several trials, Baxter and Blandin discovered a method of upcycling agricultural waste derived from everything from rice husks, wheat straw and other cellulose rich byproducts combined with a polymer to make sustainable and scalable bioplastics while simultaneously upcycling agricultural waste.
The result mimics the texture, durability, and performance of traditional petroleum-based plastic completely, drops into existing plastic processing machinery and costs less than any other plastic alternative ever brought to market. Best of all, it is the only plant-based plastic alternative that completely breaks down within hours in an everyday home composting bin. The company, called PlantSwitch (founded in 2020), also has a carbon negative production process.
PlantSwitch is the game changer for all single use plastics that hundreds of millions of us use every day.
Corporate America and the U.S. Government has taken notice. Baxter and Blandin’s PlantSwitch has raised a total of $19.5 Million, to date, including a recently closed bridge round with Dallas-based alternative investment firm NexPoint Capital. Other investments include a federal grant from the U.S. Department of Agriculture.
“Having institutional backing is a huge step for PlantSwitch and for our environment,” says Baxter, now 26. “With our steadily growing capital, we will be able to continue to scale our business and deliver sustainable and biodegradable bioplastics to some of the largest companies and conglomerates in the U.S.”
PlantSwitch’s 52,000sf manufacturing facility has the capability of making 50 million lbs. of its bioplastics annually.
“Our goal is to replace petroleum-based single-use plastic with plants through the manufacturing and distribution of our compostable bioplastic resin,” shares Baxter.
PlantSwitch has recently entered into framework contracts with several nationwide restaurant and grocery store chains that will begin supplying as early as January 2024.