by Gary Mintchell | Oct 16, 2018 | Automation, Process Control, Technology
This week is another week on the road—five out of the last six—and now I’m in Chicago at Pack Expo. Much like IMTS, Pack Expo fills three halls of McCormick Place with machines. And machine components such as controls, drives, software, instrumentation, and the like.
Two weeks ago was Emerson Global Users Exchange. I wandered into the Emerson Automation Solutions booth not expecting much that was new. OK, got that one wrong.
If you want an indicator that Emerson has seriously expanded beyond oil & gas, keep on reading. It is now a serious player in this space, as well.
I once was an executive with a company that designed and built automated assembly machines. One interesting niche we had was an expert in helium mass spectrometry leak testing. I can give the sales pitch on the value of in-line, 100% testing of products.
Well, not as good as when Emerson explained its new food and beverage leak detection system.
Emerson’s RosemountTM CT4215 uses laser technology to detect leaks, reject defective packages with no production slowdown.
The Rosemount CT4215 is the first quantum cascade laser/tunable diode laser (QCL/TDL) continuous, inline detection system designed to help assure quality and safety, maximize production volume and decrease product waste for food and beverage products. The Rosemount CT4215 tests the seal and integrity of every bottle or package on a production line, detecting leaks at a sensitivity as low as 0.3 mm and automatically rejecting any defective bottle or package without slowing down production. This is in contrast to the traditional practice of testing occasional grab samples, which can leave a manufacturer vulnerable to low quality, unsafe food or beverages, reduced profitability and damaged reputation.
“In an industry being driven by an increasing consumer awareness of freshness and safety, manufacturers need solutions that allow them to assure these qualities while maintaining, or even increasing, efficiency,” said Peter Watmough, global leak detection product manager, Emerson Automation Solutions. “The Rosemount CT4215 provides packagers with an easy-to-install, easy-to-use assurance of freshness and safety. For the first time, food and beverage packagers can measure every package and bottle for leaks without having to compromise their production speed.”
Emerson further unveiled a new line of transmitters designed specifically for hygienic applications in the food and beverage industry with a compact form factor that will enable manufacturers to minimize downtime and lower production costs.
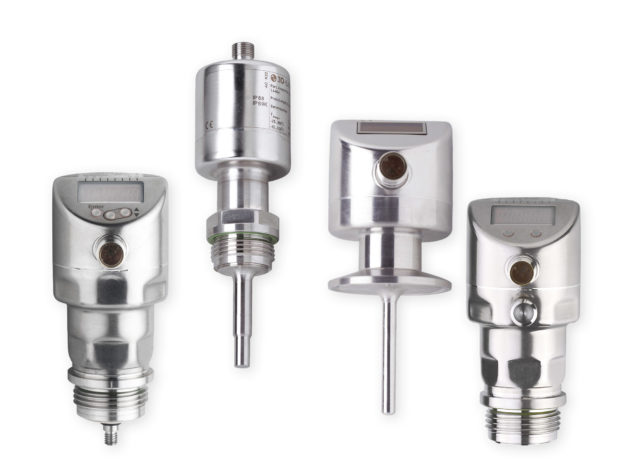
The new line of transmitters—Rosemount 326P Pressure, Rosemount 326T Temperature, Rosemount 327T Temperature and Rosemount 326L Level instruments—are designed to operate in the hygienic environments required by food and beverage manufacturers:
All comply with 3-A and FDA specifications, and are available with nine common industry process connections to ensure the right fit for new tanks and pipe fittings, as well as capability to be retrofitted on legacy systems. The new, small transmitters also can be mounted in tighter locations common on packaging machinery. Conventional 4-20 mA outputs and IO-Link connectivity make the transmitters easy to integrate with automation systems.
To give a sense of the breadth of Emerson Automation Solutions commitment to the space, following are some summaries of products.
Emerson’s ASCO G3 Fieldbus Electronics completely modular system plugs together via mechanical clips that allow easy assembly and field changes without dismantling the entire manifold, and its modules can be used in centralized or distributed applications.
