by Gary Mintchell | Sep 4, 2019 | Automation, Events, Productivity, Technology
That engineers would develop ways for humans and robots to co-exist, yes even collaborate, seemed inevitable. Why should we consign robots to cages as safety hazards when the future assuredly requires close collaboration. Therefore the burgeoning area of collaborative robotics or cobots.
I’m thinking not just about industrial applications. Robots surely will assist an aging population cope with everyday tasks in our (near) future of fewer people to populate those jobs.
Several of the “old guard” robotics companies have developed “co-bots” but I’ve watched the development of Universal Robots for some time. The company sponsored this blog for a while a few years ago. Here I’ve picked up on a couple of items. The UR marketing team was a bit surprised to discover that I have more than a passing interest in packaging. As a matter of fact, I noticed packaging as a likely growth area for automation about 18 years ago, and that feeling has been borne out.
One story concerns a packaging demonstration with a socially worthwhile goal mixed in. The other reports on a recent market study by ABI Research.
Universal Robots Solves Random Picking Challenge, Providing Food for At-Risk Youth
The challenge: Pick six differently sized food items randomly oriented on a moving conveyor and place each of these items into the same pouch. Then do this again 1,199 more times, ensuring each pouch has the same six items. This is the challenge Universal Robots and Allied Technology will address, quickly identifying and picking items – ranging widely from packs of Craisins to cans of beef ravioli – in Pack Expo’s Robotics Zone during the three-day show.
“Random picking is quickly becoming one of the most sought-after automation tasks from industries such as e-commerce, fulfillment centers and warehousing,” says Regional Sales Director of Universal Robots’ Americas division, Stuart Shepherd. “At Pack Expo, Universal Robots and Allied Technology will demonstrate how UR cobots can be quickly deployed in a compact, modular system, handling the entire process from box erecting, to vision-guided conveyor tracking, part picking, tote assembly, pouch filling and sealing, kitting and palletizing,” he says, adding how the packaging line is also a testament to the capabilities of Universal Robots’ growing number of Certified System Integrators (CSIs). “Allied Technology was able to quickly create this fully-automated solution. We are delighted to see our cobots competently integrated in so many new packaging applications now.”
Allied Technology and Universal Robots’ packaging line features four UR cobots equipped with products from the UR+ platform that certifies grippers, vision cameras, software, and other peripherals to work seamlessly with UR’s collaborative robot arms. The latest flexible grasping technology will be showcased by a UR5e with Piab’s new Kenos® KCS vacuum gripper guided by a vision camera from UR+ partner Cognex.
Once completed, the 1,200 bags of food will be delivered to “Blessings in a Backpack” a leader in the movement to end childhood hunger, ensuring that children receiving free or subsidized school lunches during the week do not go hungry over the weekends. “We look forward to showcasing this demo that is meaningful in so many ways,” says Shepherd. “We are excited to partner with Blessings in a Backpack while also addressing the needs of the packaging industry with solutions that will simplify and fast-track cobot deployment on their lines.”
Unlike traditional robots caged away from show attendees, visitors to the UR booth are able to walk right up to the UR cobots and interact with them. The booth “playpen area” will feature several cobot arms including a U53e with Robotiq’s new UR+ certified E-Pick Vacuum Gripper, allowing attendees to explore on-the-spot programming. The gripper is one of the recent additions in a rapidly expanding UR+ product portfolio that now includes no less than 195 UR+ certified products with 400+ companies participating in the UR+ developer program.
Market Leadership
Meanwhile, Universal Robots maintains top spot in ABI Research’s Ranking of Cobot Companies in Industrial Applications; Doosan, Techman Robot, and Precise Automation are closing in.
This news originates with ABI Research. There are well over 50 manufacturers of collaborative robots (cobots) worldwide, but only a handful of these companies have so far deployed cobots on any meaningful level of scale. Tens of thousands of cobots have been sold as of 2019 and earned US$500 million in annual revenue for world markets. In its new Industrial Collaborative Robots Competitive Assessment, global tech market advisory firm, ABI Research finds Universal Robots (UR) to be the clear forerunner, particularly in implementation.
