by Gary Mintchell | Jun 23, 2020 | Events, News, Process Control, Workforce
One conference I’m attending from the comfort of my office this week is Honeywell Virtual Technology Experience. Thanks to the pandemic, no Honeywell User Group (HUG) this year.
This remote conference technology constantly improves. This is my fourth of the season. Technical glitches have been rare. Speakers overall have ranged from good to outstanding. Jason Urso, Honeywell Process Solutions Chief Technology Officer gave his usual great technology roundup even dialing in demos from Australia.
Interesting that I used the word remote, because that is the word of the year. Any of us who can work from home are. That includes process control where many engineers can work from home and avoid getting sick.
Urso pointed to disruptions in the economy including disturbances to supply chains, postponed maintenance checks, and restricted travel combining to increase operational risks for critical manufacturers. Simultaneously, demand for key products like toilet paper for hygiene, filter paper for purification products, and packaging materials for shipping is peaking, making reliable, high-quality production even more important.
“Living in this new reality, manufacturers are faced with having to find new ways of operating, balancing the need to keep critical processes and plants running while ensuring the safety of their employees,” noted Urso. ”Here are three critical steps manufacturers can take to navigate this unprecedented situation:
- Focus on essential work onsite to minimize the potential exposure of workers
- Adopt proven and secure remote solutions for operations
- Receive aid remotely through collaboration with on-call experts”
The bulk of the keynote reviewed three remote solutions Honeywell Process has developed for situations just like this.
Remote Project Engineering
Honeywell is continuing project operations by using software and digital twin technology. Project engineers from around the world continue working on Honeywell projects from home or in locations where offices are still operating with social distancing.
“We do so by utilizing digital twin technology that makes a digital replica of the customer’s equipment and processes which allows our project engineers to work on the ‘digital copy’ of the project versus on the actual equipment itself,” says Urso. “Critical infrastructure projects in oil and gas, pharmaceuticals, and power can proceed without interruption.”
Remote Operations
Customers increasingly have fewer individuals working onsite to follow stay-at-home orders. In some cases, quarantines of key individuals are also affecting the availability of skilled resources at the site. In response, Honeywell has issued new software that enables process operations to be monitored or even executed from remote locations outside of the facility. Remote support staff in other facilities or at home can be utilized as if they are working directly at the process location.
Case study
We recently deployed remote operations solutions to one of our own specialty additives plants in Orange, Texas, that produces polyethylenes, allowing us to operate and ensure business continuity even with reduced onsite staffing. A virtual remote-control workstation duplicates the operator’s distributed control system stations in the main control room and can fully take over in case of further restrictions or illness. Our engineers can now support operations and execute essential tasks from remote locations, maintaining social distancing while keeping the same number of eyes on the plant.
According to Urso, “software was up and running in less than two hours and is protected by the highest levels of cybersecurity protocols and best practices.”
Remote Services and Support
Our customers are also looking for Honeywell to provide remote support in light of restrictions on personnel traveling and entering a site. Honeywell has deployed multiple remote service options to continue providing expert support via remote connectivity to our equipment. These remote options also use the power of Honeywell Forge offerings to proactively detect issues and bring them to the attention of both the customer and Honeywell experts.
Because our remote offerings help our customers in essential industries maintain critical activities in a safe manner during this crisis, Honeywell Process Solutions has trained all service technicians to build awareness of this capability and collaborate with our customers through this challenging time.
by Gary Mintchell | Oct 23, 2019 | Automation, Commentary, Process Control, Security
I’ve followed Foxboro and Triconex for many years now in my coverage of the process automation business. A great company that, not unlike too many others, suffered now and again with very poor management. The company has now settled in nicely at its home in Schneider Electric and appears to be healthy here.
Much credit must go to Gary Freburger. He provided a steadying hand as the leader before and through the transition, as well as guiding the integration into the new home. He is retiring at the end of the year. I’ve met a number of great leaders and a few stinkers in my 20 years at this side of the business. Gary’s one of the great ones. And his chosen successor (see more below) seems more than up for the task of building on his successes.
Marcotte Succeeds Freburger as Process Automation President
This week’s major announcement revealed that Nathalie Marcotte has been selected to succeed Freburger as president of its Process Automation business, effective Jan. 1, 2020.
