by Gary Mintchell | Oct 22, 2019 | Manufacturing IT, Software
Inductive Automation has selected the recipients of its Ignition Firebrand Awards for 2019. The announcements were made at the Ignition Community Conference (ICC), which took place September 17-19. I get to see the poster displays and chat with the companies at ICC. I love the technology developers, but it’s fascinating to talk with people who actually use the products.
[Disclaimer: Inductive Automation is a long-time and much appreciated sponsor of The Manufacturing Connection. If you are a supplier, you, too, could be a sponsor. Contact me for more details. You would benefit from great visibility.]
The Ignition Firebrand Awards recognize system integrators and industrial organizations that use the Ignition software platform to create innovative new projects. Ignition by Inductive Automation is an industrial application platform with tools for the rapid development of solutions in human-machine interface (HMI), supervisory control and data acquisition (SCADA), manufacturing execution systems (MES), and the Industrial Internet of Things (IIoT). Ignition is used in virtually every industry, in more than 100 countries.
“The award-winning projects this year were really impressive,” said Don Pearson, chief strategy officer for Inductive Automation. “Many of them featured Ignition 8 and the new Ignition Perspective Module, both of which were released just six months ago. We were really impressed with how quickly people were able to create great projects with the new capabilities.”
These Ignition Firebrand Award winners demonstrated the power and flexibility of Ignition:
- Brock Solutions worked with the Dublin Airport in Ireland to replace the baggage handling system in Terminal 2. The new system has 100,000 tags and is the largest Ignition-controlled airport baggage handling system in the world.
- Corso Systems & SCS Engineers partnered on a pilot project for the landfill gas system of San Bernardino County, California. The pilot was so successful, it will be expanded to 27 other county sites. It provides a scalable platform with strong mobile capabilities from Ignition 8 and Ignition Perspective, plus 3D imaging from drone video and virtual reality applications.
- ESM Australia developed a scalable asset management system to monitor performance and meet service requirements for a client with systems deployed all over Australia. The solution leveraged Ignition 8, Ignition Perspective, MQTT, and legacy FTP-enabled gateways in the field.
- H2O Innovation & Automation Station partnered to create a SCADA system for the first membrane bioreactor wastewater treatment plant in Arkansas. The new system for the City of Decatur shares real-time data with neighboring water agencies as well as the mayor.
- Industrial Networking Solutions created a new oil & gas SCADA system in just six months for 37 sites at ARB Midstream. The solution included hardware upgrades, a new control room, and a diverse collection of technologies with cloud-hosted SCADA, MQTT, Ignition Edge, and SD-WAN.
- MTech Engineering developed an advanced real-time monitoring and control system for the largest data center campus in Italy. The project for Aruba S.p.A. had to work with huge amounts of data — and was done at a much lower cost than was possible with any other SCADA solution.
- NLS Engineering created a single, powerful operations and management platform for more than 30 solar-power sites for Ecoplexus, a leader in renewable energy systems. The solution provided deep data acquisition, included more than 100,000 tags, and led to the creation of a platform that can be offered to other clients.
- Streamline Innovations used Ignition, Ignition Edge, Ignition Perspective, and MQTT, to facilitate the automation of natural gas treating units that convert extremely toxic hydrogen sulfide into fertilizer-grade sulfur. The solution increased uptime, reduced costs, and provided access to much more data than Streamline had seen previously.
by Gary Mintchell | Oct 19, 2019 | Automation, Internet of Things, Technology, Uncategorized
This is still more followup from Emerson Global Users Exchange relative to sessions on Projects Pilot Purgatory. I thought I had already written this, but just discovered it languishing in my drafts folder. While in Nashville, I ran into Jonas Berge, senior director, applied technology for Plantweb at Emerson Automation. He has been a source for technology updates for years. We followed up a brief conversation with a flurry of emails where he updated me on some presentations.
One important topic centered on IoT projects—actually applicable to other types of projects as well. He told me the secret sauce is to start small. “A World Economic Forum white paper on the fourth industrial revolution in collaboration with McKinsey suggests that to avoid getting stuck in prolonged “pilot purgatory” plants shall start small with multiple projects – just like we spoke about at EGUE and just like Denka and Chevron Oronite and others have done,” he told me.
“I personally believe the problem is when plants get advice to take a ‘big bang’ approach starting by spending years and millions on an additional ‘single software platform’ or data lake and hiring a data science team even before the first use case is tackled,” said Berge. “My blog post explains this approach to avoiding pilot purgatory in greater detail.”
I recommend visiting Berge’s blog for more detail, but I’ll provide some teaser ideas here.