The Industrial Collaborative Robots Competitive Assessment analyzed and ranked 12 collaborative robot vendors in the industry – ABB, Aubo Robotics, Automata, Doosan Robotics, FANUC, Franka Emika, Kuka AG, Precise Automation, Productive Robotics, Techman Robot, Universal Robots, and Yaskawa Motoman – using ABI Research’s proven, unbiased innovation/implementation criteria framework. For this competitive assessment, innovation criteria included payload, software, Ergonomics and human-machine interaction, experimentation and safety; implementation criteria focused on units and revenue, cost and ROI, partnerships, value-added services, and the number of employees.
“Market leaders in cobots generally have well-developed cobot rosters, in many cases backed up by an ecosystem platform that integrates applications, accessories, and end-of-arm-tooling (EOAT) solutions in with the base hardware,” said Rian Whitton, Senior Analyst at ABI Research. With 37,000 cobots sold so far, UR leads, followed by Taiwanese provider Techman with 10,000, and Korea-based Doosan with over 2,000. Precise Automation, which uses an advanced direct drive solution to develop faster collaborative robots, was cited as the most innovative of the 12 providers, just edging out Universal Robots, who claimed the overall top spot due to their significant lead in implementation.
There are several companies that are too young to be challenging the dominant parties in the cobot market but are developing new and disruptive technologies that will allow them rise to prominence in the years to come. Productive Robotics is a case-in-point. The California-based developer has an arm with inbuilt vision, 7 axes for superior flexibility, long reach, and a very affordable price point, but has yet to deploy at scale. Automata, a British company that develops a ‘desk-top’ cobot costing less than US$7,000, is significantly lowering the barriers to entry for smaller actors and is championing the use of open-source middleware like ROS to program cobots for industrial use-cases. Germany-based Franka Emika and Chinese-American provider Aubo Robotics also represent relatively new entrants to the market who are building on the success of Universal Robots and are beginning to compete with them.
Perhaps surprisingly, while the major industrial robotics providers have developed cobot lines, they have generally been less successful in marketing them or gaining market traction relative to the pure-cobot developers. In part, this is down to focus. While collaborative robots are valuable, they generally suit deployments and use-cases with smaller shipments and a wider variety of small and large end-users. For industrial players like ABB, FANUC, KUKA AG and Yaskawa Motoman, their client-base tends to be large industrial players who buy fixed automation solution through bulk orders. Aside from this, all four of these companies are competing extensively for greater shipment figures in China, where the cobot oppurtunity relative to the market for traditional industrial systems is much less apparent than in Europe or North America.
“Though many of the cobots deployed by these companies are impressive, and they have a lot of software services, the high-cost and lack of easy use among their systems largely defeat the current value proposition of cobots, making them the laggards in this competitive assessment.” says Whitton.
Looking forward, the larger industrial players are likely to improve their relative position, as future growth in cobots rests on scaling up and large deployments. “Universal Robots, though likely to remain the market leader for the foreseeable future, will be increasingly competing on an even footing with near-peer cobot developers, who are already developing second-generation cobots with significant hardware improvements. Meanwhile, some more innovative companies will be able to accelerate adoption through price decreases, improved flexibility, and common platforms to retrofit collaborative capability on industrial robots,” Whitton concluded.
These findings are from ABI Research’s Industrial Collaborative Robots Competitive Assessment report. This report is part of the company’s Industrial Solution, which includes research, data, and analyst insights. Competitive Assessment reports offer comprehensive analysis of implementation strategies and innovation, coupled with market share analysis, to offer unparalleled insight into a company’s performance and standing in comparison to its competitors.
by Gary Mintchell | Oct 17, 2018 | Automation
Beckhoff Automation had a sizable booth at Pack Expo this week. Much to my surprise, when I asked about whether there was something new (I don’t expect new product introductions in automation at Pack Expo) the answer was yes. Well, I had a glimpse at Hannover in April.
