by Gary Mintchell | Nov 8, 2019 | Automation, Technology
Artificial Intelligence, or AI, is not necessarily the dystopian technology portrayed in books and movies. Although neither artificial or intelligent, AI can be a powerful tool in the engineer’s kit.
Recently Carl Palme of Neurala chatted with me introducing the company and what it means by AI in its vision systems. We both have some sheet metal work in our backgrounds, so we found common cause with one of the powerful applications—finding small surface anomalies.
There is also company news. In short:
- IHI Corporation Selects Neurala to Enable Industrial Visual Inspection and Analysis Powered by AI
- One of the Largest Global Heavy-Industry Manufacturers Partners With Leader in Automated Visual Inspections to Build Vision AI-Powered Industrial Solutions
AI-powered visual inspection pioneer Neurala announced a partnership with IHI, one of the largest manufacturers in the world.
IHI is a leading producer of aircraft engines and turbochargers for vehicles and industrial machines, along with additional transport-related machinery and more. Neurala’s automated visual inspection platform will be deployed as a key component of IHI’s workflow, improving manufacturing optimization and enabling more efficient industrial inspections.
“Automation is an area of critical focus as we further strengthen our reputation as the leading manufacturer of transport-related machinery worldwide,” said Ms. Nobuko Mizumoto, Director of IHI Corporation. “Today, we are collecting data on our workflow that needs to be carefully analyzed. AI-assisted data analysis is the future of manufacturing processes, and Neurala has the industrial and manufacturing inspection expertise we require in an AI solution. As we lead IHI into Industry 4.0, we are proud to partner with Neurala to deploy a reliable AI that can function in settings that are subjective and change rapidly, without requiring any downtime on our production lines.”
IHI will leverage Neurala’s automated visual inspection platform to review product and workflow processes, cementing its reputation as a leader in safety and efficiency. AI-powered inspections allow manufacturers to accelerate new initiatives without sacrificing a gold standard of quality workmanship. IHI will use Neurala’s Brain Builder, the first cost-effective AI tool that allows users to build, deploy and analyze custom vision AI solutions with instant feedback on performance. Brain Builder simplifies the process and reduces the time to deployment in subjective settings, using on-the-fly learning to increase accuracy as the user adds data.
“We are thrilled to partner with IHI as we illustrate the critical role AI will play in manufacturing, improving efficiency in a field in which optimization is essential,” said Massimiliano Versace, co-founder and CEO of Neurala. “We look forward to building upon our strong presence in the APAC region through an industry leader like IHI. IHI selected Neurala to bolster its offerings as the industrial sector continues to evolve; our partnership will demonstrate the value of implementing AI to solve challenges of visual inspection on factory floors and to improve automation.”
Neurala is the company behind Brain Builder: a SaaS platform that dramatically reduces the time, cost and skills required to build and maintain production-quality custom vision AI solutions. Founded in 2006, Neurala’s research team invented Lifelong-DNN (L-DNN) technology, which reduces the data requirements for AI model development and enables continuous learning in the cloud or at the edge. Now, with customers in the industrial, drone, robotics, and smart devices verticals, Neurala’s technology has been deployed on 53 million devices globally.
by Gary Mintchell | Sep 5, 2018 | Automation, Technology
Humans are still essential for many manufacturing processes. Especially for assembly. But assuring the correct parts go in the assembly in the correct orientation is essential. Enter an augmented reality (AR) tool to help.
Light Guide Systems partnered with information technology company HP Inc. to release a tech tool an augmented reality (AR) dubbed Light Guide Stratus. Leveraging Sprout Pro computing platform by HP, Light Guide Stratus provides a flexible, adaptable benchtop platform for assembly processes.
