by Gary Mintchell | Dec 16, 2019 | Networking, Standards
Sander Rotmensen of Siemens automotive test center in Nuremberg, Germany and Yongbin Wei of Qualcomm recently discussed the birth of 5G networks for industrial applications. The occasion concerned the press release announcing implementation of a 5G private industrial network.
We’ve all heard about 5G and worries from a variety of national governments about whether another country is embedding spy firmware in its local company’s products. Personally, I think the worry is both silly and well-founded. Every country that houses a company in the market most likely has intelligence agents trying to do the same thing. (I could go into my university education and acquaintance with a professor with “former” CIA ties, but that goes too far afield.) And all companies will deny any tie.
And…we are going to use 5G because the benefits are great. A benefit everyone mentions is the ability to build private networks for a local facility. The network has very low latency and built-in 5-9s (99.999%) uptime.
And what are some of the use cases we can anticipate? Rotmensen and Wei provided a list of ideas:
- Mobile equipment (tablets, etc.)
- Assisted Workers (remote video/audio to experts, etc.)
- Backhaul depending upon geography
- Autonomous machines–robots, cobots with communication and low latency
- Autonomous logistics
- Edge computing, larger amounts of data with low latency
With the final release of IEEE Time Sensitive Networking still years away, 5G is looking very good. We are on release 15 presently. Release 16 is anticipated in June, 2020. With release 17, the increased capacity would easily handle pretty dense machine-to-machine and IoT applications.
First Private Standalone Industrial 5G Network
Showing the benefits of today’s trend toward cooperation and partnerships, this joint proof-of-concept network will explore the capabilities of 5G standalone networks for industrial applications.
The private 5G standalone (SA) network in a real industrial environment uses the 3.7-3.8GHz band. Both companies have joined forces in this project: Siemens is providing the actual industrial test conditions and end devices such as Simatic control systems and IO devices and Qualcomm is supplying the 5G test network and the relevant test equipment.
The 5G network was installed in Siemens’ Automotive Showroom and Test Center in Nuremberg. Automated guided vehicles are (AGV) displayed here which are primarily used in the automotive industry. New manufacturing options and methods are also developed, tested and presented before they are put into action on customer sites. This allows Siemens’ customers, such as automated guided vehicle manufacturers, to see the products interact live.
The Automotive Showroom and Test Center enables Siemens and Qualcomm to test all the different technologies in a standalone 5G network under actual operating conditions and to come up with solutions for the industrial applications of the future. Qualcomm Technologies installed the 5G test system comprising infrastructure and end devices in less than three weeks. Siemens provided the actual industrial setup including Simatic control systems and IO devices.
“Industrial 5G is the gateway to an all-encompassing, wireless network for production, maintenance, and logistics. High data rates, ultra-reliable transmission, and extremely low latencies will allow significant increases in efficiency and flexibility in industrial added value,” says Eckard Eberle, CEO Process Automation at Siemens. “We are therefore extremely pleased to have this collaboration with Qualcomm Technologies so that we can drive forward the development and technical implementation of private 5G networks in the industrial sector. Our decades of experience in industrial communication and our industry expertise combined with Qualcomm Technologies’ know-how are paving the way for wireless networks in the factory of the future.”
“This project will provide invaluable real-world learnings that both companies can apply to future deployments and marks an important key milestone as 5G moves into industrial automation,” said Enrico Salvatori, Senior Vice President & President, Qualcomm Europe/MEA. “Combining our 5G connectivity capabilities with Siemens’ deep industry know-how will help us deploy technologies, refine solutions, and work to make the smart industrial future a reality.”
The German Federal Network Agency has reserved a total bandwidth of 100 MHz from 3.7 GHz to 3.8 GHz for use on local industrial sites. German companies are thus able to rent part of this bandwidth on an annual basis and to make exclusive use of it on their own operating sites in a private 5G network whilst also providing optimum data protection. Siemens is using this principle to evaluate and test industrial protocols such as OPC UA and Profinet in its Automotive Showroom and Test Center together with wireless communication via 5G.
by Gary Mintchell | Oct 23, 2019 | Automation, Commentary, Process Control, Security
I’ve followed Foxboro and Triconex for many years now in my coverage of the process automation business. A great company that, not unlike too many others, suffered now and again with very poor management. The company has now settled in nicely at its home in Schneider Electric and appears to be healthy here.