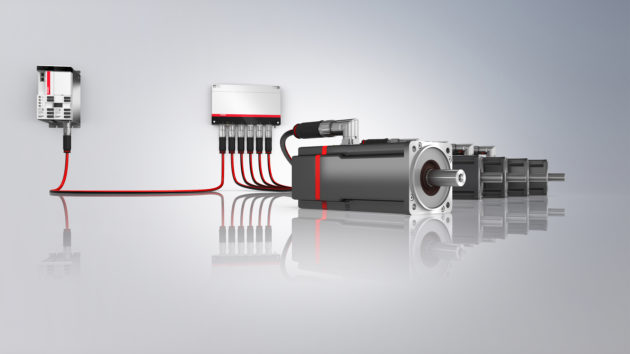
The AMP8000 servo system has an innovative design where the integrated drive is placed on the end of the servo motor rather than the usual side. This design allows for maximum heat dissipation from the motor. They were able to package the drive and motor that only added 75 mm to the length of the motor.
By combining a servo drive and servomotor into one device, the AMP8000 system reduces overall packaging machine footprint and space requirements inside control cabinets and enclosures. A single coupling module can operate up to five drives using the EtherCAT P One Cable Automation solution that supplies industrial-grade power and EtherCAT industrial Ethernet communication.
Requiring Requiring no alterations to the existing machines, the AMP8000 boasts power ratings from 0.61 to 1.23 kW and standstill torque ratings from 2.00 to 4.8 Nm at an F4 flange size or power ratings from 1.02 to 1.78 kW and standstill torque ratings from 4.10 to 9.7 Nm with an F5 flange. The servo drive system also represents the Beckhoff commitment to promoting safety technology in all areas via integrated STO and SS1 safety functions.
TwinCAT software updates have added a number of important tools for packaging machine builders and end users, including expanded data processing through TwinCAT Analytics and HTML5-enabled TwinCAT HMI for industrial displays and mobile devices. In addition, TwinCAT Motion Designer supplies additional tools to commission entire motor, drive and mechanical systems in software, whether integrated into the TwinCAT 3 platform or used as a stand-alone motion system engineering tool.
by Gary Mintchell | Oct 16, 2018 | Automation, Process Control, Technology
This week is another week on the road—five out of the last six—and now I’m in Chicago at Pack Expo. Much like IMTS, Pack Expo fills three halls of McCormick Place with machines. And machine components such as controls, drives, software, instrumentation, and the like.
Two weeks ago was Emerson Global Users Exchange. I wandered into the Emerson Automation Solutions booth not expecting much that was new. OK, got that one wrong.
If you want an indicator that Emerson has seriously expanded beyond oil & gas, keep on reading. It is now a serious player in this space, as well.
I once was an executive with a company that designed and built automated assembly machines. One interesting niche we had was an expert in helium mass spectrometry leak testing. I can give the sales pitch on the value of in-line, 100% testing of products.
Well, not as good as when Emerson explained its new food and beverage leak detection system.
Emerson’s RosemountTM CT4215 uses laser technology to detect leaks, reject defective packages with no production slowdown.
The Rosemount CT4215 is the first quantum cascade laser/tunable diode laser (QCL/TDL) continuous, inline detection system designed to help assure quality and safety, maximize production volume and decrease product waste for food and beverage products. The Rosemount CT4215 tests the seal and integrity of every bottle or package on a production line, detecting leaks at a sensitivity as low as 0.3 mm and automatically rejecting any defective bottle or package without slowing down production. This is in contrast to the traditional practice of testing occasional grab samples, which can leave a manufacturer vulnerable to low quality, unsafe food or beverages, reduced profitability and damaged reputation.
“In an industry being driven by an increasing consumer awareness of freshness and safety, manufacturers need solutions that allow them to assure these qualities while maintaining, or even increasing, efficiency,” said Peter Watmough, global leak detection product manager, Emerson Automation Solutions. “The Rosemount CT4215 provides packagers with an easy-to-install, easy-to-use assurance of freshness and safety. For the first time, food and beverage packagers can measure every package and bottle for leaks without having to compromise their production speed.”