First he recommends
- Think Big
- Start Small
- Scale Fast
Scale Fast
Plants must scale digital transformation across the entire site to fully enjoy the safety benefits like fewer incidents, faster incident response time, reduced instances of non-compliance, as well as reliability benefits such as greater availability, reduced maintenance cost, extend equipment life, greater integrity (fewer instances of loss of containment), shorter turnarounds, and longer between turnarounds. The same holds true for energy benefits like lower energy consumption, cost, and reduced emissions and carbon footprint, as well as production benefits like reduced off-spec product (higher quality/yield), greater throughput, greater flexibility (feedstock use, and products/grades), reduced operations cost, and shorter lead-time.
Start Small
The organization can only absorb so much change at any one time. If too many changes are introduced in one go, the digitalization will stall:
- Too many technologies at once
- Too many data aggregation layers
- Too many custom applications
- Too many new roles
- Too many vendors
Multiple Phased Projects
McKinsey research shows plants successfully scaling digital transformation instead run smaller digitalization projects; multiple small projects across the functional areas. This matches what I have personally seen in projects I have worked on.
From what I can tell it is plants that attempt a big bang approach with many digital technologies at once that struggle to scale. There are forces that encourage companies to try to achieve sweeping changes to go digital, which can lead to counterproductive overreaching.
The Boston Consulting Group (BCG) suggests a disciplined phased approach rather than attempting to boil the ocean. I have seen plants focus on a technology that can digitally transform and help multiple functional areas with common infrastructure. A good example is wireless sensor networks. Deploying wireless sensor networks in turn enables many small projects that help many departments digitally transform the way they work. The infrastructure for one technology can be deployed relatively quickly after which many small projects are executed in phases.
Small projects are low-risk. A small trial of a solution in one plant unit finishes fast. After a quick success, then scale it to the full plant area, and then scale to the entire plant. Then the team can move on to start the next pilot project. This way plants move from PoC to full-scale plant-wide implementation at speed. For large organization with multiple plants, innovations often emerge at an individual plant, then gets replicated at other sites, rolled out nation-wide and globally.
Use Existing Platform
I have also seen big bang approach where plant pours a lot of money and resources into an additional “single software platform” layer for data aggregation before the first use-case even gets started. This new data aggregation platform layer is meant to be added above the ERP with the intention to collect data from the ERP and plant historian before making it available to analytics through proprietary API requiring custom programming.
Instead, successful plants start small projects using the existing data aggregation platform; the plant historian. The historian can be scaled with additional tags as needed. This way a project can be implemented within two weeks, with the pilot running an additional three months, at low-risk.
Think Big
I personally like to add you must also think of the bigger vision. A plant cannot run multiple small projects in isolation resulting in siloed solutions. Plants successful with digital transformation early on establish a vision of what the end goal looks like. Based on this they can select the technologies and architecture to build the infrastructure that supports this end goal.
NAMUR Open Architecture (NOA)
The system architecture for the digital operational infrastructure (DOI) is important. The wrong architecture leads to delays and inability to scale. NAMUR (User Association of Automation Technology in Process Industries) has defined the NAMUR Open Architecture (NOA) to enable Industry 4.0. I have found that plants that have deployed digital operational infrastructure (DOI) modelled on the same principles as NOA are able to pilot and scale very fast. Flying StartThe I&C department in plants can accelerate digital transformation to achieve operational excellence and top quartile performance by remembering Think Big, Start Small, Scale Fast. These translate into a few simple design principles:
- Phased approach
- Architecture modeled on the NAMUR Open Architecture
- Ready-made apps
- East-to-use software
- Digital ecosystem
by Gary Mintchell | Oct 17, 2019 | Security
If I would offer you an opportunity to spend $300 and make $50,000 right away with more to come and no additional expense, would you take it? What about downloading a cybersecurity hack for that much off the Dark Web and using it to steal a $50,000 car?
Such a possibility exists Etay Maor, Chief Security Officer of IntSights told me yesterday. His firm, a threat intelligence company focused on enabling enterprises to Defend Forward, released the firm’s new report, Under the Hood: Cybercriminals Exploit Automotive Industry’s Software Features. The report identifies the inherent cybersecurity risk and vulnerabilities manufacturers face as the industry matures through a radical transformation towards connectivity.
Car manufacturers offer more software features to consumers than ever before, and increasingly popular autonomous vehicles that require integrated software introduce security vulnerabilities. Widespread cloud connectivity and wireless technologies enhance vehicle functionality, safety, and reliability but expose cars to hacking exploits. In addition, the pressure to deliver products as fast as possible puts a big strain on the security capabilities of cars, manufacturing facilities, and automotive data.
The two main things that affect hackers’ motivation, regardless of their skills and knowledge are the cost effectiveness of the attack and the value of the information.
Vehicles usually have more complicated attack surfaces to penetrate compared to other options, i.e. attacks against banks or retail shops. That said, the automotive industry still has numerous attack vectors, just as any other industry: needs Phishing, credential leakages, leaked databases, open ports, and services, insider threats, brand security, and more.