Much credit must go to Gary Freburger. He provided a steadying hand as the leader before and through the transition, as well as guiding the integration into the new home. He is retiring at the end of the year. I’ve met a number of great leaders and a few stinkers in my 20 years at this side of the business. Gary’s one of the great ones. And his chosen successor (see more below) seems more than up for the task of building on his successes.
Marcotte Succeeds Freburger as Process Automation President
This week’s major announcement revealed that Nathalie Marcotte has been selected to succeed Freburger as president of its Process Automation business, effective Jan. 1, 2020.
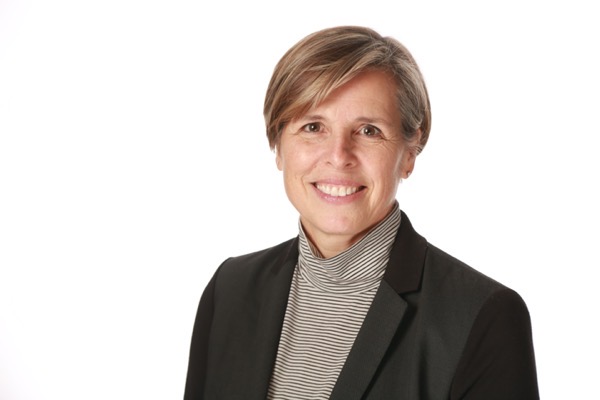
“After a long, successful industry career, including more than 15 years serving Invensys and Schneider Electric in various senior leadership roles, Gary has decided to retire,” said Peter Herweck, executive vice president, Industrial Automation business, Schneider Electric. “We thank him for his many contributions and his strong legacy of success. We wish him well, and I congratulate Nathalie on her appointment. She brings more than 30 years of industry knowledge, expertise and experience, as well as a long record of success. I look forward to working with her as we build on the success Gary has delivered.”
Since joining the Schneider organization in 1996, Marcotte has held several positions of increasing responsibility, including vice president of Global Performance and Consulting Services; vice president, North America marketing; general manager for the Canadian business; and, prior to her current position, vice president, marketing, Global Systems business. As the company’s current senior vice president, Industrial Automation Services, she is responsible for Schneider Electric’s Services business and offer development, ranging from product support to advanced operations and digital services. She is also responsible for the company’s Global Cybersecurity Services & Solutions business, including the Product Security Office.
“As we move through this transition, it will be business as usual for Schneider Electric and our Process Automation customers,” Marcotte said. “Gary and I are working very closely together to ensure there will be no disruptions to our day-to-day operations. This ensures our customers have the same access to the exceptional people, products and technology they have come to trust and rely on to improve the real-time safety, reliability, efficiency and profitability of their operations.”
“I thank Gary for his many contributions to Schneider Electric and to our industry in general. Under his leadership, our customers, partners and employees have never been better situated to succeed, today and tomorrow,” Marcotte said. “This transition will have no impact on our technology strategy and portfolio roadmap. We remain committed to our continuously-current philosophy, which means never leaving our customers behind. Now, by leveraging the strength of the full Schneider Electric offer, we can take the next step toward enabling an easier, less costly digital transformation for our customers, while keeping them on the path to a safer, more secure and profitable future.”
Following the opening keynotes, I had the opportunity to chat privately with Freburger and Marcotte. Following summarizes a few key takeaways.
Digitalization and Digital Transformation.
These topics were prominently displayed in the ballroom before the keynotes. In fact the welcome and opening presentation were given by Mike Martinez, Director of Digital Transformation Consulting. These are common themes in the industry—in fact, not only process automation, but also at the IT conferences I cover. Each company has its own unique take on the terms, but it still boils down to data, data integrity, databases, and data security. All of which were discussed.
Key Points From the Presidents.
Integration across Schneider Electric. One priority has been working with other business units (and their technologies) across the Schneider Electric portfolio. This could be PLCs and drives, but power is a huge emphasis. Schneider Electric management wants very much for its process automation acquisition to integrate well with its historic electric power business. This is seen as a strategic opportunity. One thought-provoking observation—is the process engineer/electrical engineer divide as serious as the IT/OT divide? No direct answer. But these domains have historically had little to no collaboration. One to watch.