One particular demonstration that will feature G3 Fieldbus Electronics is Emerson’s ASCO Bread Packing Machine. This state-of-the-art system provides full pneumatic automation control to ensure high-speed, repeatable packaging of food products. Its G3 Fieldbus integrates pneumatic control and provides real-time diagnostic data via an integrated webserver. It demonstrates flexible and energy-efficient design through proper sizing of pneumatic systems to fit any food packaging operation.
Emerson’s SolaHD Power Quality solutions remove limitations in the power architecture, allowing machine designers and operators to safely put power where they need it. These power supplies can be mounted directly on a machine, freeing packaging lines from design constraints; eliminating the complexity and cost of unnecessary enclosures and excess wiring; and providing the power for current and future automation capabilities.
Emerson’s Branson Ultrasonic Automated Cutting System provides precise food portioning with an almost frictionless cutting surface resulting in cleaner cuts, faster processing, minimal waste, longer blade life, higher productivity for greater throughput, and reduced downtime for cleaning.
Emerson helps packaging operations reduce process variation and decrease costly losses through technologies that deliver real-time insight into machine and process performance. With the accurate, relevant data in hand, packaging operations can achieve better reliability, reduce losses and contamination as well as ensure long-term performance.
With Emerson’s Micro Motion Filling Mass Transmitter (FMT), high-value packaging lines can accurately fill a wide range of container sizes and products with a single meter, eliminating the cumulative error associated with multiple-device measurement solutions. The Micro Motion FMT reliably measures fluids with entrained solids or gases or with changing viscosities, making it ideal for high-speed filling and dosing applications. Its Coriolis mass-based measurement is immune to variations in process fluid, temperature or pressure, and Automatic Overshoot Compensation (AOC) ensures repeatable fills even under valve performance changes. In addition, the Micro Motion FMT enables operators to track quality control and filling valve-performance data in real time to reduce filler maintenance and cost.
In addition, Emerson’s Micro Motion Multiphase Flow Meter technology can help complex process operations reliably log Gas Void Fraction and liquid density and concentration measurements. Utilizing Micro Motion Advanced Phase Measurement software, these meters also tolerate “real life” conditions of foaming, end-of-batch cavitation or slug flows to enable consistent measurements in challenging multiphase conditions. In addition, Smart Meter Verification delivers detection of coating or fouling within the meter for added clean-in-place efficiency and insight.
An interactive display illustrating pneumatics and IIoT features Emerson’s AVENTICS Smart Pneumatics Monitor, an IIoT hub allowing local data collection and analysis independent of the controller. The pick-and-place display illustrates “predictive maintenance” by showing the health and performance of valves, cylinders and shocks, which can minimize the risk of unplanned machine downtime to increase ROI.
To demonstrate how operators can protect personnel and reduce risk without impacting productivity. the Emerson booth will feature the Emerson ASCO 503 Series Zoned Safety Manifold (with G3 fieldbus electronics). It simplifies the design of a redundant pneumatic safety circuit with a manifold system that can be configured to shut down air and power only to the group of valves that controls the machine’s motion in the operator’s vicinity while the rest of the machine remains in operation. Multiple independent safety circuits can easily and cost-effectively be designed into a single pneumatic valve manifold, reducing the number of safety system components by up to 35 percent, requiring less plumbing, and shrinking the size of a safety system so that valuable real estate within the machine and manifold can be used for other purposes while still providing enhanced operator safety.
by Gary Mintchell | Jul 12, 2018 | Automation, News, Technology
There are electric motors and then there are electric motors. On my recent trip about an hour south to the Siemens electric motor manufacturing plant in Norwood, OH (a suburb of Cincinnati) I was often thinking about the line from Crocodile Dundee when the main character pulled out that child of a sword and Bowie knife and said, “Knife? That ain’t no knife. This is a knife.” When we start talking Medium Voltage motors at greater than 10,000 HP, that’s a motor.
