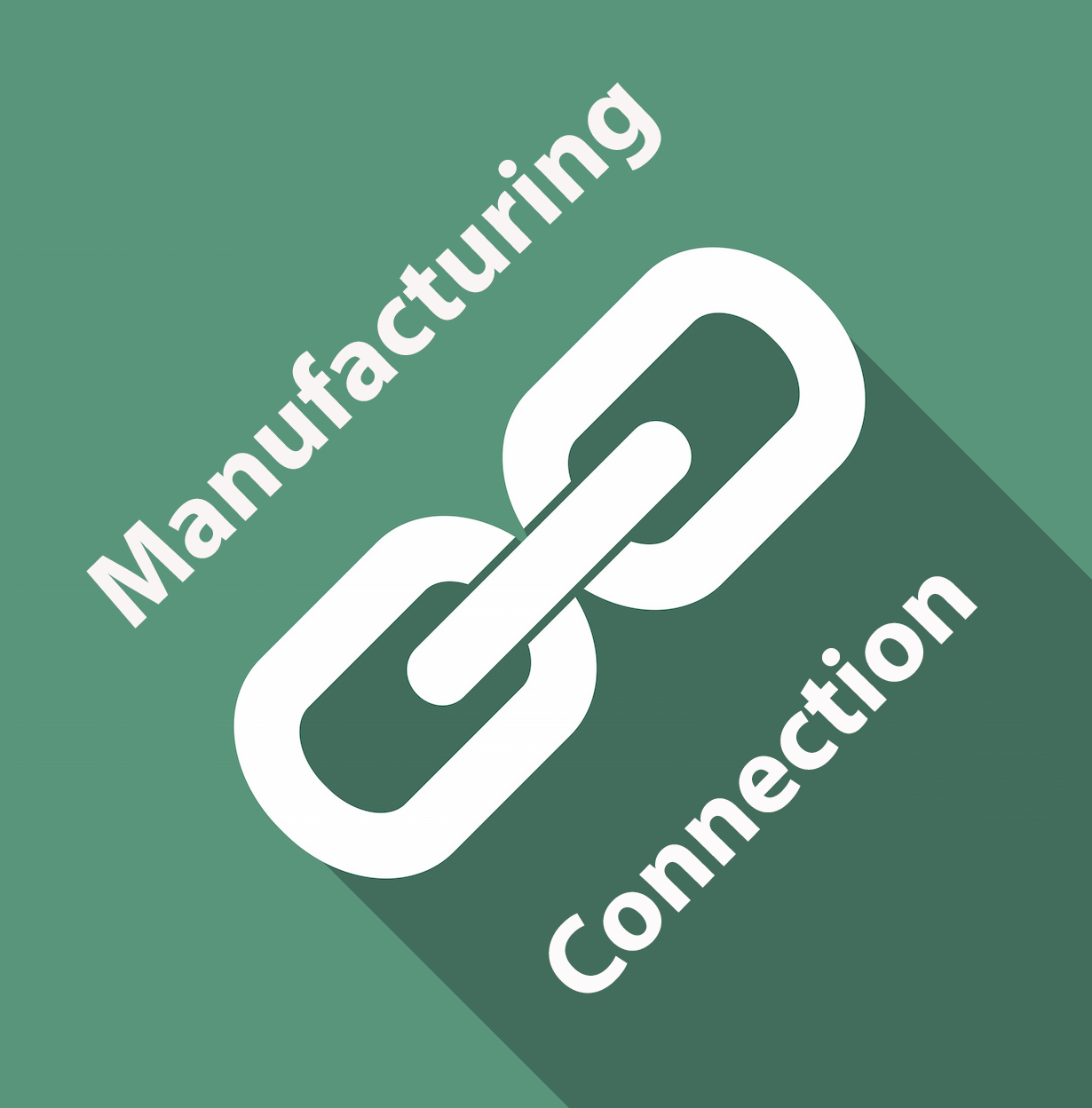
Data Drives A New Manufacturing Hero The Reliability Engineer
I chatted this week with two executives from GE Digital. Jeremiah Stone is the General Manager – Industrial Data Intelligence Software at GE Digital, and Jennifer Bennett is the General Manager – Manufacturing Software Solutions (Brilliant Factory) at GE Digital.