Close working relationship with AVEVA. If you recall, Schneider Electric bundled its various software acquisitions including the ones from Invensys (Wonderware, Avantis) and used them to buy into AVEVA—the engineering software company. Bringing automation and software together was a constant source of pain for Invensys. Schneider Electric dealt with it through a separate company. Along the way, cooperation seems to be better than ever. Marcotte explained to me that Foxboro combines its domain expertise with the more broadly general software platforms to achieve customer values. See for example my previous post on Plant Performance Advisors Suite.
Cybersecurity. Marcotte has been leading Schneider’s cybersecurity efforts. These are seen as a key part of Schneider Electric’s offer. See especially the establishment of the ISA Global Cybersecurity Alliance. They don’t talk as much about Internet of Things as at other conferences, when I probed more deeply about IT, cybersecurity was again brought up as the key IT/OT collaboration driver.
It’s been a struggle, but the Schneider Electric process automation business (Foxboro and Triconex) seems as strong as ever. And the people here—both internal and customers—are optimistic and energetic. That’s good to see.
by Gary Mintchell | Jul 25, 2019 | Commentary, News, Security
The International Society of Automation (ISA) held a press conference today to announce the first Founding Members of its new Global Cybersecurity Alliance (GCA): Schneider Electric, Rockwell Automation, Honeywell, Johnson Controls, Claroty, and Nozomi Networks.
As we would expect, the speakers emphasized the importance of standards as the foundation for work in the Alliance. Speakers also tied in safety and productivity as partners with cybersecurity in protecting and improving manufacturing and critical infrastructure facilities and processes. I’m not so sure just exactly what the Alliance will accomplish, but if it succeeds in just raising awareness and a sense of urgency among companies it the industries, it will have accomplished an important task.
ISA created the Global Cybersecurity Alliance to advance cybersecurity readiness and awareness in manufacturing and critical infrastructure facilities and processes. The Alliance brings end-user companies, automation and control systems providers, IT infrastructure providers, services providers, and system integrators and other cybersecurity stakeholder organizations together to proactively address growing threats.
ISA is the developer of the ANSI/ISA 62443 series of automation and control systems cybersecurity standards, which have been adopted by the International Electrotechnical Commission as IEC 62443 and endorsed by the United Nations. The standards define requirements and procedures for implementing electronically secure automation and industrial control systems and security practices and assessing electronic security performance. The standards approach the cybersecurity challenge in a holistic way, bridging the gap between operations and information technology.
Leveraging the ISA/IEC 62443 standards, the Global Cybersecurity Alliance will work to increase awareness and expertise, openly share knowledge and information, and develop best practice tools to help companies navigate the entire lifecycle of cybersecurity protection. The Alliance will work closely with government agencies, regulatory bodies, and stakeholder organizations around the world.
“Accelerating and expanding globally relevant standards, certification, and education programs will increase workforce competence, and help end users identify gaps, reduce risks, and ensure they have the tools and systems they need to protect their facilities and installations,” said Mary Ramsey, ISA Executive Director. “Through the proliferation of standards and compliance programs, we will strengthen our global cyber culture and transform the way industry identifies and manages cybersecurity threats and vulnerabilities to their operations.”
The press release notes that first Founding Members of the Alliance are leading multi-national, industrial-technology providers with deep expertise in technology and applications, and they’ll apply their experience and knowledge to accomplish the Alliance’s priorities. However, two of the members were represented by building automation divisions. Two of the members are cybersecurity suppliers. Rockwell Automation is a pure play factory and process automation company and its Maverick Technologies division has been an ardent supporter of ISA. Schneider Electric is a large, multi-disciplined company, and I’m not sure which division within it is the sponsor.
“Participating in the Alliance truly shows the commitment our founding members have to the safety and security of the industrial ecosystem, as well as the criticality of collectively moving forward together to ensure the standards, best practices and methods are applied,” Ramsey said.