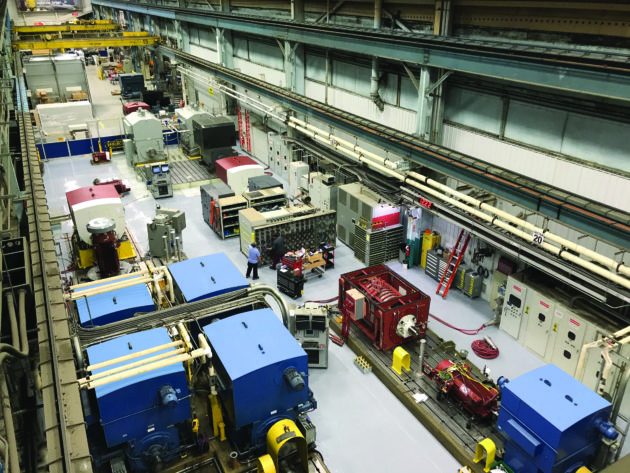
Note: the one in red is a motor under test. Note the size versus the size of the person.
I’ve visited the plant a time or two before but wrote the news for magazines. Only a mention on my blog. When I was there in 2012, they talked about the transformation of the plant from a traditional old-school heavy manufacturing plant to a modern, lean, clean place to work putting out quality products.
The occasion for this visit was to view results of some significant investments by Siemens in maintaining Norwood as a state-of-the-art motor manufacturing plant. There are several new machines for precision machining of large parts. The pièce de résistance however was a new test bed and “Test Center Observatory” where customers can witness the testing of their motors in comfort with a dedicated Ethernet connection so that they can continue working during downtimes in the test process. A complete test regimen can last for several hours or even longer. Some customers come from other countries. Speaking as someone with experience traveling to witness tests on my products for certification, I’d have really appreciated this facility back in the day.
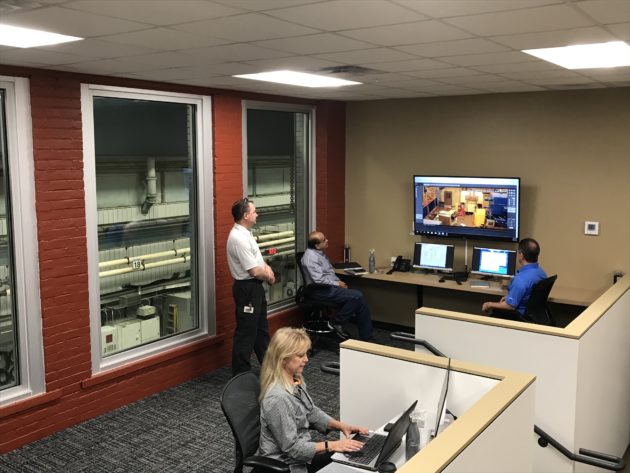
Before I get to the test bed, a brief discussion of digitalization and vibration.
Siemens has developed a digitalization methodology for motors called Drive Train Analytics. They are sensoring more and more in order to monitor and analyze a more complete virtual picture of the motor. Not surprisingly, they use Siemens Mindsphere sending data to the cloud using a variety of analysis tools. Customers have access to these tools in the observatory. Actually, customers could receive a complete virtual runoff of their motor back home. But engineers being engineers, they love to see the hardware in person. So they get both.
Aside from heat, the main killer of motors is vibration. Siemens has taken steps both to reduce vibration in the motor and to reduce ambient vibrations in the test process so that more accurate readings of the motor itself.
Working with customers who provide feedback from their use cases, Siemens developed a new shaft requiring new machining techniques. Some of the advantages of the new shaft include:
- Eliminates variation due to fabrication and spider bar tolerances
- Reduces required balance weight applied during rotor balance
- Removes heat-treatment process
- Improves rotor thermal stability
- More predictable rotor lateral stiffness
- Reduces stress concentration of weldment
The News-Test Observatory
With its celebration of more than 120 years of innovation, market and product leadership, technology and quality, Siemens’ Norwood Motor Manufacturing plant recently opened a new Test Observatory.