The conversation opened with the idea that it’s about data. Companies must become data-driven. But then it’s also beyond data. Not all data sets are equal. And it’s not just about finding anomalies–it’s really about finding that data and anomalies that matter most to business success.
Then we went a direction that I’ve never gone with GE before–remote monitoring and diagnostics (RM&D) targeted to reliability engineers. The often overlooked skillset of reliability engineers, and how their knowledge offers a distinct competitive advantage to companies battling it out in the industrial market.
As the advantages from unlocking big data insights continue to benefit enterprises of all sizes, data scientists – the gatekeepers and analysts of this data – have become an increasingly popular career choice. In fact, The Harvard Business Review proclaimed data scientists to be “the sexiest job of the 21st century.” But with more advanced Remote Monitoring and Diagnosis (RM&D) technologies being utilized to find and address problems before they happen, reducing the costs of planned and unplanned downtime, the emerging industrial superstars are reliability engineers.
This list summarizes our conversation:
- RM&D in the cloud uncovers the gap of reliability-centered maintenance and operations. This new technology shines a light on an old problem for customers– frustrations around the fact that they’re not able to executive consistently on maintenance and operations.
- Successful asset monitoring is more than just software. Organizations have a false sense of security that if they install monitoring software, they instantly have a handle on their operations. But the real secret in handling the complexity that monitoring creates with RM&D is the reliability engineers that can run and interpret the technology.
- Identifying anomalies in RM&D is not the problem. Identifying anomalies that matter to operations is the problem. RM&D create numerous alerts so it’s hard for an organization to know which ones to really focus on. Reliability engineers have the expertise to shift through the notifications and identify false positives, telling their organizations which ones to ignore and which ones to pay attention to.
- Cloud-based business strategy is becoming less about technology and more about knowledge sharing. The benefits of utilizing cloud technology are increasingly becoming centered on the fact that organizations can internally share and learn from a pooled knowledge base, no matter the location. The cloud offers a way for reliability engineers to capture and preserve knowledge that is crucial to the business’s ongoing success.
Stone said that this idea ties in to GE’s strategy itself. As disciples of Deming, the company is data driven, and a lot of that means remote monitoring and diagnostics for GE’s fleet. Incorporating technologies such as those from the SmartSignal acquisition, company engineers and managers are now excited. With the RM&D, they now can execute on goals, avoid failure, achieve greater reliability, and be more proactive. “Now we are excited to bring tools we use to the rest of the industrial world.”
Today’s RM&D enables excellence in manufacturing from a larger, systemic view, in order to deliver business advances, added Stone. Now engineers and managers can look at the entire scope/span of problem, not just one process or loop. “We help companies on the journey beginning with an assessment of where they are and what they want to achieve. We offer professional services to help them figure out what are outcomes they want to achieve. Not just getting connected to get data but doing it in a way that makes sense.”
Bennett pointed to the variety and complexity of data. “The problem has been all data has been in silos, but the value is upstream and downstream. Some challenges in manufacturing are often quite complex. Data flows from contexts requiring tracking back to cause. The platform we’re building on Predix brings data together. We can make insightful decisions. In RM&D we’re looking at history records, maintenance records, and the like. In the past we relied on people who have knowledge and experience for data. Now we can combine and analyze.”
We started discussing workforce and the challenges of recruiting and retaining younger people. Stone noted that young people today are looking for autonomy, mastery, and purpose. “What was magic 20 years ago isn’t now. We find a sense of curiosity in new people and a desire for a job with meaningful impact.”
One improvement in the job situation is the ability to spend more time problem solving and less time gathering data. According to studies, a typical data and analytics project required 80% of the time just collecting and collating data. Stone noted, “Our focus is on dramatically minimizing amount of time to get the data so people can start moving toward problem solving and analytics. Traditionally reliability engineers have been frustrated by availability of data. We are talking about taking it from calendar time to wrist watch time. Then we give collaborative capability. Both newer and more senior engineers are delighted with this new possibility to spend more time problem solving.”