by Gary Mintchell | Feb 24, 2021 | Automation, Business, News, Technology
Schneider Electric presented a couple of news items to us at the ARC Industry Forum a couple of weeks ago. It continues to push its evangelization of software-defined control using IEC 61499. It also announced a strategic agreement with Wood plc. I just got off a Webcast billed as customers using Automation Expert. Instead, it was a deep dive into the product—which is OK.
Interesting note (to me, anyway) that the speaker called IEC 61499 a new standard written with Industry 4.0 in mind. I pulled a book from my library a couple of weeks ago that I reviewed in 2001, “Modeling Control Systems Using IEC 61499”. Anyway, this really is a step in the right direction. The Open Process Automation group uses this standard, among others. One last weird note—they call Automation Expert new, but they just released version 21.0?
Schneider Electric announced EcoStruxure Automation Expert version 21.0, the next in an ongoing series of updates and enhancements for the world’s first software-centric system.
Schneider Electric is implementing Agile software development methodology to deliver a new EcoStruxure Automation Expert release, based on direct customer feedback, every six months.
“Keeping pace with rapid innovation while still maintaining the capability to be 100% future proof is a key benefit of EcoStruxure Automation Expert for our customers,” said Fabrice Jadot, senior vice president, next generation automation, Schneider Electric. “In the space of a couple months we’ve added features and functions that will enhance the user experience and directly address high-demand customer needs. Our best-in-class implementation of agile mode project delivery¾along with an overall agile mindset¾helps us provide an always-current experience for our users.”
IEC 61499 adoption
EcoStruxure Automation Expert, first launched to the public in November 2020, is the world’s first universal automation offer, based on the IEC61499 standard for interoperability and portability.
Early interest in this new category of industrial automation is strong. The company reports that its integrator partners see enormous benefit in being able to add value beyond traditional PLC control. Early adopters are innovating to provide comprehensive, more capable solutions by combining technologies for their customers.
“This is not the same automation platform from 30 or 40 years ago, so there’s an initial learning curve for adjusting to IEC61499-based technology,” said Jadot. “But we’re finding that once customers and partners dive into the technology, they see real returns in flexibility and speed of engineering unlike anything they’ve experienced before. When users realize the full value of EcoStruxure Automation Expert, the most common response is, ‘This is a game changer.’”
EcoStruxure Automation Expert is particularly drawing interest from businesses in the consumer packaged goods and logistics sectors where the added flexibility is needed to react quickly to changing market dynamics, take advantage of new opportunities, or rapidly mitigate potential risk.
Next-generation technology
Enhancements in EcoStruxure Automation Expert V21.0 include:
- EtherNet/IP scanner for software programmable automation controller
- ASi-5 gateway
- Position control with Lexium 32 servo drives
and updates include:
- Common function library improvements
- Improved user interface
- Ability to define supported function blocks in logical devices
- Physical view enhancements
- Other quality, performance, security and usability enhancements
Universal automation
Universal automation is the world of plug and produce automation software components based on the IEC61499 standard that solve specific customer problems in a proven way. Adoption of a universal automation layer, common across vendors, will provide limitless opportunities for growth and modernization across industry.
By greatly extending the capabilities of existing IEC61131-based systems and enabling an app-store-like model for automation software components, the advancements possible in the Fourth Industrial Revolution will be fully realized. As its benefits become visible, Schneider Electric believes other vendors will adopt universal automation, and end users will soon begin to demand it from their automation suppliers and ecosystem.
Schneider Electric and Wood Forge Strategic Agreement
Schneider Electric has formed a strategic relationship with Wood, a global leader in delivering automation solutions for projects, operations and consulting services to energy, industrial, and several other vertical markets, to make open and interoperable automation a reality for customers.
The memorandum of understanding agreement provides Wood’s automation and control group access to Schneider Electric’s IEC61499-based software, helping them deliver open, standards-based automation solutions to their global energy and industrial customers. Using object-oriented, event-based programming, where hardware and software lifecycles are decoupled and engineering efficiency is optimized, Schneider Electric and Wood are now able to provide mutual clients with next-generation, open automation and control, which can deliver step-change operational improvements today while also simplifying upgrades in the future.