Emerson further unveiled a new line of transmitters designed specifically for hygienic applications in the food and beverage industry with a compact form factor that will enable manufacturers to minimize downtime and lower production costs.
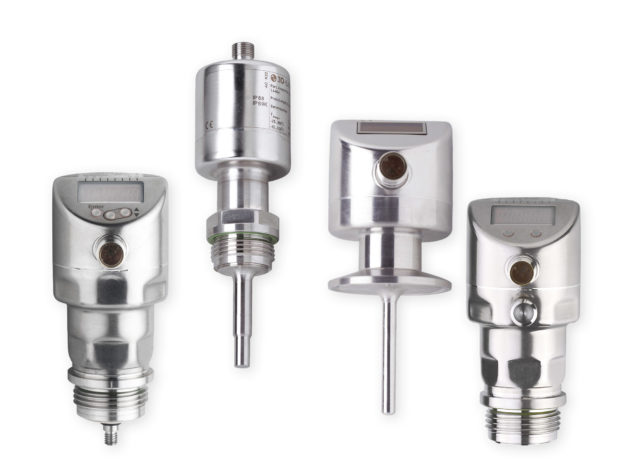
The new line of transmitters—Rosemount 326P Pressure, Rosemount 326T Temperature, Rosemount 327T Temperature and Rosemount 326L Level instruments—are designed to operate in the hygienic environments required by food and beverage manufacturers:
All comply with 3-A and FDA specifications, and are available with nine common industry process connections to ensure the right fit for new tanks and pipe fittings, as well as capability to be retrofitted on legacy systems. The new, small transmitters also can be mounted in tighter locations common on packaging machinery. Conventional 4-20 mA outputs and IO-Link connectivity make the transmitters easy to integrate with automation systems.
To give a sense of the breadth of Emerson Automation Solutions commitment to the space, following are some summaries of products.
Emerson’s ASCO G3 Fieldbus Electronics completely modular system plugs together via mechanical clips that allow easy assembly and field changes without dismantling the entire manifold, and its modules can be used in centralized or distributed applications.
One particular demonstration that will feature G3 Fieldbus Electronics is Emerson’s ASCO Bread Packing Machine. This state-of-the-art system provides full pneumatic automation control to ensure high-speed, repeatable packaging of food products. Its G3 Fieldbus integrates pneumatic control and provides real-time diagnostic data via an integrated webserver. It demonstrates flexible and energy-efficient design through proper sizing of pneumatic systems to fit any food packaging operation.
Emerson’s SolaHD Power Quality solutions remove limitations in the power architecture, allowing machine designers and operators to safely put power where they need it. These power supplies can be mounted directly on a machine, freeing packaging lines from design constraints; eliminating the complexity and cost of unnecessary enclosures and excess wiring; and providing the power for current and future automation capabilities.
Emerson’s Branson Ultrasonic Automated Cutting System provides precise food portioning with an almost frictionless cutting surface resulting in cleaner cuts, faster processing, minimal waste, longer blade life, higher productivity for greater throughput, and reduced downtime for cleaning.
Emerson helps packaging operations reduce process variation and decrease costly losses through technologies that deliver real-time insight into machine and process performance. With the accurate, relevant data in hand, packaging operations can achieve better reliability, reduce losses and contamination as well as ensure long-term performance.
With Emerson’s Micro Motion Filling Mass Transmitter (FMT), high-value packaging lines can accurately fill a wide range of container sizes and products with a single meter, eliminating the cumulative error associated with multiple-device measurement solutions. The Micro Motion FMT reliably measures fluids with entrained solids or gases or with changing viscosities, making it ideal for high-speed filling and dosing applications. Its Coriolis mass-based measurement is immune to variations in process fluid, temperature or pressure, and Automatic Overshoot Compensation (AOC) ensures repeatable fills even under valve performance changes. In addition, the Micro Motion FMT enables operators to track quality control and filling valve-performance data in real time to reduce filler maintenance and cost.