Opened in 1898, the Norwood facility has undergone a century of change, as the process to manufacture motors and the technology behind them has improved. Norwood has stood the test of time through three industrial revolutions and is one of the longest continuously operating Siemens’ plants globally. With Industry 4.0 upon us, the mechanical motor of old is now a connected device, a valuable plant floor asset capable of providing vast amounts of data with preventative and predictive analytics to ensure more productivity, efficiency and uptime.
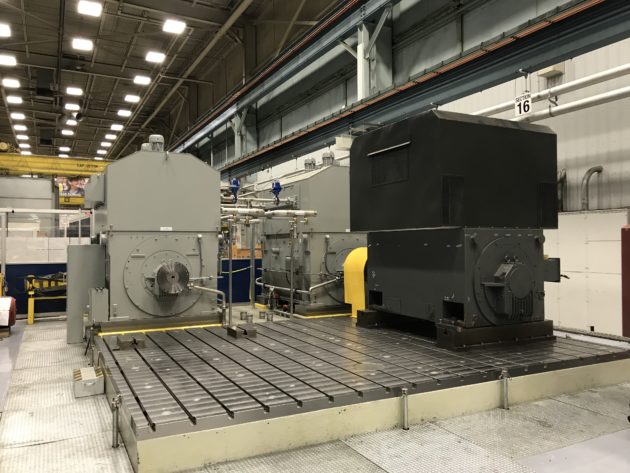
With the largest motor test base in North America, Siemens can combine its century of industry leadership in motor manufacturing with an enhanced customer experience. The new equipment extends Norwood’s testing range from 10,000 horsepower (HP) to 20,000 HP at frequencies from 10 Hz to 300 Hz, thus addressing the market’s increased use of variable frequency drives. The new test observatory, akin to an executive suite, allows customers to participate by observing testing through bay windows, direct cameras and mirroring computers, which display real time critical data being gathered by sensors attached to their motor.
The project, which began in 2016, required the removal of 550 tons of soil and concrete from the site, excavating a 13-foot deep hole, driving 114 pilings for stability and building a huge concrete vault to securely support a fully loaded test stand. The test stand weighs 360 tons and rests on a self-leveling air spring system designed to support 500 tons when loaded with motors and drives.
The testing equipment includes two Sinamics Perfect Harmony GH180 drives and two dynamometers. Generating power to test a 20,000 HP motor requires significant amounts of electricity, and by recycling power to the grid, the new equipment reduces power loss by 90 percent.
“At Norwood, we test every motor that we produce or repair – some 30 to 50 tests per week – and these new facilities give us the ability to conduct as many as five motor tests at a time.” said Tim Bleidorn, Manager, Manufacturing Excellence. “We expect the customer witness tests to average two to three per week and as many as 120 per year.”
In addition to the new test base and observatory, the multi-million dollar investment in Norwood also includes WFL high-precision shaft making equipment and a high-speed balancer, key for two-pole applications at higher speeds and the ability to balance a rotor at up to 12,000 rpm.
“It’s exciting and I’m proud that Siemens is investing in the North American market. We have the No. 1 market share in AboveNEMA motors right now and these new capabilities send a strong signal to our customers and competitors that we intend to maintain that position,” says Ryan Maynus, AboveNEMA Product Manager.
With more than 100 patents, the 350,000 square-foot facility is a cornerstone to Siemens AboveNEMA motors. The ISO-9001 certified plant has produced more than 150,000 high voltage motors since 1898. The Norwood plant produces horizontal AC induction motors up to 20,000 horsepower and voltage ranges from 460 to 13,200 volts. The plant also manufactures a complete line of large AC vertical motors up to 8,000 horsepower.
by Gary Mintchell | Mar 21, 2017 | Operations Management, Software
Software solution underlies project to improve Overall Equipment Effectiveness (OEE) in a BorgWarner plant. Lean practitioners once hated automation and software. Over the years, though, appropriate use of these technologies actually improves Lean performance. Here is a case study.
