I started out in a small shop. I had roles that encompassed purchasing, production/inventory control, manufacturing engineering, and even worked production when something needed done.
So it was that one day I was trimming parts from a vacuum-formed plastic sheet using a bandsaw. Probably illegal today, may have been back then for all I know. Occasionally I would catch my mind drifting away. A guitar player, I’d pause and count fingers just to be sure.
Humans want jobs. But jobs that don’t challenge creativity and problem-solving but are only tedious, repetitive, mind-numbing can lead to tragedy.
A major reason robots gained such wide use especially in automotive manufacturing was that very problem along with removing humans from unsafe environments. Use robots when the task is dirty, dull, or dangerous.
The new breed of collaborative robots, or cobots, help expand robot’s usage into new areas of industry.
For example, this partnership just announced between Phillips Corp. and Universal Robots for loading and unloading CNC machines. Phillips Corporation, the largest global distributor of Haas CNC machines, offers a fast track to spindle uptime using Universal’s cobots.
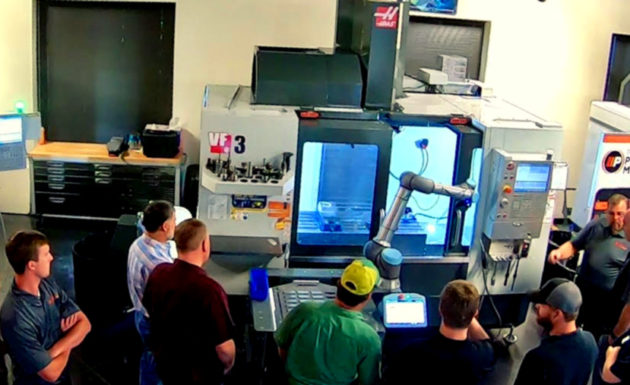
“Having an expensive machine sit idle and missing out on orders due to lack of staffing is every manufacturer’s nightmare,” says Stu Shepherd, Regional Sales Director for the Americas division of Universal Robots (UR) that has already sold more than 1,000 UR cobots for tending Haas CNC machines. “This partnership between the largest distributor of the leading CNC brand and the leading collaborative robot brand offers a huge advantage for manufacturers, helping them solve staffing issues and stay competitive. We expect this new partnership to fast-track cobots in this sector, with significant advantages for manufacturers.”
With 9 offices representing 12 states throughout the South and Mid-Atlantic regions, Phillips Corporation boasts an installed base of more than 19,000 Haas CNC machines. “There is tremendous potential both for retrofitting existing installations with UR cobots and for getting through the door to new customers, offering turn-key solutions,” says president of Phillips Corporation’s commercial division, Michael Garner, who is also the chairman of Haas Automation’s North American distributor council. “We see a significant demand for cobots, which address labor shortages and also support manufacturers who need flexible automation tools they can operate without safety caging,” adds the Phillips president, stressing the UR cobots’ ease of programming. “There is no hardwiring or complex coding involved in getting a Universal Robot to communicate with a Haas machine since UR has solutions like the VersaBuilt software that facilitates two-way communication between the UR cobot and the CNC.”
VersaBuilt’s Haas CNC Integration Kit is a simple yet powerful interface that enables UR cobots to easily execute any machining program stored on the Haas CNC directly through the cobot’s own teach pendant, maintaining all Haas safety interlock features. Versabuilt is available through the UR+ platform, a showroom of products all certified to integrate seamlessly with UR cobots.
More than 60 different Haas models can be automated Universal Robots’ cobot arms. UR’s Stu Shepherd emphasizes how fast integration also means fast ROI. “Machine tending applications have consistently delivered an ROI of less than a year, sometimes even paying themselves back in a few months. A Haas-UR solution offered with Phillips’ CNC expertise and application know-how will help further improve that payback time.