“With closed systems, the full potential of Industry 4.0 remains untapped,” said Fabrice Jadot, Senior Vice President, Industrial Automation, Schneider Electric. “To accelerate industrial digital transformation, we must prioritize portability of automation applications. Today, agility and resilience are paramount. The IEC61499 standard delivers that needed interoperability and that’s why it is fundamental to the shift towards more flexible automation. We are delighted to be working with Wood, an industry innovator that has been leveraging the benefits of IEC61499, to deliver the next-generation automation solutions that end users need to thrive in the digital economy.”
“By combining our diverse capabilities and domain expertise in automation with the IEC61499 technology, we can unlock unprecedented innovation for our customers,” said Bridget Fitzpatrick, Global Process Automation Authority, Wood. “The siloed nature of industry is holding us all back. We agree that collaboration is essential to next-generation industries, and IEC61499 is the enabler. We look forward to continuing to bring greater value to our customers’ projects and welcoming a new era of open automation.”
by Gary Mintchell | Feb 10, 2021 | Automation, News, Organizations, Technology
OMAC, now dubbed Organization for Machine Automation and Control and a part of PMMI, first zapped to my attention at the 1998 ARC Forum. I’ve followed it for the ensuing 23 years through some ups and downs. It never successfully came up with a PLC built entirely from standards to put pressure on the major companies to bring prices down. On the other hand, a lot of the standardization discussions led activists in a variety of beneficial directions. Plus, a group of packaging end users and suppliers devised PackML and other standards that brought organization to control logic and HMI for packaging machines.
This is ARC Forum week, but none of us made the trip to Orlando this year. I had not heard from the organization for some time, so I reached out to Bryan Griffen, who is now Director of Industry Services for PMMI (Packaging Machinery Manufacturers Institute) and leader of OMAC, for an update. Griffen was previously director of engineering for an end user and implementer of the standard.
OMAC is still going strong. 2020 was a bit of a down year in terms of visibility since there were no events in which we could participate to get some exposure. However, we got a lot of things accomplished last year that are being rolled out now. Here are a few of the highlights:
• We completed an update of the ISA-TR88.00.02 (PackML). We slightly updated the state model, added several new PackTags, and improved the overall document content. The update is currently being reviewed by ISA for official publication. We hope to have it out in next couple of months. Yaskawa led this activity.
• We developed a new HMI and stacklight guideline for use with PackML implementations. It provides a common look and feel to operator interfaces in order to facilitate training, operations and maintenance activities. Mettler Toledo led this activity.
• We developed an new OEE guideline and new PackTags for implementing automatic OEE calculations on a PackML enabled line. ProMach led this activity.
• We just completed a new white paper on best practices for remote access to enable data collection, troubleshooting, upgrades and other remote activities. This effort was led by ei3.
• We are just now finishing up the design and migration to a new web platform. The new website will go live on March 1 and will include pages for all of the items above.
We are also just starting the election process for three open seats on the Board of Directors. This process will continue through March. We are planning a virtual General Session meeting in early April to announce the new board members, highlights from 2020, officially unveil the new website and so forth. The date for the General Session will be posted on the website as soon as we have nailed it down. The meeting is open to anyone, not just OMAC members.
by Gary Mintchell | Feb 5, 2021 | Automation, Technology
Many companies have been prototyping applications with Microsoft’s HoloLens augmented reality “glasses.” I have experienced many of these at a variety of trade shows (remember those?). Microsoft recently sent a link to some news from Charlie Han. Principal Program Manager at Microsoft regarding updates.
It’s been an energizing first year, in-market, for HoloLens 2. We loved seeing the ways HoloLens 2 has empowered customers across industries to increase productivity and innovate with purpose.
- Lockheed Martin is using HoloLens 2 to build the Orion spacecraft and reduce touch labor—what used to require an eight-hour shift can now be completed in just 45 minutes.
- Imperial College Healthcare NHS Trust is using HoloLens 2 to limit healthcare employee’s exposure to patients with COVID-19, reducing the time staff are exposed to the disease by as much as 83 percent.