The cloud-based lean manufacturing solution provider Leading2Lean was part of a Total Productive Maintenance (TPM) solution that helped auto powertrain maker BorgWarner increase Overall Equipment Effectiveness of an operating area by 10 percent in six months when coupled with its TPM implementation, at its Seneca, SC plant.
Soon after implementing Leading2Lean, the plant began to resolve inefficiencies and frustrations with a system that allowed them to better identify production weaknesses. The plant handled an increase in product demand while still improving First Pass Yield ratios, reducing scrap, maintaining high production levels, better utilizing labor resources, and improving overall communication with management and employees.
The team maintained high levels of operational availability—some areas as high as 90 percent. Area employees drive this process optimization—scheduling, planning and monitoring performance of machines on their lines—all through the Leading2Lean product.
“It’s as easy to use as Facebook or Google,” said Will Venet, TPM Implementation Leader at BorgWarner. Experienced managers also find the system intuitive. “What a reliability engineer took decades of experience to learn can be learned in an afternoon,” Venet said.
Plant Maintenance Engineer Rodney Osborne said the crew used to use “gut checks” to guess which machine needed maintenance or how much money they spent on spare parts for a machine. “But now with Leading2Lean we do a simple report and it tells us—there’s no ambiguity,” Osborne says. “It takes the gut check out of it. It’s real data, and it’s without question a much better way of doing business for us.”
Initially, some employees thought bringing in the Leading2Lean system was an oversight effort, like “Big Brother,” but results soon changed their minds. Today, there is a far more collaborative relationship between Production and Maintenance, and team members at all levels feel more engaged because they are empowered to identify and produce solutions for continuous improvement.
Downtime reductions were driven largely by the engagement of operators. This was because they had easy access to the data and the manipulation of that data to drive improvements in preventative maintenance. What used to take four or five days to analyze through laborious data mining can now be done in 20 minutes.
“The collaborative efforts the team is making for continuous improvement are influenced by having a tool that is universally appreciated,” Venet said. “I’ve come to appreciate that what Leading2Lean is really doing is helping us to be a better manufacturer all around.”
by Gary Mintchell | Mar 3, 2017 | Automation, Technology
Despite the bad press that robots receive these days, I still have a soft spot in my heart for the technology. I first learned to program one in 1985. I’ve seen how robots remove humans from unsafe working conditions and improve product quality.
I have also liked what I’ve seen from Rethink Robotics. However, the press release I recently received was so filled with superlatives, that I was beginning to wonder if there was substance behind the hype. I’m betting there is. (And I removed most of the superlatives so that it reads better. Maybe I’ll see them at Automate and get a deeper dive.)
Rethink Robotics has announced Intera 5, a first-of-its-kind software platform that connects everything from a single robot controller, extending the smart, flexible power of Rethink Robotics’ Sawyer to the entire work cell and simplifying automation with ease of deployment.
Intera 5 fundamentally changes the need for integration, making it substantially easier and more affordable, allowing manufacturers to deploy full work cell automation in a matter of hours, not weeks, according to the press release.
Intera 5 is much more than the latest version of Rethink Robotics’ software; it’s a new way to approach automation that allows manufacturers to control the robots, orchestrate the work cell and collect data.
“With the introduction of Intera 5, we’ve created the world’s first smart robot that can orchestrate the entire work cell, removing areas of friction and opening up new and affordable automation possibilities for manufacturers around the world,” said Scott Eckert, president and CEO, Rethink Robotics. “Intera 5 is driving immediate value while helping customers work toward a smart factory, and providing a gateway to successful Industrial Internet of Things (IIoT) for the first time.”
Rethink Robotics’ Intera 5 modernizes the traditional work cell by improving coordination, increasing flexibility and drastically reducing deployment times. Run through the robot’s controller, manufacturers can orchestrate conveyors, equipment and other machines from a central Intera 5-powered robot.