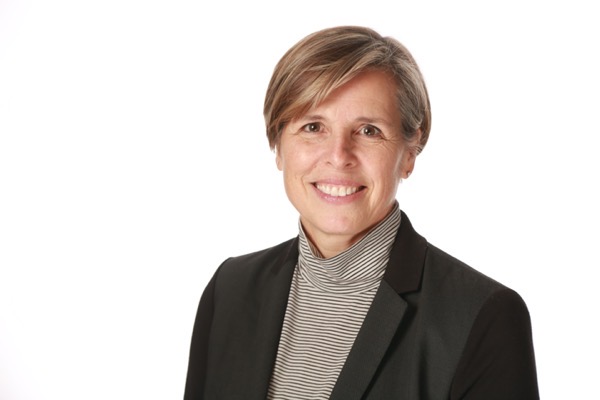
“After a long, successful industry career, including more than 15 years serving Invensys and Schneider Electric in various senior leadership roles, Gary has decided to retire,” said Peter Herweck, executive vice president, Industrial Automation business, Schneider Electric. “We thank him for his many contributions and his strong legacy of success. We wish him well, and I congratulate Nathalie on her appointment. She brings more than 30 years of industry knowledge, expertise and experience, as well as a long record of success. I look forward to working with her as we build on the success Gary has delivered.”
Since joining the Schneider organization in 1996, Marcotte has held several positions of increasing responsibility, including vice president of Global Performance and Consulting Services; vice president, North America marketing; general manager for the Canadian business; and, prior to her current position, vice president, marketing, Global Systems business. As the company’s current senior vice president, Industrial Automation Services, she is responsible for Schneider Electric’s Services business and offer development, ranging from product support to advanced operations and digital services. She is also responsible for the company’s Global Cybersecurity Services & Solutions business, including the Product Security Office.
“As we move through this transition, it will be business as usual for Schneider Electric and our Process Automation customers,” Marcotte said. “Gary and I are working very closely together to ensure there will be no disruptions to our day-to-day operations. This ensures our customers have the same access to the exceptional people, products and technology they have come to trust and rely on to improve the real-time safety, reliability, efficiency and profitability of their operations.”
“I thank Gary for his many contributions to Schneider Electric and to our industry in general. Under his leadership, our customers, partners and employees have never been better situated to succeed, today and tomorrow,” Marcotte said. “This transition will have no impact on our technology strategy and portfolio roadmap. We remain committed to our continuously-current philosophy, which means never leaving our customers behind. Now, by leveraging the strength of the full Schneider Electric offer, we can take the next step toward enabling an easier, less costly digital transformation for our customers, while keeping them on the path to a safer, more secure and profitable future.”
Following the opening keynotes, I had the opportunity to chat privately with Freburger and Marcotte. Following summarizes a few key takeaways.
Digitalization and Digital Transformation.
These topics were prominently displayed in the ballroom before the keynotes. In fact the welcome and opening presentation were given by Mike Martinez, Director of Digital Transformation Consulting. These are common themes in the industry—in fact, not only process automation, but also at the IT conferences I cover. Each company has its own unique take on the terms, but it still boils down to data, data integrity, databases, and data security. All of which were discussed.
Key Points From the Presidents.
Integration across Schneider Electric. One priority has been working with other business units (and their technologies) across the Schneider Electric portfolio. This could be PLCs and drives, but power is a huge emphasis. Schneider Electric management wants very much for its process automation acquisition to integrate well with its historic electric power business. This is seen as a strategic opportunity. One thought-provoking observation—is the process engineer/electrical engineer divide as serious as the IT/OT divide? No direct answer. But these domains have historically had little to no collaboration. One to watch.
Close working relationship with AVEVA. If you recall, Schneider Electric bundled its various software acquisitions including the ones from Invensys (Wonderware, Avantis) and used them to buy into AVEVA—the engineering software company. Bringing automation and software together was a constant source of pain for Invensys. Schneider Electric dealt with it through a separate company. Along the way, cooperation seems to be better than ever. Marcotte explained to me that Foxboro combines its domain expertise with the more broadly general software platforms to achieve customer values. See for example my previous post on Plant Performance Advisors Suite.