- Mercedes-Benz USA is using HoloLens 2 to improve service technician efficiency and reduce time to problem resolution, realizing a 35 to 40 percent decrease in service technician travel.
As part of listening, and always learning, we heard strong demand for HoloLens 2 to operate in environments that have rigorous requirements or are regulated by industry certifications. In the semiconductor and pharmaceutical industries, partners require a device that meets particle emissions standards to enter and operate in their highly controlled clean room environments. In the energy sector, partners need a device that can function safely in potentially hazardous environments.
Enhance worker productivity and accelerate innovation
We are announcing the HoloLens 2 Industrial Edition, an untethered mixed reality device designed, built, and tested to support regulated industrial environments.
In addition to the industrial standards ratings, HoloLens 2 Industrial Edition is supported with a two-year warranty and a Rapid Replacement Program. The Rapid Replacement program minimizes downtime, with advance exchange and expedited shipping.
With HoloLens 2 Industrial Edition, customers can now use HoloLens 2 in restricted environments without modifying your space, protocols, or workflows. Supported with a robust ecosystem of first and third party mixed reality applications that are backed by the reliability, security, and scale of Azure, HoloLens 2 Industrial Edition will empower enterprises operating in regulated environments to:
- Provide workers with access to remote experts any time they need it.
- Complete tasks faster and more accurately than ever before with interactive 3D guides.
- Train and onboard new employees faster with a “learning by doing” approach.
HoloLens 2 Industrial Edition is open for pre-order in select markets where HoloLens 2 is available, and shipments will begin in Spring 2021. Learn more or reach out to your Microsoft channel supplier for more details.
by Gary Mintchell | Feb 4, 2021 | Automation, Embedded Control, Technology
Twenty-plus years ago, some of the IT people where I worked and I would sometimes discuss FreeBSD, Linux, and other software at that level of servers or other compute devices. I came close to a part-time gig writing for a Linux magazine about Linux for control. I have not thought about FreeBSD for almost that long. And certainly not as the OS for an industrial controller. So this announcement from Beckhoff was one of the few that really surprise me.
TwinCAT/BSD provides an alternative operating system for all of the latest Beckhoff Industrial PC (IPC) platforms. TwinCAT/BSD combines the TwinCAT runtime with FreeBSD, an industrial-proven and reliable open-source operating system. FreeBSD is Unix-compatible and is continually being further developed, improved and optimized as an open-source project by a large group of developers.
The FreeBSD system – and thus also TwinCAT/BSD – supports ARM CPUs up to Intel Xeon processors, providing a scalable platform from small embedded controllers to high-performance IPCs. With this scalable new solution, Beckhoff presents a new operating system that combines the advantages of Windows CE – low cost and small footprint – with the numerous features of large Windows operating systems. Therefore, TwinCAT/BSD is also an alternative to Windows 7 or 10 in many applications.
The current minimum size of a basic image is around 300 MB, with very small RAM consumption of less than 100 MB. Therefore, diverse machines and systems can leverage very compact controllers with TwinCAT/BSD and use all TwinCAT 3 runtime functions. The programming still occurs on a Windows development computer and with TwinCAT 3 XAE integrated in Visual Studio®.
The new TwinCAT/BSD operating system offers multi-core support, making it possible to reserve individual cores exclusively for TwinCAT if required. In addition to a large number of FreeBSD and Linux programs, TwinCAT functions can also be installed via the Beckhoff Package Server. Moreover, uncomplicated updates of the operating system and the TwinCAT runtime are possible in this way via the network.
by Gary Mintchell | Jan 12, 2021 | Automation, Embedded Control, News, Organizations, Technology
- Artificial Intelligence coordinates multi-agent systems
- Implementing European projects on the demonstrator in Kaiserslautern
The Chief Technology Officer of a major automation supplier once told me that an important technology I should keep an eye on was intelligent agents. Indeed, the poor little software object rarely gets star billing on the program. The technology does exist. This information came to me last month about multi-agent systems. It encompasses a European smart factory initiative. This initiative bears watching.