“ISA engaged with discussions, initiated by Schneider Electric, to create an ISA-led global, open and industry-wide alliance comprised of all cybersecurity stakeholder companies. ISA quickly expanded those conversations to include Rockwell Automation, Honeywell, Johnson Controls, Claroty, and Nozomi Networks. These first Founding Members have since worked together to help us define the Alliance’s objectives. We are thankful for their collaboration and commitment. Together we welcome companies and organizations from all segments of industry to join our efforts.”
The Alliance is seeking additional members to support its initiatives. End-user companies, asset owners, automation and control systems providers, IT infrastructure providers, services providers, and system integrators and other cybersecurity stakeholder organizations are invited to join. Annual contributions to fund initiatives are based on company revenues and are tax-deductible.
Perspectives: Quotes from the ISA Global Cybersecurity Alliance Founding Members
“Over the last few years, global industry has recognized that taking on increasingly dangerous cyber risks can’t be limited to a single company, segment, or region. However, until now, there has been limited ability to respond as a unified whole to these worldwide threats. But by establishing an open, collaborative, and transparent body, with a focus on strengthening people, processes, and technology, we can drive true cultural change. We are pleased that ISA has stepped forward, and we look forward to working openly and collaboratively with them, our fellow Founding Members, and many others affiliated with global industry, especially end users. Together we will bring to bear the standards-based technology, expertise, and special skills required to better secure and protect the world’s most critical operations and the people and communities we serve.” — Klaus Jaeckle, Chief Product Security Officer, Schneider Electric
“Cybersecurity is critical to digital transformation. It’s critical not only for the protection of information and intellectual property, but also for the protection of physical assets, the environment, and worker safety. We make it a priority to collaborate with partners and research institutions to develop secure products. Rockwell Automation participated in the development of the 62443 standards from the beginning and continues to support ISA cybersecurity initiatives. Our engagement with the Global Cybersecurity Alliance will be another important step in our efforts to help customers identify and mitigate risks.” — Blake Moret, CEO, Rockwell Automation
“Cybersecurity is the great equalizer to all companies. It’s critical to the connected world we live in and the cornerstone of trust that the world needs to be able to operate. Whether protecting critical infrastructure or managing a building’s operations, users need to do this with the confidence the employed systems are robust and secure. We are committed to and proud to work together ISA and the GCA members to continue to drive the adoption of the ISA/IEC 62443 series of standards and identify further ways to secure and protect the connected world which we live. At Honeywell, we see cybersecurity as a core part of the future we are making, and we see the GCA as an important way to work together to make that happen.” — Matthew Bohne, Vice President and Chief of Product Security, Honeywell Building Technologies
“Digital transformation in the building sector continues to accelerate, which heightens the urgency for cybersecurity across the industry and beyond. As a leader in the industrial automation controls business, Johnson Controls is already a strategic member of the ISASecure program and is consistently taking proactive actions to protect customers against cyber-threats and risks. Joining ISA Global Cybersecurity Alliance is a necessary and meaningful step as it supports our company values, customer adoption of the ISA/IEC 62443 standard and efforts to educate global government and regulatory bodies. We are proud to solidify our commitment to this important effort.” — Jason Christman, Vice President, Chief Product Security Officer, Global Products, Johnson Controls
“One of the most effective ways to drive consistency in an industry is by putting standards in place, and we’re looking forward to collaborating with all of these founding members, as well as future Alliance members, to help drive global best-practices forward in this historically standard-less environment. Claroty is committed to the mission of protecting all IoT and OT networks from cyber risks. Through our work with the Global Cybersecurity Alliance, we will be able to help shape the future of cybersecurity in these high-risk industries.” — Dave Weinstein, Chief Security Officer, Claroty
“Nozomi Networks believes real community collaboration, actionable standards and effective education are key ensuring a secure future for industrial organizations around the world. That’s why we are helping develop secure-by-design standards as a working member of ISA99 standards committees, why we’ve designed our industrial cyber security solutions for easy integration across the broadest possible set of industrial and IT technologies; and why we are thrilled to help establish the Global Cybersecurity Alliance. Together we will build a secure future for the industrial infrastructure that runs the world.” — Andrea Carcano, Nozomi Networks Co-founder and Chief Product Officer
by Gary Mintchell | Jun 28, 2019 | Automation, News, Security
Industrial Automation. I guess sometimes it’s good and sometimes not. Tesla had difficulty ramping up production on its low-end vehicle. Elon Musk blamed automation for his problems. Well maybe it was vaguely automation. But maybe they tried automating too much, or they automated things they shouldn’t have. Maybe Rockwell Automation now has a place he can drive to to learn more about automating production.