Cybersecurity. Marcotte has been leading Schneider’s cybersecurity efforts. These are seen as a key part of Schneider Electric’s offer. See especially the establishment of the ISA Global Cybersecurity Alliance. They don’t talk as much about Internet of Things as at other conferences, when I probed more deeply about IT, cybersecurity was again brought up as the key IT/OT collaboration driver.
It’s been a struggle, but the Schneider Electric process automation business (Foxboro and Triconex) seems as strong as ever. And the people here—both internal and customers—are optimistic and energetic. That’s good to see.
by Gary Mintchell | Oct 11, 2018 | Automation, Networking
The ODVA held its Industry Conference and 19th Annual meeting this week in Atlanta. Perhaps more than the Common Industrial Protocol (CIP), the topic of conversation was Michael—the hurricane. We started getting rain from its outer bands in the late afternoon Wednesday. By the time I awoke at 5:30 am to get ready to catch my flight out, it was all over. Not so fortunate were the millions directly impacted. My prayers go out to them.
I have missed the last two or three of these. It was good to get an update. There was no announcement while I was there, but there were some people from Honeywell Process Solutions present who talked about using EtherNet/IP for process automation applications. These switching industry alignments are fascinating to watch. Foundation Fieldbus seems to have lost momentum recently. Will EtherNet/IP, the CIP network, absorb some of the market share?
A well organized series of speakers started Wednesday morning tech sessions with a quick update from all of the SIGs. There are many volunteers putting out an incredible amount of hours developing and updating the various specifications. I can‘t report on them all here—it would be too deep into the weeds anyway. But let‘s just say that ODVA is alive and well.
As even casual readers here know, I am a fan of Time Sensitive Networking (TSN). Yes, I know that it‘s not ready for prime time, yet. Products are beginning to appear in the market, and interest is building across the industry.
I sat in two sessions focused on TSN and CIP. There is technical work going on. The sessions and ensuing questions laid bare the engineering challenges involved in developing CIP over TSN. It‘s non-trivial, but doable. Some may still question TSN, but I‘m even more bullish.
On another front, work has begun on updating the ODVA product data sheet specifications. This work will eventually provide for more and better information to users.
by Gary Mintchell | Aug 8, 2018 | Automation, Process Control, Technology
Foxboro and Triconex looks to be on the path to health under Schneider Electric. Its annual user conference is this week in San Antonio. I‘d love to be there, but personally more important is “grandparent duty” that I’m on this week. So, I had the opportunity to talk with Gary Freburger, leader of the group, and Peter Martin, VP of marketing, to get an update and view of what I’ll be missing.
Gary Freburger began with the market rebounding due to current oil pricing. Business is starting to get strong. IA product line has done well and the process business also did well going up 6% in the first half of the year. He’s expecting majority of growth over the next two years. Schneider Electric is still investing around EcoStruxure system. Foxboro is continuing on the path they discussed with us at the last user conference—how to get more value from control systems going from “necessary evil” to value add in the eyes of customer executives. The strategy is to turn data and connectivity into a business driver. The goal is enabling better decisions and improving profitability.
Freburger discussed cooperating with OPAF for a comprehensive strategy. Then he dropped in an interesting tidbit—cooperation with AVEVA. I’ve wondered about how AVEVA with the inclusion of previous Schneider Electric software would work with the Foxboro side of things. He told me they now have and end-to-end relationship to improve time to market. He noted as oil prices dropped customers thought “what can I afford to do?” Now, all have reset expectations. As oil prices rebound, they have not changed expectations. Some interesting applications and strategies include AVEVA auto populate control system, digital twin of facility, operations feedback our systems to AVEVA’s, then customer asset management upgrade works easier.
Martin discussed how Schneider is trying to change the question—from how to do control to how do we help customers solve problems that impact business? He pointed out that they’ve been doing digitization for years. What’s new is how to drive this new approach. 40 years ago controls was a solution-driven business; then with digitization the industry went from solutions to technology-driven. The times now require a need to flip flop. Solutions oriented but with today’s portfolios taking it to a much higher level. The speed of industrial business has increased—what was stable, e.g. cost of electricity—is stable no longer. The speed means IT world can’t keep up. Built-in real-time accounting control helps plants go beyond control to profitability. Foxboro is still dedicated to taking the use of technology to the next level.