A consortium of seventeen European partners is developing multi-agent systems for autonomous modular production in the research project called MAS4AI (Multi-Agent Systems for pervasive Artificial Intelligence to assist humans in modular production environments). The European Union (EU) has funded the project with almost 6 million euros.
MAS4AI is a project focused on selected sectors of industry that plans for their smart digital transformation over the next three years using the tools of Artificial Intelligence (AI). The aim is to achieve resilient production that can react flexibly to changing requirements or disruptions in the added value networks. The underlying basis is the large variety of products in lot size 1 in complex manufacturing operations.
Single agents acting in concert
Multi-agent systems are an area of distributed artificial intelligence research, in which several differently specialized “intelligent” and mostly autonomous software components (agents or bots) act in a coordinated manner to jointly solve a problem. The researchers are working towards the long-term goal of stable production, which among other things, relies on Shared Production and Production-as-a-Service. Communication, synchronization, and coordination of skills (production capabilities) are needed in a production network in order to implement our vision. This coordination will be performed by AI processes in the future. The European project partners envision a future production that can be distributed in European networks (like GAIA-X).
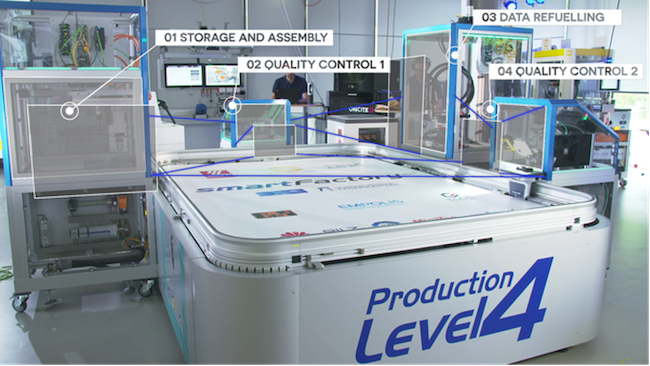
People make the decisions
Scientists and engineers from Greece, Germany, Italy, Lithuania, the Netherlands, Poland and Spain are initially working on a modular system architecture and a communication structure to create the foundation on which to integrate industrial AI services for smart production. In the process, human participants will always retain control over the AI technologies. The prerequisite for this is to have AI processes designed in a way that is always understandable to the operator. Only then can they be validated, optimized, or modified. Demonstrators oriented on a series of industrial use cases are being developed in MAS4AI. The use cases are in European industrial sectors of high added value, such as companies from the automotive industry, contract manufacturing, bicycle production, or wood processing.
Production Level 4 as the visionary basis
“MAS4AI fits perfectly into our concept of Production Level 4, which is based on production-bots and modular networks. Our concept envisions future production resources that offer their capabilities (skills) to the networks and autonomously (self-directed) call up the products,” said Prof. Martin Ruskowski, Chairman of the Executive Board of SmartFactory-KL, Head of DFKI’s Innovative Factory Systems research, and Chair of the department of Machine Tools and Controls at TU Kaiserslautern. “The products in our vision know their attributes and their current production progress. Such products search their own way among the skills to complete their own production. This may take place in a facility, but also in a Europe-wide network.”
Four scientific and technological goals
The consortium is developing the following four topics:
- Multi-agent systems for the distribution of AI components at various levels of a hierarchy. The key idea is to control interaction between agents on a task-specific basis with agents integrated to form an overall system.
- AI agents that use knowledge-based representations with semantic web technologies. Every agent can detect what skills it has to offer and those of other agents and, in this way, decide what action should be executed. This also makes it easier to integrate people into the production, because the data is also prepared in a way that is understandable to them.
- AI agents for the hierarchical planning of production processes. Processes are broken down into individual steps and optimally reassembled according to the current requirements. Disturbances in the flow can be compensated.
- Model-based AI agents for Machine Learning (ML). These hybrid models are designed to combine human knowledge about physical processes with data acquired for machines.
A fundamental concept in MAS4AI is the integration of all smart components (machines with attributes like self-direction, self-description, and self-learning abilities) in a holistic system architecture. This facilitates easy development and use of industrial AI technologies. Software developers, system integrators, and end users will all benefit because the hurdle for the use of AI is low. “We expect this to generate revolutionary ideas for business models as well as brand new market opportunities,” said Ruskowski.