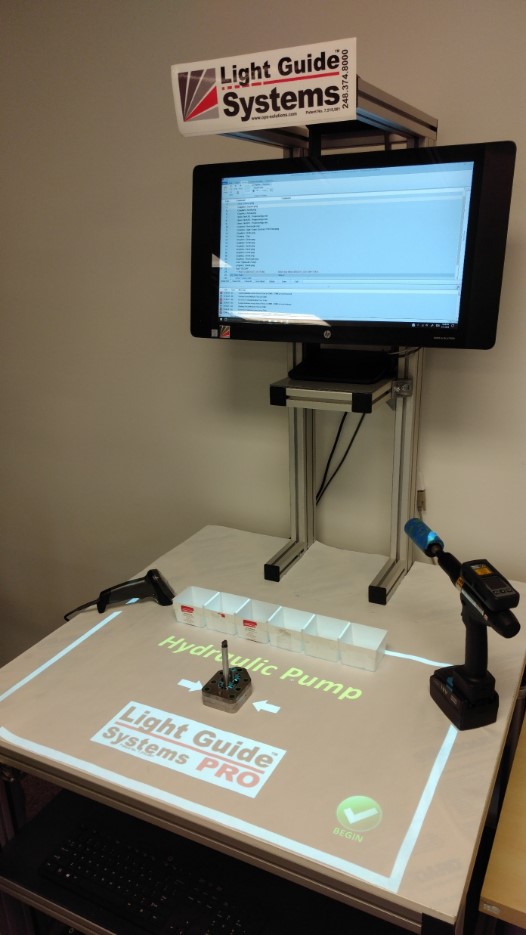
Light Guide Stratus builds on the company’s initial product Light Guide Systems Pro, which launched in 2016. The Stratus system integrates the Sprout Pro directly into a bench structure to increase the display surface area and free up critical space on the workstation. This expanded workspace can be used to integrate new types of applications and tools for a particular assembly sequence.
“The launch of Light Guide Stratus is a testament to the growing demand for flexible and powerful AR guidance systems,” said Paul Ryznar, OPS Solutions founder, president and CEO. “We knew that Light Guide Systems Pro brought a critical level of functionality and flexibility to improve outcomes for nearly any industry. We expect Light Guide Stratus to address even more applications and become an integral part of assembly and manufacturing operations for companies in every space, from medical to auto to aerospace and energy.”
Light Guide Systems projects a digital operating “canvas” onto virtually any work surface to provide audio and visual prompts, guidance, pacing, and direction. Light Guide Systems Pro takes the tool to the next level by incorporating its proprietary software into the Sprout Pro PC platform. Light Guide Stratus takes user experience into account with a flexible and repeatable design that opens up the workspace.
“HP’s Sprout Pro with Light Guide Systems reduces training time and improves quality in manufacturing assembly through projection and scanning in an augmented reality platform,” said Louis Kim, vice president and general manager of Immersive Computing, HP Inc. “Light Guide Stratus demonstrates the flexibility of the Sprout Pro platform combined with Light Guide’s innovation and leadership.”
by Gary Mintchell | Dec 7, 2017 | Automation, Internet of Things, Operations Management, Safety, Wireless
An enterprise computing and IT infrastructure company user event seems a weird place for a discussion of the Internet of Things and the Refinery of the Future. But there I was moderating a bloggers’ Coffee Talk with Doug Smith, CEO, and Linda Salinas, plant manager, of Texmark Chemicals, along with an executive of Hewlett Packard Enterprise (HPE) and one from PTC (ThingWorx).
HPE invited me to Madrid, Spain, (and paid my expenses) as an Operations Technology blogger to participate in Influencer sessions, interview a number of technologists, and experience its Discover Madrid user conference. Several times during each of the three days November 28-30 we participated in coffee talks. These were Live Streamed by Geekazine. This is a link to the first day. My session was toward the beginning of the first day, and I appear at the end of day three.
Telling the IoT Story
Texas toll manufacturer Texmark Chemicals teamed with HPE and Aruba to build a Refinery of the Future featuring advanced IIoT capabilities. The results: better process analytics, increased up-time, uninterrupted productivity, satisfied customers, and safer workers.
Every IoT implementation I have seen so far relied on predictive maintenance as the justifying application. Here, the first priority was safety. Then came predictive maintenance, improved operations, and consistent quality.
Texmark produces dicyclopentadiene (DCPD), a polymer precursor for everything from ink to boats. DCPD manufacturing processes involve flammable materials requiring stringent safety measures — and as demand increases, so does the complexity of the supply chains that rely on it.