During the conference (while I am writing from the forests in southern Ohio while the grandkids are in bed), Schneider Electric announced the release of EcoStruxure Foxboro DCS Control Software 7.1.With expanded capabilities and an enhanced HMI, the updated software simplifies engineering and enhances the user experience, while expanding the ability of EcoStruxure Foxboro DCS to drive measurable operational profitability improvements, safely.
The EcoStruxure Foxboro DCS is an open, interoperable and future-proof process automation system that provides highly accurate and effective control over a manufacturing plant’s operational profitability. It is the only process control system that provides measurable operational profitability improvements and a future-proof architecture, enabling a measurable 100 percent ROI in less than one year.
EcoStruxure is Schneider Electric’s open, interoperable, IoT-enabled system architecture and platform. This includes Connected Products, Edge Control, and Apps, Analytics and Services. EcoStruxure has been deployed in 480,000+ sites, with the support of 20,000+ system integrators and developers, connecting over 1.6 million assets under management through 40+ digital services.
EcoStruxure Foxboro DCS Control Software 7.1 runs on Windows 10 and Windows Server 2016, to provide maximum flexibility while ensuring robust cybersecurity. When planning upgrades, Schneider Electric customers can mix Windows XP, Windows 7 and Windows 10 on the same system, allowing flexibility in scheduling and timing for upgrades. Customers can upgrade individual sections of the plant in any order, at any pace, to best accommodate plant production schedules. With Microsoft support for Windows 7 due to end in 2020, transitioning to Windows 10 allows EcoStruxure Foxboro DCS customers to benefit from the strongest operating system with the most up-to-date cybersecurity features.
Among other new and updated features, the continuously current EcoStruxure Foxboro DCS Control Software 7.1 now includes:
• EcoStruxure Field Device Expert that improves efficiency, safety and profitability, while considerably reducing time for startup and restarts. It includes:
◦ Intelligent Commissioning Wizard, to reduce commissioning time up to 75 percent by automating HART device commissioning and documentation processes.
◦ Device Replacement Wizard to significantly reduce time and expertise to replace or commission HART devices, either individually or in bulk.
◦ Bundled HART DD library for increased security, faster device deployment, eradication of version mismatch and elimination of cybersecurity risks previously created by moving documents from the HART consortium web page into the system.
• New HMI Bulk Graphics Editor for increased operational efficiency and reliability by greatly reducing engineering hours and improving quality during testing. Use in major projects shows that replicating hundreds of displays with the new Bulk Graphics Editor saves months of man hours and improves quality by delivering highly predictable results. The Bulk Graphics Editor makes migrating from the classic FoxView HMI to the new Foxboro DCS Control HMI easier, requiring far fewer engineering hours, which reduces the time and cost to transition between technologies.
• Control Editors Activity Monitor for increased efficiency by improving communication, workflow and collaboration.
• Real-time asset health condition monitoring for increased reliability.
• Future-proof technology supporting the latest FTD 2.0 standard, which improves compatibility with digitized field devices from Schneider Electric and third-party vendors.
• New migration path, along with the new HMI Bulk Graphics Editor, simplifies the transition from existing FoxView HMI displays to the EcoStruxure Foxboro DCS Control Software 7.1 HMI platform for a continuously current and future-proof system. An upgrade migration path is available from previous Control Software Versions 5.x, 6.x and 7.0. After upgrading, users can tap into newer technologies that improve productivity, cybersecurity, efficiency and profitability.
by Gary Mintchell | Jul 17, 2018 | Automation, Process Control, Software
Did Honeywell Process Solutions (HPS) short-circuit the Open Process Automation work? Inquiring minds wonder. Once again, some news and analysis of a conference that I couldn’t attend—three of these the same week in June.
HPS and ExxonMobil sent this release. Subsequently, I talked with some sources at competitor companies who broached the question to me—did this news short-circuit the ExxonMobil-led effort for a new process control solution? An interesting caveat is that there is more than one group within ExxonMobil—and they don’t necessarily agree.