Dark Web Forums
In the research, IntSights discovered online shops that sell car hacking tools that appear on the clear web and are easy to find. These online shops sell services that disconnect automobile immobilizers, as well as services that sell code grabbers and forums that give bad actors a complete tutorial on how to steal vehicles.
“The automotive manufacturing industry is wrought with issues, stemming from legacy systems that can’t be patched to the proliferation of vehicle connectivity and software as consumers demand more integration with personal devices and remote access,” said Maor. “A lack of adequate security controls and knowledge of threat vectors enables attackers to take advantage of easily acquired tools on the dark web to reap financial gain. Automakers need to have a constant pulse on dark web chatter, points of known exposure, and data for sale to mitigate risk.”
Top Vehicle Attack Vectors:
- Remote Keyless Systems
- Tire Pressure Monitoring Systems
- Software and Infotainment Applications
- GPS Spoofing
- Cellular Attacks
Other attack vectors explored include:
- CAN-BUS
- Attacking Can-BUS
- Remote Attack Vectors
- Car Applications
- Physical Attack Vectors
IntSights has “the industry’s only all-in-one external threat protection platform designed to neutralize cyberattacks outside the wire.” Its cyber reconnaissance capabilities enable continuous monitoring of an enterprise’s external digital profile across the clear, deep, and dark web to identify emerging threats and orchestrate proactive response.
by Gary Mintchell | Oct 16, 2019 | Software
The design engineering function originates data. It includes data about the structure of the plant or factory, data about the equipment and processes used to make the product, and data about the product(s) itself. In my early career, I embodied the movement of the data from design to operations and then back to design in a continuous loop of as designed—>as built—>as designed. I was also involved for a while in the development of a platform to automate this process using standards.
To say I’m interested in this area would be an understatement. And this process is important to all of you, too. Including those who siphon off some data for other uses such as accounting, customer service, maintenance, and reliability.
AVEVA, the integration of its iconic design engineering software and Schneider Electric’s software business, just introduced integrated engineering software designed to help customers transform the way capital projects are engineered, executed, and integrated into operations and maintenance.
The integrated portfolio comprises three software solutions. AVEVA Unified Engineering integrates process design with front-end engineering and detailed 3D based design. AVEVA Unified Project Execution links and streamlines procurement and construction processes for capital projects. AVEVA Enterprise Learning enables the rapid skilling of operators and engineers using Extended Reality (XR) and simulation tools, to ensure efficient startups and shutdowns, normal operations, and the ability to handle abnormal situations
“This launch builds on the recent news describing AVEVA’s capabilities as the first company in the engineering and industrial software market to comprehensively address the end-to-end digital transformation imperatives with an integrated portfolio of solutions that deliver efficiency, unlock value and empower people across the lifecycle of capital assets and operational value chains,” commented Craig Hayman, CEO, AVEVA. “It changes the way that owner operators engage with Engineering, Procurement and Construction (EPC) companies in designing, building, commissioning, and operating their capital assets.”
The functionality provided in these integrated solutions enables the realization of an EPC 4.0 strategy for owner operators, central to digital transformation in the capital-intensive process sectors. This allows collaboration on a global scale, through hybrid cloud architectures and on a common platform. The entire manufacturing process can be traced, tracked, and linked – from engineering and design, through procurement and construction, to handover and to operations and maintenance, as a comprehensive Digital Twin for the capital asset.
“As competition in the business world accelerates the time has come for industrial organization to innovate to facilitate the transition from the manual, document-centric processes, towards a data-driven vision of project design, procurement, and execution in order to increase safety, reduce costs, and minimize delays, “ commented Craig Hayman, CEO AVEVA. “With the launch of AVEVA Unified Engineering, a first of its kind solution, we are breaking down the silos between engineering disciplines and enabling our customers to turn conceptual designs into 3D models quickly, accelerating engineering to estimation and ensuring designs can be operated before committing billions of dollars.”
New AVEVA Unified Engineering enables the integration of the process model and plant model lifecycles from concept to detailed design, delivering frictionless collaboration for multi-discipline engineers to collaborate in the cloud. The net result is a minimum 50% improvement in engineering efficiency in FEED and up to 30% in detail design, which can yield a 3% total installed cost improvement. These savings can be re-invested to ensure engineering quality, accuracy, and maturity for downstream project execution business processes.
AVEVA Unified Project Execution solutions integrate with AVEVA Unified Engineering to further break down the silos within Procurement and Construction by combining key disciplines covering Contract Risk Management, Materials and Supply Chain Control, and Construction Management into one cloud based digital project execution environment. AVEVA Unified Project Execution solutions deliver up to 15% reduction in material costs, 10% reduction in field labor costs and reduces unbudgeted supplier change orders by up to 50%, which translates to 10% total installed costs savings opportunities for our customers.
