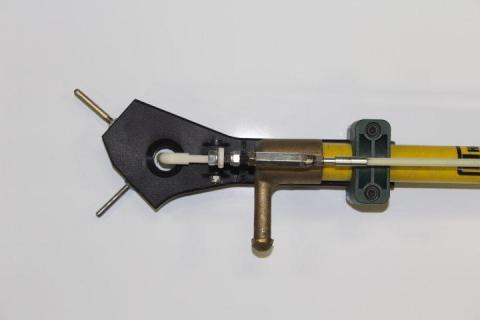
Electrical Safety Invention for Manufacturing Technicians
I don’t do a lot of products yet at this site, but I’m old enough to remember the times before lockout/tagout. And old enough to remember many injuries and almost deaths at places where I worked. I really like all the cool ideas that have evolved over the past 20 years.
Here is one from Eaton, a company well known for power management. Employees at the company’s Shenandoah, Iowa, commercial vehicle transmission plant have invented a new electrical lockout device that minimizes electrical safety risks during machine maintenance and significantly improves efficiency of the lockout procedure.
Eaton’s Vehicle Group is in the process of installing the newly developed Bus Plug Lockout at more than 40 manufacturing facilities worldwide. Maintenance technicians and tool designers at the Shenandoah facility collaborated to invent the device on which a patent application is pending in the U.S. Patent and Trademark Office.
The new device allows workers to safely disable power to plant equipment at an electrical bus bar – typically located 13 feet off the ground – without having to use an aerial lift. In addition to eliminating exposure to arc flashes and working at heights, using the Bus Plug Lockout device reduces the former 11-step process to just three steps, saving more than an hour of time.
“The new safety device embraces Eaton’s Zero Incident culture and shows the ingenuity of our employees in Shenandoah,” said Jorge Zedillo, Shenandoah plant manager.
The U.S. Occupational Safety and Health Administration requires workers to lock out power to manufacturing equipment prior to servicing or maintenance. Such lockouts typically are done directly at the machine on the ground.
Define Lockout
Locking out at the bus bar completely disables power to the corresponding plant equipment, which eliminates potential exposure to electrical arc flashes when a technician opens the machine for maintenance. In the past, workers needed an aerial lift to access the bus bar. To use the lift they had to be properly trained and were required to follow strict time-consuming procedures.
Eaton developed the Bus Plug Lockout tool by modifying an existing hot stick – an insulated pole used to protect workers from electrical shock when testing voltage or performing maintenance. The non-conductive frame and fiberglass linkage for the Bus Plug Lockout can be easily attached and removed to a hot stick as needed, allowing workers to reach up and turn power off at the bus bar.
The new lockout device can handle up to 100 amps, which is the limit for 90 percent of the more than 850 bus bars at Eaton’s Shenandoah plant. The facility currently has three Bus Plug Lockout units, including one with a short handle for easier use on lower bus bars. Shenandoah workers have quickly adopted the use of the devices, saving the facility both time and money.
“But the real benefit is eliminating the need to work at heights during the lockout procedure,” said Jason Hawpe, environmental, health and safety manager for the Shenandoah plant. “You can’t fall out of an aerial lift or off a ladder if your feet are firmly planted on the ground.”
The Bus Plug Lockout design can be adapted for any 100-amp unit and could potentially be used by any manufacturing company to safely and efficiently lock out bus bars.