In addition, Emerson’s Micro Motion Multiphase Flow Meter technology can help complex process operations reliably log Gas Void Fraction and liquid density and concentration measurements. Utilizing Micro Motion Advanced Phase Measurement software, these meters also tolerate “real life” conditions of foaming, end-of-batch cavitation or slug flows to enable consistent measurements in challenging multiphase conditions. In addition, Smart Meter Verification delivers detection of coating or fouling within the meter for added clean-in-place efficiency and insight.
An interactive display illustrating pneumatics and IIoT features Emerson’s AVENTICS Smart Pneumatics Monitor, an IIoT hub allowing local data collection and analysis independent of the controller. The pick-and-place display illustrates “predictive maintenance” by showing the health and performance of valves, cylinders and shocks, which can minimize the risk of unplanned machine downtime to increase ROI.
To demonstrate how operators can protect personnel and reduce risk without impacting productivity. the Emerson booth will feature the Emerson ASCO 503 Series Zoned Safety Manifold (with G3 fieldbus electronics). It simplifies the design of a redundant pneumatic safety circuit with a manifold system that can be configured to shut down air and power only to the group of valves that controls the machine’s motion in the operator’s vicinity while the rest of the machine remains in operation. Multiple independent safety circuits can easily and cost-effectively be designed into a single pneumatic valve manifold, reducing the number of safety system components by up to 35 percent, requiring less plumbing, and shrinking the size of a safety system so that valuable real estate within the machine and manifold can be used for other purposes while still providing enhanced operator safety.
by Gary Mintchell | Jun 6, 2018 | Asset Performance Management, Data Management, Internet of Things
Have you been wondering about GE Digital and such products as Predix Asset Performance Management since the announcements of the new GE CEO reducing the group and throwing it into turmoil?
Well, just when I realized I had not heard anything for a while, this press release appeared. I don’t usually write about the announcements that come daily about sales “wins” or about success stories. But I felt this was significant in that it was news that GE Digital is still out there and that here is a user that is not a GE company. Also it reflects a trend of collaboration among companies. Plus another trend—one of the original hopes for the Industrial Internet of Things, that is, adding ability for OEMs to monitor their equipment at the customer’s site and provide service and support.
Here, GE Digital and SIG, a leading provider of packaging systems and solutions for the food and beverage industry, announced a strategic partnership to power digital innovation in food and beverage packaging.
SIG will deploy GE Digital’s PredixAsset Performance Management (APM) and Predix ServiceMax industrial applications across more than 400 customer factories worldwide to drive new levels of efficiency, create intelligent solutions and enable new possibilities for its customers.
The food and beverage industry is ripe for digital transformation, with consumers increasingly seeking innovative, convenient products that are not only safe and sustainable but also affordable and differentiated. At the same time, producers are facing competitive pressures, supply chain complexities and ever-shorter production cycles – creating an increased need for technologies that can enable producers to quickly identify, predict and act on changing consumer and market demands.
The unique combination of GE Digital’s APM and ServiceMax applications will enable SIG to build an end-to-end digital platform that will bring a new level of insight and data-driven intelligence to its customers worldwide – helping them and SIG transform how they predict, manage and service the entire lifecycle of SIG filling lines. By automatically collecting and analyzing asset data – tapping into billions of data points across its operations globally in real time – SIG and their customers can move beyond traditional asset monitoring and predictive service models to reimagine their supply chain, enhance quality control technologies and evolve their portfolio mix.
“Our ability to harness data is central to delivering on our promise of opening up new opportunities for our customers,” said Rolf Stangl, SIG, CEO. “By tapping into information in new and innovative ways, we will be able to deliver an unmatched level of performance, security, transparency and creativity across the entire food and beverage supply chain – through to the end consumer.”
SIG’s customers fill more than 10,000 unique products into SIG packaging across 65 countries worldwide. In 2017 alone, SIG produced 33.6 billion carton packs for its customers. Through this large-scale partnership, SIG and GE Digital will co-innovate packaging solutions and technologies to address the industry’s two biggest needs today: improving asset performance and optimizing service delivery.