While I was traveling, Rockwell Automation released some news. I had to seek clarification on some. Here are two interesting items.
The first piece of news concerned Rockwell Automation opening an 8,000 square-foot Electric Vehicle (EV) Innovation Center at 111 North Market Street in San Jose, California, within its Information Solutions development facility. The center will provide live manufacturing demonstrations, hands-on trials utilizing new technology and events showcasing collaboration with industry experts and Rockwell Automation partners.
Upon first glance I thought maybe it was getting into the EV business. Actually it is bringing its experience and products from “Detroit” building cars to Silicon Valley building cars—just with different power trains.
Utilizing augmented and virtual reality modeling, the EV Innovation Center provides automotive start-ups and established manufacturers an environment to learn new technologies and standards, enabling them to deliver electric vehicles to market faster, with less risk and at lower cost.
The Center features not only traditional Rockwell products, but also features partners such as its FactoryTalk InnovationSuite powered by PTC, Eagle Technologies’ battery pack assembly machine, and FANUC robot technologies.
Other partners featured include Hirata, a turnkey assembly line builder, provides an assembly cell that demonstrates electric drive unit assembly and testing; Emulate 3D, Rockwell Automation’s simulation software, helps to prototype and test machines before they’re built; teamtechnik performs functional testing to confirm performance before building the drive into the electric vehicle.
“With growing global consumer demand, electric vehicle companies are challenged to meet aggressive production timelines,” said John Kacsur, vice president, Automotive and Tire Industries, Rockwell Automation. “We established the Electric Vehicle Innovation Center to expand their possibilities and get their products to consumers quickly and at the lowest possible cost, while operating more efficiently.
The second Rockwell news concerns its partner Claroty and cybersecurity services. To help prevent incidents and combat the unpredictable threats that cause them, industrial companies around the world can now manage cyber risk in their operations using the Rockwell Automation Threat Detection Services powered by the Claroty threat detection platform.
“A scary aspect of security threats is what you don’t know about them – what techniques they’ll use, what attack vector they’ll leverage, what vulnerabilities they’ll exploit,” said Umair Masud, manager security services portfolio, Rockwell Automation. “Our Threat Detection Services combine our innate understanding of industrial automation with Claroty’s trusted OT network visibility. The services can give companies peace of mind by protecting not only one facility but their entire supply chain from unpredictable threats.”
The Threat Detection Services help safeguard connected operations in three key ways:
- Identify and Protect: Identifying all industrial control networked assets, and their vulnerabilities, to help companies know what to protect
- Detect: Monitoring networks for not only known threats but, more importantly, anomalous traffic or behaviors to alert companies of a security incident – possibly before it even happens
- Response and Recovery: Developing plans for containing, eradicating and recovering from attacks to keep operations running or more quickly return to a fully operational state
The Claroty threat detection platform creates an inventory of a user’s industrial network assets, monitors traffic between them and analyzes communications at their deepest level. Detected anomalies are reported to plant and security personnel with actionable insights.
“The Claroty platform, used within the Threat Detection Services, can accelerate a company’s journey to more connected and digitally driven operations,” said Amir Zilberstein, co-founder and CEO, Claroty. “Most critically, the platform can help companies detect and quickly respond to threats that bypass their security controls. But it can also give companies a deeper understanding of their industrial assets and improve their ability to keep operations running.”
by Gary Mintchell | Jun 11, 2019 | Automation, Events, Manufacturing IT, News, Process Control
My wife’s family took me off for a week-long vacation to the beach last week. Eight days of much needed rest after a bunch of travel and a hectic (meaning wet) spring soccer season.
Last week was also Rockwell Automation TechED. That conference was once open only to distributer and integrator tech people. Several years ago it opened to media and became quite a thing for a few years. Last year I received an invitation to attend but they said that there was no media program. The timing was bad for me, so I passed. This year, there was no word at all. And I saw no news.