Its manufacture involves heat and highly reactive chemicals, making safety a top priority. And as demand for DCPD grows, the global supply chain becomes increasingly complex, requiring ever more stringent controls, granular visibility, uninterrupted productivity, and regulatory oversight. Texmark must ensure its workers adhere to Process Safety Management (PSM) procedures at all times, and that its facility is managed in ways that put worker and community safety first.
As a contract manufacturer, Texmark must be prepared to adapt to customer requirements, which can change with little advance warning.
And it must continually drive plant efficiency and productivity. Historically, Texmark has depended on physical inspections of process equipment to ensure all systems remain in working order. However, these plant walk-downs can be time-consuming and labor-intensive. Texmark has 130 pumps in its plant, and spends nearly 1,000 hours a year on walk-downs and vibration analysis.
Depending solely on physical inspections also carries risk, because it relies on employees who — based on years of experience — can tell if a pump is starting to malfunction by recognizing slight variations in its noise and vibrations. But what happens if an employee with that skill is out sick, or reaches retirement age? Texmark needs ways to institutionalize that type of intelligence and insight.
Texmark’s vision for next-generation worker safety, production and asset management hinges on the emerging promise of the Industrial Internet of Things (IIoT): sensored devices combined with advanced analytics software to generate insights, automate its environment, and reduce the risk of human error.
The IIoT architecture must eliminate the need to transmit device data over a WAN, but instead support analytics at the edge to deliver real-time visibility into equipment and processes.
Texmark launched a multi-phase project to implement an end-to-end IIoT solution. Phase 1 and 2 established the digital foundation by enabling edge-to-core connectivity. Aruba deployed a secure wireless mesh network with Class 1 Div 1 access points and ClearPass for secure network access control. Aruba beacons provide location-based services for plant safety and security purposes. The wireless solution cost about half of what it would have cost to deploy a hardwired network.
For its edge analytics, Texmark selected the HPE Edgeline Converged IoT platform, an industrialized solution that supports robust compute capabilities. HPE Pointnext implemented the system as an HPE Micro Datacenter, which integrates its compute and networking technology within a single cabinet. HPE also upgraded Texmark’s plant control room to enable seamless edge-to-core connectivity and high-speed data capture and analytics, and to meet Texmark’s safety and security standards. The Edgeline system runs Texmark’s Distributed Control System software, integrating its operations technology and IT into a single system.
Phase 3 builds on the foundation established by these technology solutions to support Texmark’s use cases: predictive analytics, advanced video analytics, safety and security, connected worker, and full lifecycle asset management.
Texmark’s new IIoT solution will help make its workers even safer. It can monitor fluid levels, for example, reducing the risk of spills. It can alert Texmark immediately if a system starts to malfunction, enabling the company to respond before workers or production are endangered. And in the event of an emergency, it can help protect workers by ensuring Texmark knows their precise location and movements within the facility.
Other benefits will improve the company’s bottom line. Texmark can use data from IIoT sensors to identify which systems require hands-on evaluations, for example, so it can conduct physical inspections in a more focused and efficient manner.
The new IIoT solution makes it easier for the company to plan inspections and maintenance. To work on distillation columns, Texmark must often take systems offline and erect costly scaffolding. Improved maintenance planning will reduce these associated costs by at least 50%.
by Gary Mintchell | Nov 21, 2016 | Automation, Motion Control
This post regarding magnetic encoders is not my typical news. I met with the company at Automation Fair a couple of weeks ago. It’s the newest thing I’ve heard in encoders in a while. Thought I’d pass it along for all you servo engineers and business development managers out there.
POSITAL’s new family of kit encoders provide the manufacturers of servomotors and other machinery with rugged, accurate and cost-efficient tools for building rotary position measurements into their products. The new kit encoders are based on POSITAL’s self-contained magnetic rotary encoders. Now however, the core components of these instruments are available as separate assemblies that can be readily integrated into other products.