The new digital service model will also enable SIG to deliver new solutions and business models based on advanced performance metrics, including as-a-service delivery, performance-based and subscription solutions.
The initial deployment is expected to go live in July 2018 with the global rollout anticipated to begin in January 2019.
by Gary Mintchell | Dec 4, 2014 | Automation, Motion Control
Technosoft,
based in Neuchâtel, Switzerland, has released the first member of its iMOT line of motors with integrated motion controller and drive — the iMOT172S XM-CAN intelligent stepless motor.
The product is based on a cost-effective hybrid step motor on which the motion control specialists at Technosoft have integrated a magnetic encoder, together with a member of their powerful iPOS motion controllers, into a very compact package (42 x 42 x 70 mm).
The design is made, for high reliability, with only one PCB incorporating the encoder and the iPOS controller that utilizes the Technosoft MotionChip technology and provides 7 I/Os. The configuration, tuning and local programming of the iPOS drive can easily be done using Technosoft’s powerful graphical platform, EasyMotion Studio. The position sensor is absolute single-turn, providing 4096 counts per revolution for accurate speed and position control, down to 5 arc minutes.
While an EtherCAT version is under preparation, the current release covers two CAN versions: the standard CANopen, in accordance to the CiA 301, 305 and 402 profiles, and the TMLCAN protocol. TML (Technosoft Motion Language) opens the possibility to use the powerful motion controller, allowing it to operate as an independent intelligent device. As an example, any homing routine can be customized to match the application needs. Standalone single- or multi-axis applications with communication between drives without the need of a CAN master are possible, while various types of CAN masters are as well supported through an extended set of Technosoft Motion Control Libraries.
This intelligent stepless motor reaches a peak torque of 500 mNm at 1000 rpm without a gearbox, achieved from a motor with a square flange of 42 mm. The maximum length of the integrated unit is a mere 70 mm. The high efficiency of the solution is obtained due to Technosoft’s implementation of current and torque vector regulation under a field oriented control method (FOC) that practically transforms the motor into a stepless servo motor, dramatically reducing the current consumption and heat dissipation typical to hybrid steppers.
The standard NEMA17 flange ensures multiple sources of gearheads that are available for fitting to the motor, depending on the requirements of the application.
An intelligent motor can be used in many applications, but it has been developed for medical analysis and dosing machines, pick and place and welding robots, instrumentation and optical equipment, unmanned military vehicles, packaging, bottling and labeling machines.
Intelligent Motion Control Drive
It has also rele
ased the iPOS3604 HX-CAN—a closed frame intelligent drive offering a very compact solution for sinusoidal or trapezoidal position, speed and torque control of rotary or linear DC Brushless and open-loop or closed-loop control of 2-phase and 3-phase step motors requiring power up to 144 watts. The supply voltage range is 12 to 36 VDC with a continuous current of 4 A, (10 A peak) and a PWM frequency of 20 KHz.
This high performance servo drive offers high level single or multiple-axis control functions such as master, slave or standalone operations in a small package of only 80 x 55 x 16 mm. Although extremely compact, iPOS3604 HX embeds motion controller, drive and PLC functionality in one unit.
iPOS3604 HX can operate as a CiA402 CANopen drive, or can be programmed to execute complex motion programs directly at drive level, using their built-in motion controller and the high level Technosoft motion language (TML).Thanks to the TML instruction set, the iPOS3604 HX is an intelligent drive, programmable at user’s level and offering position and speed profiles, PVT & PT interpolated, electronic gearing and cam, external reference: analogue or sent via a communication bus.
The configuration, tuning and programming of the iPOS3604 HX-CAN drive is easy with Technosoft’s powerful graphical platform, EasyMotion Studio. System configuration and parameterization are performed by selecting and testing the system structure, motor and sensor types and control mode.
Flexibility and easy implementation make the iPOS3604 BX-CAN drives an ideal solution to fulfilling today’s motion axis control needs, using modern distributed intelligence architecture.