Tuthill Plastics Group, a full-service custom injection molding company, is using a Sawyer robot with Intera 5 to power improved product quality and more efficient production. Operating 24 hours a day, five days a week, Sawyer with Intera 5 is picking parts from a conveyor belt and communicating with a computer numeric control (CNC) machine to precisely place the part into the machine by using Intera 5’s unique force-sensing capabilities. By applying a precise level of force while placing the part, the Tuthill team has been able to improve part quality and consistency, reducing a length defect on the part by 98 percent since implementing Sawyer.
“Sawyer with Intera 5 is a major step forward in manufacturing automation,” said Richard Curtain, president, Tuthill Plastics Group. “Part placement is extremely critical to our machining process. Sawyer is able to effectively ensure product quality and consistency, handle the variability of the production line, and automatically re-register to the environment in the event that any parts move.”
German magnet manufacturer, MS Schramberg, is also leveraging Sawyer with Intera 5 and has substantially improved deployment time. With six robots operating on three machines, MS Schramberg has one robot selecting parts from a series of patterns and loading the part into the machine, while a second robot removes the part from the machine and loads the part into a tray.
With less than a day of training, an MS Schramberg engineer is able to deploy and train the robots in just more than an hour. The robots now run 24 hours per day, six days per week, and can easily configure complex logic tasks, minimizing the need for human interaction and freeing up employees for more complex tasks.
“We’ve cut our deployment times by hundreds of hours with Intera 5, and are able to easily deploy our Sawyer robots on an extremely complex task in just over an hour,” said Norman Wittke, general manager, MS Schramberg. “The ease and speed of deployment is extremely valuable for our company, and is helping make our manufacturing processes more efficient, while improving our ROI.”
With Intera 5, manufacturers will reap the benefits of:
- Industry-leading embedded vision, which will allow the robot to perform tasks just as humans do, reducing the need for expensive part presentation fixturing and additional integration costs.
- Adaptive force-sensing, allowing users to precisely set the amount of force required, or enable the robot to feel and respond to a specific force, so the robot can make adaptive decisions while performing a task.
- Intera Studio, an intuitive and powerful new tool to simply and effectively deploy automation like never before, providing a gateway to the factory of the future.
“Intera 5 is equipping industry leaders like Tuthill Plastics and MS Schramberg to achieve immediate bottom-line improvements in productivity, quality and efficiency on the factory floor,” said Eckert. “By implementing our robots equipped with Intera 5, manufacturers will have unprecedented work cell coordination, greatly reducing the need for complex, time-consuming and outdated automation options.”
Beginning in March, Intera 5 will be available for download on all existing Sawyer robots, and will come standard on all new robots.
by Gary Mintchell | Nov 16, 2016 | Automation, Safety
This is another of a series of posts from the Rockwell Automation show Automation Fair last week. This stop on the tour concerned Safe Machines. The safety team has been active for many years now developing new products and initiatives. Not everything they do is expressly pointed at selling a product. Often they are out in public teaching safe machine practices, risk assessment, and safe machine design.
They showed a BevCorp machine that had been designed with the latest safety advances in mind. The idea involved removing incentives to defeating safeties. One feature is an ultra-wide door that allows access to more of the machine.
The safety system has a “request to enter” function. This is a high inertia filler machine. Activating the function begins with guiding the machine to a slow stop at a repeatable location. Therefore the controls always know status without requiring a reboot. Of course, there is a safe reduced speed mode to allow maintenance without a shutdown.
Integral with the Connected Enterprise philosophy of Rockwell Automation, the HMI and software collects data on who/what stopped the machine, which safety devices were triggered, and the like. From this data, employee behavior can be ascertained.
This leads to the real value of Connected Enterprise–production, engineering and EH&S can come together to evaluate the entire system from all points of view. The goal is to maintain productivity through use of a safe machine.
I’ve followed Rockwell Automation safety for years. In fact, I can remember classes in the 90s before becoming an editor on risk assessment and the launch of safety products. There have been two popular podcast interviews at Automation Minutes one on Safety Automation Builder and the other on the Safety Maturity Index.
This is the last stand where I had a deep dive. Following will be a review of partners who also exhibited at the Fair. Then it will be on to the next conference–which I couldn’t visit in person, but I have some interviews.