Partners:
- Deutsches Forschungszentrum für Künstliche Intelligenz GmbH, Deutschland
- Nederlandse Organisatie voor Toegepast Natuurwetenschappelijk Onderzoek, Niederlande
- University of Patras – Laboratory for Manufacturing Systems & Automation, Griechenland
- Fundacion Tecnalia Research and Innovation, Spanien
- Asociacion De Investigacion Metalurgica del Noroeste, Spanien
- University of Silesia, Polen
- Volkswagen AG, Deutschland
- SCM Group Spa, Italien
- SC Baltik Vairas, Litauen
- VDL Industrial Modules, Niederlande
- Fersa Bearings S.A., Spanien
- Semaku B.V., Niederlande
- Symvouloi Kai Proionta Logismikou, Griechenland
- flexis AG, Deutschland
- Sisteplant, S. L., Spanien
- D.M.D. Computers SRL, Italien
- Smart Manufacturing Competences Centre INTECHCENTRAS, Litauen
by Gary Mintchell | Dec 23, 2020 | Automation, Embedded Control, Technology
Bringing together control, IT, and the IoT to create an open, scalable system
The idea of “softPLCs”, software-defined control, decoupling software and hardware for control, and the like revisited my thinking thanks to commenting on a paper on that subject by IoT-Analytics. In the discrete, machine automation world, this is an old topic dating back more than 22 years.
It still hasn’t happened. Yes, the marketing arms of some companies trumpet the idea. The Open Process Automation Forum is pushing the idea in the continuous and batch process world. I have yet to see any disruption occurring because of it. Some of the companies that analysts think are disruptive have been around for upwards of 30 years and the three main incumbents are still leading—Siemens in German/Italy, Rockwell Automation in North America, Mitsubishi in Asia.
That doesn’t mean the idea has been shelved completely. There must be some sort of cycle where Bosch Rexroth recurs on my radar with a new platform. I don’t understand all the parts of this new “ctrlX Automation”, but it looks interesting.
Thoughts?
These are quotes from Bosch Rexroth.
ctrlX AUTOMATION is based on a completely new software and engineering approach and means a complete departure from proprietary structures and systems. The automation platform includes all necessary software and hardware components for complete system solutions: high-performance controllers, compact drives, industrial PCs, safety solutions, I/O modules and HMIs.
ctrlX AUTOMATION enhanced with an open I/O range
The ctrlX I/O range from Bosch Rexroth offers new possibilities for users in terms of connectivity and networking. The solution represents a functional extension of the ctrlX CORE control platform and also enables horizontal and vertical integration. In the future, ctrlX I/O will offer comprehensive communication and performance enhancements as well as I/O modules geared towards future technologies such as 5G, TSN and AI.
Embedded controller ctrlX CORE now available
In addition, the embedded controller ctrlX CORE is ready to ship with the start of the fair. The modular, compact control is suitable for any automation application and, with its openness, offers users completely new degrees of freedom in setting up the functions. ctrlX CORE’s full scope of functions has already been tested by selected customers.
ctrlX SAFETY: redefining safe automation
With the safety solution ctrlX SAFETY, Bosch Rexroth is setting new standards for safe automation. The product is regarded as the fastest and most compact safety solution on the automation market. Its reaction time allows a more compact design and maximum safety during production.
ctrlX SERVICES for the automation of the future
The automation platform ctrlX AUTOMATION has recently been expanded to include ctrlX SERVICES. The ctrlX App Store now enables downloading of individually required software, while the ctrlX Device Portal facilitates easy and centralized administration of controls. The ctrlX AUTOMATION Community offers numerous functions such as support, know-how transfer and further training. Bosch Rexroth also guarantees 25 years of service availability for classic services.
ctrlX World for third party providers
Users can use apps from Bosch Rexroth, applications from third parties or apps they have produced themselves. ctrlX AUTOMATION users can access a broad portfolio of applications and download them easily via the App Store. In addition, more and more third-party providers are currently joining the ctrlX World, as they can provide their own apps on the platform and thus tap into new business potential.