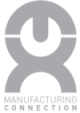
Oil and Gas Interoperability Pilot
I started another Website called Physical Asset Lifecycle last year to discuss interoperability.
Two things happened. The reason to have a separate Website evaporated into the vacuum of failed business ideas. I also ran out of time to maintain yet another Website.
So, I will be reposting the work I did there and then building upon that work as an Interoperability Series.
There are key technologies and thinking when it comes to interoperability. The foundation is that we want to break silos of people and technologies so that applications can interoperate and make life easier for operations, maintenance and engineering. This will also improve the efficiency and effectiveness of operations. Much of the work so far is led by MIMOSA.
Interoperability demo
Two years ago, the foundation came together in a pilot demo at the ISA Automation Week conference of 2012. Here is the report from then.
After years of preparatory work, the OpenO&M Initiative participants organized a demonstration pilot project of information interoperability run like a real project building a debutanizer. It demonstrated the full lifecycle of the plant including all the facets of plant from design through construction to operations and management. The demonstration was held two days at the ISA Automation Week Sept. 25-26, 2012 in Orlando.
A panel of some of the people who worked on this project presented their work and showed live demonstrations.
One of the most important advances in the project was that now the three major design software suppliers–Aveva, Bentley, and Intergraph were all involved with enabling export of design data to a standard interface.
EPC for the project was Worley Parsons. Cormac Ryan, manager, Engineering Data Management, Americas, explained the development of the P&IDs using Intergraph’s Smart Plant P&ID generator. It produced a traditional P&ID. Not only a diagram, it is a database-driven tool containing lots of reports and data. The data was published in ISO 15926 format and made available to the rest of the team.
Jim Klein, Industry Solutions Consultant from Aveva, used a schema similar to the Intergraph one. It acted as a second EPC duplicating the data with the object-based database behind the drawing. It can store and link to an engineering database that contains much more data. For example, clicking on a pump diagram can show specifications and other important design information. This data was published out to instantiate the object in a maintenance management system or to create new data as it gets revised during the engineering process. Information can communicate to a “MIMOSA cloud” server.
George Grossmann, Ph.D., Research Fellow, Advanced Computing Research Centre, the University of South Australia, explained a transform engine using Bentley Open Plant received in 2 formats–owl and ecxml. These data go to iniSA 15926 transform engine. This engine takes input from all three suppliers, exports in ISO 15926 then to MIMOSA standard exports in CCOM XML.
Next up Ken Bever, with Assetricity and also CTO of MIMOSA discussed the transform from CCOM XML to the Assetricity iomog register, assuring that information was mapped to the asset and then sent to IBM’s IIC application in a standardized way. The information was then sent to OSIsoft PI historian. From PI, data is then accessible to maintenance management and operations management applications. All data references back to the ISO 15926 ontology.
Bruce Hyre, from IBM, explained how the IIC application is a standards-based platform that federates data and provides analytics. It takes CCOM, feeds it into a model server, which then provisions tags in OSI PI server. His demonstration showed the actual live P&ID from the EPC. He added, “But our focus is on the data supporting that P&ID–the tag list/model tree. You can subscribe to a tag, see information from the upstream systems.” Therefore the demonstration showed that data have gone end-to-end from design to the PI server to provision the tags with the live data from the design. 1092 tags were provisioned in this demonstration.
A video of the presentation can be found on the MIMOSA Website.
Program manager is Alan Johnston. Contact him for more information or to lend your expertise to the effort.