AVEVA’s Enterprise Learning solutions combine traditional simulation-based learning with 3D connected learning management solutions. AVEVA’s learning solutions extend process models and 3D models from AVEVA Unified Engineering to fast track DCS panel operator training, field operator training, process and maintenance procedural training, and process safety situational awareness training using cloud and Extended Reality (XR) technology to deliver up to 2% Total Installed Cost reduction by improved operations readiness.
“Our Engineering portfolio enhancements will deliver increased agility for our customers, enabling them to reduce cost, risk, and delays, minimizing errors and driving rapid capital project execution. The cost savings are realized by mitigating capital investment risks at the process design stage, cutting engineering man-hours by up to 30% in plant design, reducing material costs in procurement by up to 15% as well as reducing field labor costs in construction by up to 10%,” commented Amish Sabharwal, SVP, Engineering Business, AVEVA. “With these new solutions AVEVA is providing integration across all stages of the capital project, from conceptual design to handover, to optimize collaboration and break down silos between both engineering disciplines and project stages.”
by Gary Mintchell | Oct 15, 2019 | Commentary, Education, Personal Development
This is a post about education, personal development, and why you should be a generalist.
Tiger Woods was trained almost from the cradle for one thing–to be the greatest golfer.
Roger Federer tried many sports. He loved soccer. Even though his mother was a tennis teacher, he didn’t pick up tennis until his early teens. Other kids had been playing for years by then. He soon passed them by and into his thirties is a dominant tennis star.
You need to be good at something, but it is good to be interested and experienced in many things.
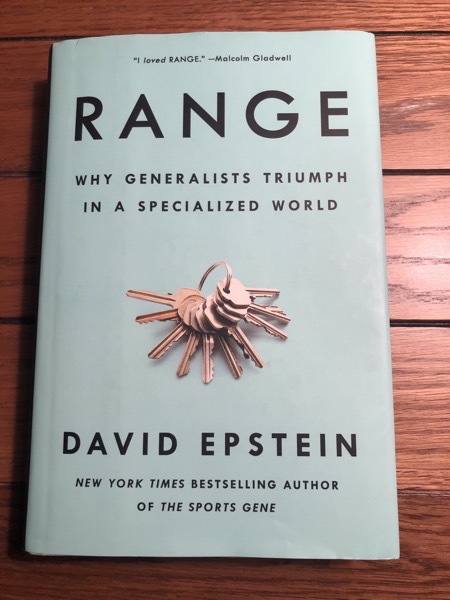
I have a book to recommend. Range: Why Generalists Triumph in a Specialized World, by David Epstein. This book will help you learn to live a fuller life–and help you bring up your kids and encourage your grandkids.
Life in the industrial age, as well as in some previous eras, was composed of patterns. You could be trained to recognize patterns and adapt and become skilled at them. These are called “kind” learning environments. Kids excel who see and repeat the patterns.
Life today is what a psychologist call a “wicked” learning environment. Here, the rules of the game are often unclear or incomplete, there may or may not be repetitive patterns, and they may not be obvious, and feedback is often delayed, inaccurate or both. In most devilishly wicked learning environments, experience will reinforce the exact wrong lessons.
So, let’s look at responding to today’s “wicked” learning environment. “The bigger the picture, the more unique the potential human contribution. Our greatest strength is the exact opposite of narrow specialization. It is the ability to integrate broadly.” This all sounds great. But what about what I read in the news as the “typical Trump voter” who is a worker trained in the old way watching his job being replaced. And who is the leader who is poised to take them to this next level? Well, no one. Just leaders who play to their fears.
There are some courageous leaders changing the system for educating young people so that they can thrive in this new environment. We just have to have more of that. More people guiding young people—and older people, as well—need to take into practice this advice from psychologist and creativity researcher Dean Keith Simoton, “Rather than obsessively focusing on a narrow topic, creative achievers tend to have broad interests.” Modern work demands knowledge transfer—the ability to apply knowledge to new situations and different demands. In my life I have worked with both highly educated engineers AND high-school-educated technicians who exhibit this. More must be encouraged.
For those who, like me, studied broadly as an undergraduate and didn’t care much about grades, take this observation from professor and researcher James Flynn who was “bemused to find that the correlation between the test of broad conceptual thinking and GPA was about zero. Flynn, “The traits that earn good grades at [the university] do not include critical ability of any broad significance.
Here is a tip for those who teach at any level. When asking a student a question, force them to answer, even if it is wrong. Then just force them to answer again. And again. Until they get it right. Giving them hints to guide a correct answer quickly provided fewer long-term results than the first method. “Repetition is less important than struggle.”
Oh, and in a test of forecasting, experts were far worse than “amateurs” getting it right!
How does one adapt? By reading widely. Pursue several interests. That will be the human triumph in an age of robots.