There are several industrial automation user conferences this week. PTC invited me to its conference in Boston. Then I was invited to Honeywell User Group (HUG). Then there were other invitations. Busy week. I initially told PTC I would attend, then putting it in my calendar, I realized that the week included my wedding anniversary. It’s big number (as in large). My better sense prevailed and I’m watching both of those conferences from afar.
So far this week, Honeywell Process Solutions has made a big announcement with some innovative product releases. Rockwell Automation, which owns about 8% of PTC and is banking on the partnership to bring its software into the new age, also issued a release. I’m still figuring that one out.
Honeywell Proclaims New Approach to Engineering
• Experion PKS Highly Integrated Virtual Environment (HIVE) significantly simplifies control system design, implementation and lifecycle management while reducing cost
• Market-first solution uniquely decouples the assignment of input/output (IO) modules and control strategies from specific controllers, and leverages IT capabilities in customers’ own data centers
My take on this announcement considers the HIVE product suite part of the growing trend under the umbrella of “digital twin.” Other companies have some somewhat similar products, but what I’ve found is that each company moves the ball forward a little more in a seemingly endless cycle of innovation. Honeywell labels it an evolution of the company’s flagship Experion Process Knowledge System (PKS).
Experion PKS HIVE uses Honeywell’s LEAP project execution principles, software, and networking to unchain control applications from physical equipment, and controllers from physical IO. This enables control systems to be engineered and implemented in less time, at lower cost and risk, and with simpler, modular builds. The solution also transforms the way control systems are maintained over their lifecycle, shifting day-to-day management of servers to a centralized data center, where experts and established protocols mitigate cybersecurity risk, allowing plant engineers to focus more proactively on optimization of their control systems.
Experion PKS HIVE incorporates three elements – IT HIVE, IO HIVE and Control HIVE – which can be used individually or collectively, in tandem with customers’ existing systems and infrastructure:
• Experion PKS IT HIVE centralizes up to 80% of the IT infrastructure traditionally used in project engineering to lower project delivery and lifecycle costs, better leverage skills, and drive consistent physical and cybersecurity management across an enterprise.
• Experion PKS IO HIVE provides flexible IO and control distribution enabling the control system to become a natural extension of process equipment and to facilitate modular and parallel project execution.
• Experion PKS Control HIVE uniquely applies control containers to provide flexibility and standardization of control hardware platform, control location, and control engineering. With multiple physically controllers operating as part of a Experion PKS Control HIVE, control engineering is dramatically simplified through automated load balancing.
“In developing Experion PKS HIVE, Honeywell worked closely with customers across the chemical, refining and oil and gas industries,” said Jason Urso, chief technology officer, Honeywell Process Solutions. “Many of these organizations want a more efficient approach to control system engineering, yet one that can be adopted incrementally and used interchangeably with their existing systems and infrastructure. Experion PKS HIVE provides these benefits and is truly a distributed control as it applies and geographically distributes technology to where it is needed.”
Experion PKS HIVE shifts IO to the field and makes it fully accessible to any controller, taking individual physical controllers and distributing the load so that they appear as a single controller to eliminate complexity. The solution distributes IT compute from onsite to offsite providing a seamless operations experience.
The Experion PKS IT HIVE and IO HIVE can be ordered now, with deliveries beginning Q1 2020. Experion PKS Control HIVE will be available in the second half of 2020.
Rockwell Automation Emphasizes PTC Partnership
Rockwell Automation announces its “unique combination of IT and OT software accelerates customers’ Digital Transformation Initiatives.” It says its solutions-oriented approach simplifies how manufacturers achieve business outcomes that transform operational processes, workforce productivity and efficiency.
Showcasing solutions during LiveWorx this week the company highlights:
Enterprise Operational Intelligence – cuts manufacturing costs and increases flexibility and agility of manufacturing networks by providing real-time manufacturing performance management across the industrial enterprise.
Digital Workforce Productivity – heightens productivity, improves quality, and avoids safety and compliance risk by equipping workers with actionable, augmented intelligence.
Intelligent Asset Optimization – reduces downtime and maximizes asset utilization through real-time monitoring, diagnostics, and predictive and prescriptive analytics into asset capacity, performance, and health status.
Scalable Production Management – lowers cost of inventory, improves quality, and compliance and accelerates time to market with effective planning and control of production processes.