The POSITAL kit encoder components offer a number of advantages over the rotation measuring devices that have traditionally been used with servomotors and rotating equipment. Compared to resolvers, they are more accurate and offer multi-turn measurement capabilities. They also provide digital outputs instead of the analog signals produced by resolvers. While POSITAL’s magnetic encoder technology provides slightly less precision than the best optical disk encoders, it is less costly, less vulnerable to contamination from oil or dust and more resistant to shock and vibration. POSITAL encoders also provide an all-electronic multi-turn absolute position measuring capability that evaluates the full absolute angular position, including the total number of shaft rotations. The rotation counter is powered by the company’s well-proven Wiegand-effect energy harvesting technology so that rotation counts are always accurate, even if the rotations occur when external power is unavailable. This system eliminates the need for backup batteries or for the geared optical disks used in some products.
POSITAL magnetic kit encoders are easy to incorporate into normal manufacturing processes since they don’t require extra-precision, near-cleanroom assembly conditions. A built-in self-calibration capability can compensate for small sensor-to-shaft alignment errors. The electronic components, including Hall-effect sensors, a 32-bit microprocessor and the Wiegand-wire energy harvesting system, are packaged in a convenient 36 mm diameter, 24.2mm deep unit. For servomotors with magnetic brakes, a special magnetic shield has been developed to isolate the magnetic pickups of the measurement system from the external magnetic fields.
The resolution of the new POSITAL kit encoders is 17 bit, with an accuracy of better than + 0.1°. The operating temperature range is -40 to +105 °C. These devices are available with a variety of non-proprietary communications protocols, including BISS, SSI and RS485-based protocols.
POSITAL is a supplier of advanced industrial position sensors used in a wide variety of motion control and safety systems. The company is also an innovator in product design and manufacturing processes and a pioneer of Industry 4.0 (Industrial Internet of Things/IIoT), offering customers the benefits of built-to-order products combined with the price advantages of mass-production. POSITAL is a member of the international FRABA group, whose history dates back to 1918, when its predecessor, Franz Baumgartner elektrische Apparate GmbH, was established in Cologne, Germany to manufacture relays. Since then, the company has played a trendsetting role in the development of rotary encoders, inclinometers and other sensor products. POSITAL has a global reach with subsidiaries in Europe, North America and Asia – and sales and distribution partners around the world.
by Gary Mintchell | Aug 17, 2016 | Automation, Technology
The most exciting thing happening now with industrial robots is the new intimacy of human and machine–collaborative robots.
Since I had other plans and could not attend the Rockwell Automation track at the EHS Conference coming up in Pittsburgh, Rockwell brought a piece of the safety symposium to me. George Schuster, a member of the global safety team at Rockwell and a robotics safety expert, discussed the current state of the art with me.
Schuster told me that Rockwell Automation is working with Fanuc Robots to change the way people and machinery interact.
There is much interest in the work in the user community to create manufacturing processes that leverage the strengths of machines (stability, reliability, strength) and the intelligence and adaptability of humans.
“In the past we engineered to keep them separate or at least arbitrate the shared space. Now we’ve found good benefits to engineer ways for people and machines to work together,” said Schuster.
Three things are enabling this approach. First, there are the standards. ISO 10218 and ANSI/RIA 15.06-2012 give guidance for designers. They also make it clear that thorough risk assessments must be carried out when designing these processes. Next, Rockwell is blending its safety technology with robotics. Then design approaches are looking holistically at what is possible with human and machine working together. Together, this is actually more of an application space rather than just technology.
Increasingly working on removing barriers between robotics and controllers, technology includes connectivity and safety–EtherNet/IP Safe; GuardLogix system; Add-on profiles in software-pre-engineered common data structure; part of the Connected Enterprise, includes connection of devices plus communication to upper levels to collect and analyze information–all working together.
There are four key current applications: ability to stop robot without killing power to allow operator to interact for instance load/unload, can quickly enter/leave area; hand guided operation, person can move/guide robot kind of like ergonomic load assist; speed and separation monitor, sensor system detects presence and position of personnel, modulates robot, can stop if person gets too close, coordinates robot speed and approaching person; power force limiting-this one is a little tricky, it’s hard to know where the robot will come in contact and what force is acceptable to the human, difference between soft flesh and hard place, etc.
This is all cool. It is ushering in a new era of manufacturing.