by Gary Mintchell | Nov 1, 2019 | Internet of Things, Manufacturing IT, Uncategorized
Many engineers and programmers like open source projects combined with open APIs. Some open source catches on and quietly becomes widely used. Others languish. The Linux Foundation’s Edge project, especially EdgeX Foundry, keeps quietly growing. What are the odds that this becomes a widely used Internet of Things tool?
Today’s news in brief:
- EdgeX’s fifth release offers more scalable solutions to move data from devices to cloud, enterprise and on-premises applications
- The first LF Edge project to achieve Stage 3 ratification, EdgeX hits widespread adoption and production-level maturity
- EdgeX and LF Edge onsite at IoT Solutions World Congress with demos from Dell Technologies, Home Edge, IOTech and Project EVE
EdgeX Foundry, a project under the LF Edge umbrella organization within the Linux Foundation that aims to establish an open, interoperable framework for IoT edge computing independent of connectivity protocol, hardware, operating system, applications or cloud, announced the availability of its “Fuji” release. This release offers additional security and testing features on top of the production-ready “Edinburgh” release launched this spring.
“EdgeX Foundry has experienced significant momentum in developing an open IoT platform for edge-related applications and shows no signs of slowing down,” said Arpit Joshipura, general manager, Networking, Edge and IoT, the Linux Foundation. “As the only Stage 3 project under LF Edge, EdgeX Foundry is a clear example of how open collaboration is the key to an active community dedicated to creating an interoperable open source framework across IoT, Enterprise, Cloud and Telco Edge.”
Launched in April 2017, and now part of the LF Edge umbrella, EdgeX Foundry is an open source, loosely-coupled microservices framework that provides the choice to plug and play from a growing ecosystem of available third-party offerings or to augment proprietary innovations. With a focus on the IoT Edge, EdgeX simplifies the process to design, develop and deploy solutions across industrial, enterprise, and consumer applications. As a Stage 3 project under LF Edge, EdgeX is a self-sustaining cycle of development, maintenance, and long-term support. As an example of the rapidly accelerating use of the code, EdgeX hit a milestone of 1 million platform container downloads, which almost half of these took place in the last few months.
“The 1M container download isn’t our only milestone,” said Keith Steele, EdgeX Foundry chair of the Technical Steering Committee and LF Edge Governing Board member. “The development team has expanded with more than 150 active contributors globally and the partner ecosystem of complementary products and services continues to increase. As a result, we’re seeing more end-user case studies that range from energy and utilities, building automation, industrial process control and factory automation, smart cities, retail stores and distribution and health monitoring.”
The Fuji Release
As the fifth release in the EdgeX Foundry roadmap, Fuji offers significant enhancements to the Edinburgh 1.0 release, which launched in July, including:
- New and improved security features to include PKI infrastructure for token/key generation.
- Application services that now offer full replacement capability to the older export services provided with previous EdgeX releases. These application services offer more scalable and easier to use solutions to get data from the EdgeX framework to cloud, enterprise and on-premises applications.
- Example application services are provided with this release to allow users to quickly move data from EdgeX to the Azure and AWS IoT platforms.
- A new applications function Software Development Kit (SDK) also provides the EdgeX user community with the ability to create new and customized solutions on top of EdgeX – for example, allowing EdgeX to move edge data to legacy and non-standard environments.
- Unit test coverage is considerably increased (in some services by more than 200 percent) across EdgeX core and supporting microservices.
- New device service connectors to BLE, BACNet, IP camera, OPC UA, GPS, and REST device services.
- Choices for commercially-supported EdgeX device connectors are also starting to blossom with offerings for CANopen, PROFINET, Zigbee, and EtherCat available through EdgeX community members.
Inaugural EdgeX Open
The EdgeX Foundry community recently kicked off a series of hackathons, titled the EdgeX Open. More than 70 attendees participated in the first event on October 7- 8, 2019, in Chicago. Hosted by LF Edge and the Retail Industry Leader Association (RILA), and sponsored by Canonical, Dell Technologies, Deep Vision, Intel, IOTech, IoTium and Zededa, the event featured five teams that competed in retail use case categories. More details on the event, including the winning use case from Volteo, are available in this blog post.
The next hackathon will coincide with the Geneva release, targeted for Spring 2020. It will be centered on the Manufacturing vertical and held in a location in Europe.
by Gary Mintchell | Nov 23, 2018 | Automation, Networking, Standards, Technology
I will only be at SPS for a few hours this year to check in with old friends and see some of the latest automation goodies. But I’m glad to be there at all. Thank you to Siemens who is sponsoring a press tour that includes a couple of days of intense cybersecurity briefings and workshops.