From the first release:
The Open Process Automation group was initiated by ExxonMobil who was trying to find a better (less expensive) upgrade path for its control systems that had fallen behind that of its competitors. The oil & gas supermajor still has in operation a significant number of older systems installed as far back as the 1980s—systems that have served the company well for more than 30 years, but as older electronic components have been replaced by more modern alternatives, spare-parts shortages and looming obsolescence put ExxonMobil and other owner operators in a difficult place.
When facing obsolescence, rip-and-replace is clearly the option of last resort—incurring high costs, protracted downtime and the loss of all the intellectual property invested in developing a system’s displays, databases, control strategies and third-party interfaces, according to David Patin, distinguished engineering associate – control systems, ExxonMobil Research & Engineering.
The company’s installed base of Honeywell TDC 3000 systems, in particular, looked to be facing a critical shortage of spare parts in the year 2025, Patin explained. “So in 2011 we met with Honeywell regarding the future of TDC 3000,” Patin began, addressing a plenary session of the Honeywell Users Group Americas 2018 conference this week in San Antonio.
Challenge issued
Unwilling to settle for rip-and-replace, “We challenged Honeywell to develop and prove a method to migrate TDC forward,” Patin said. The two companies established a joint task team to investigate the problem.
ExxonMobil’s wish list of deliverables included avoiding wholesale system replacement (especially the I/O); preserving the company’s intellectual property investment; allowing for on-process migration of system components (meaning without shutting down the process); enabling new capabilities not currently possible with TDC; and unifying TDC with Honeywell’s current state-of-the-art Experion platform.
This last item encapsulated a desire for a solution that would “be usable by a younger workforce, yet stand the test of time,” Patin said. “I picture a third-grader who’s also a future TDC engineer,” he said. “They just don’t know it yet.”
Also implicit in ExxonMobil’s requirements were continued “rock solid” reliability and security, Patin added.
Solution identified
Since the technical obstacles to bringing TDC forward hinged on hardware obsolescence, notably controller microprocessors and communications chips that would no longer be available, the team settled on an emulation approach that would effectively abstract TDC system functionality from the specifics of the older hardware.
And in February 2018, seven years after that first meeting of the minds—and two years ahead of schedule—Honeywell answered ExxonMobil’s challenge with the release of Experion LCN R501.1. The Experion LCN, or ELCN, effectively emulates the TDC system as software. “It’s 100% binary compatible and interoperable with the old system,” Patin explained. “Current TDC code runs unmodified in this virtual environment, greatly reducing the technical risks. Intellectual property such as application code, databases and displays are preserved.”
In the end, the Experion Station, Server, ACE and APP nodes can take the shape of Windows-based “physical” applications or virtual machines. Application Modules, Network Gateway and Network Interface Module functionality is redeployed on Universal Embedded Appliances or as virtual appliances. Only the Enhanced PLC Gateway cannot be readily virtualized because the emulation of serial network connectivity is not well behaved, Patin explained. “This means you can build an almost 100% virtualized or 100% physical system—or somewhere in between.”
With the new solution, LCN and UCN messages are now encapsulated in standard Internet Protocol. “All the old networks now exist as logical constructs on Fault Tolerant Ethernet,” Patin said. “We’re no longer locked into proprietary networks.”
And to address the challenge of on-process migration, Honeywell has also introduced several bridge devices that effectively facilitate the virtualization of TDC system node functionality—without the need to interrupt the process under control.
Benefits achieved
Virtualization of the TDC environment has come with some added benefits, including the ability to use Honeywell’s cloud-based Open Virtual Engineering Platform to engineer TDC solutions; lower cost, smaller footprint training simulators; peer-to-peer integration of virtualized HPM controller nodes with current-generation C300/ACE nodes; support for OneWireless (ISA 100 and WirelessHART) connectivity; and integration with ControlEdge and Unit
Operations Controllers.
“It’ll be a game-changer,” said Patin. “We don’t know all that’s possible as yet.”
Other benefits include a drastic reduction—or elimination—of spare parts, as well as reductions in cabinet space requirements. “We’ve gone from two nodes to six in a single cabinet,” Patin said. “We’ve not fully realized unification with Experion, but that process has begun.”
Overall, Patin gave high marks to the Honeywell team for its response to ExxonMobil’s needs. “The challenge was met, and expectations exceeded,” he said. “The need to replace an entire system is eliminated, future component issues are virtually eliminated (pun intended), intellectual property is preserved and on
process migration is supported.
“ELCN technology essentially resets the odometer on your TDC 3000 investment,” Patin added. “It’s the best example of Honeywell’s commitment to continuous evolution that I’ve ever seen. And if it were a final exam, I’d give Honeywell an A on this one.”
<End of release>
Safety Manager
HPS also announced Safety Manager SC, the next generation of its flagship Safety Manager platform. Its modular, scalable design enables it to function as a single platform for all enterprise safety applications, allowing customers – who are often using four or five different safety systems – to consolidate and reduce their training and engineering costs, and spare parts inventories.
Safety Manager SC incorporates a new Series C-based controller and Honeywell technologies such as LEAP, Universal Safety IO, offline simulation and Experion integration, which collectively simplify safety system engineering, development and testing.
“Our customers increasingly want integrated safety and control solutions and the simplicity of partnering with one supplier for all their needs,” said Tim LeFevre, global customer marketing manager for safety systems, HPS. “We deliver exactly that by combining unrivaled expertise in distributed control systems (DCS) and safety systems with deep integration know-how. Honeywell is one of the few vendors that can support the full safety lifecycle.”
HUG
The ability of Honeywell Connected Plant’s offerings to deliver higher levels of safety, reliability, efficiency and profitability will continue to be the primary discussion point at the 43rdHoneywell Users Group (HUG) Americas symposium. More than 1,300 delegates from across the oil and gas, chemical, pulp and paper, and metals and mining sectors are attending the event, which features numerous displays of the newest technologies along with dozens of Honeywell- and customer-led sessions and technical discussions.
Throughout the conference, Honeywell will showcase how turning data into actionable insight requires more than just upgrading technology; it requires a system for capturing, retaining and sharing knowledge that allows both the plant and its workers to perform at their best every day.
“Digital transformation has to be about more than just moving data into the cloud,” said John Rudolph, president of Honeywell Process Solutions (HPS). “It ultimately has to be about the outcomes, including driving increased productivity and savings for our customers while allowing them to increase knowledge capture, knowledge sharing and knowledge retention among their employees.”
Rudolph was named president of HPS on May 31, 2018, succeeding Vimal Kapur, who was named president and CEO of Honeywell Building Technologies. Rudolph led the Projects and Automation Solutions, and Lifecycle Solutions and Services businesses for HPS over the past six years, driving significant growth. Rudolph also has held leadership roles with TAS Energy, General Electric and Ingersoll Rand.
Here is a revealing comment from the press release about HPS’s strategy and direction—something we’ve all been wondering about. “HUG attendees will be able to see and experience the Company’s ongoing transformation into a software-industrial provider.”
Announcements in brief:
- Thermal IQ – Enables maintenance engineers and plant managers to more effectively monitor and manage their thermal process equipment, minimizing unplanned downtime and maximizing uptime.
- Uniformance Cloud Historian – This software-as-a-service cloud hosting solution for enterprise-wide data capture, visualization and analysis helps customers improve asset availability, optimize processes and increase plant uptime.
- Asset Performance Management – Integrates asset and process data for actionable insights to improve asset performance and plant profitability.
- Immersive Competency – This cloud-based simulation offering uses a combination of augmented reality (AR) and virtual reality (VR) to train plant personnel on critical industrial work activities, empowering them to directly improve plant performance, uptime, reliability and safety.
- Personal Gas Safety – This solution integrates with Honeywell’s leading plant control system to protect workers and speed emergency response in case of hazardous leaks or worker injury.
- Intelligent Wearables – This hands-free, wearable technology allows industrial workers to more safely, reliably and efficiently accomplish their tasks in the plant or the field. It uses a head-mounted visual display that responds to voice and brings live data, documents, work procedures, as well as health and safety information into view and can connect field workers with remote experts in real time.
- Experion Batch – Combines Experion distributed control, batch automation, and new visualization technology for improved efficiency, quality and throughput.
- Measurement IQ for Gas – Provides measurement under control by transforming metering operations with 24/7 real-time condition-based monitoring.