Oh, and a trip to Allianz Stadium to see the technology and a Bayern Munchen football match.
Some early SPS news:
- Avnu Alliance Demonstrates New Conformance Test Reference Tool
- OPC Foundation promises much news plus addition of Rockwell Automation
OPC Foundation
OPC Foundation has sent a couple of emails inviting us to a press briefing at SPS promising much news. I won’t be in Nuremberg on Tuesday, but I’ll catch up with Stefan and Tom for sure on Wednesday.
The mating dance has ended after a few months. Rockwell Automation has rejoined the OPC Foundation and gained a board seat. OPC Foundation has elected Juergen Weinhofer, vice president of common architecture and technology for Rockwell Automation, to its board of directors. Note that Weinhofer is also the Rockwell delegate to the ODVA board.
Weinhofer’s election to the board extends Rockwell Automation’s engagement in the technical work of the OPC Foundation and its technical advisory council.
“OPC UA has become the dominant open protocol for machine-to-software and machine-to-cloud solutions, and it is becoming critical for companies deploying a Connected Enterprise,” Weinhofer said. “I look forward to helping the OPC Foundation become a leader in machine-to-machine applications and helping OPC UA users unlock more value from their production systems.”
This quote is from the OPC news release. We should note that “Connected Enterprise” (capitalized) is the Rockwell Automation theme. I also note while parsing the comment that Rockwell is still firmly fixed in the factory floor area where Weinhofer specifically states “become a leader in machine-to-machine applications.”
“Rockwell Automation is a proven leader in industry standardization and open information technologies,” said Stefan Hoppe, president of the OPC Foundation. “I welcome not just Juergen’s business and political skills on the board but also the increased technical and commercial contribution that the wider Rockwell Automation team will also bring to the foundation.”
Avnu Alliance
Avnu Alliance, an industry consortium enabling open, standards-based deterministic networking, will exhibit at SPS IPC Drives in the University Stuttgart ISW booth. Avnu Alliance, alongside ISW and Industrial Internet Consortium (IIC), will showcase the role of conformance test plans, testbeds and test reference tools in ensuring an interoperable ecosystem of Time Sensitive Networking (TSN) devices.
“We are in cooperation with IIC, IEEE, IEC and others in creating an interoperable ecosystem through a common network foundation that stems from industry open standards and testing,” said Todd Walter, Avnu Alliance Industrial Segment Chair. “The market will continue to require multiple application layer protocols for networked industrial systems. The Avnu Alliance charter is to enable interoperability at the network layer, to ensure ‘One TSN.’ We are the organization focused on providing TSN test plans and reference test architectures to anyone in the industry that wants to test for TSN compatibility.”
As such, Avnu serves to support Fieldbus organizations by providing its TSN conformance tests and procedures to ensure those organizations’ interoperability in the wider Ethernet system.
Leveraging the industry-defined requirements for TSN network interoperability, Avnu ensures there is a universal set of test plans for conformance to guarantee interoperability at the network layer. Avnu has developed a baseline test plan in the industrial market that ensures industrial devices, whether end device, infrastructure component or silicon, conform to the relevant IEEE standards, as well as the industrial automation profile being defined by IEC/IEEE 60802 Joint Project working group.
Starting with Time Synchronization, or 802.1AS as the foundation for all TSN devices, Avnu released the first set of test plans at SPS IPC Drives in 2017. Avnu will soon publish additional conformance test plans for end devices, such as enhancements for scheduled traffic.
At SPS IPC Drives 2018, Avnu Alliance will show a new proof-of-concept (POC) Conformance Test Reference Design that offers a single, streamlined way for vendors to test TSN interoperability. The POC Conformance Test Reference Design is designed to automatically test TSN devices for compliance to 802.1AS. The demonstration features a Linux open-source test tool created by ISW in partnership with Avnu. This tool would also allow other protocol organizations to test application stacks on top of a TSN network in a streamlined way enabling one-stop certification at any test house.
by Gary Mintchell | Nov 8, 2018 | Internet of Things, Operations Management, Standards
Another group validates standards for industrial communication including FDT and OPC UA.
FDT Group, an independent, international, not-for-profit standards association supporting the evolution of FDT technology (IEC 62453), announced that its Board of Directors voted unanimously to empower the emerging FDT IIoT Server (FITS) architecture with full platform independence. This decision strengthens the FITS architecture to support the diverse array of operating systems to meet industry-driven demands.
In addition to platform independence, key features of the FITS solution include native integration of the OPC Unified Architecture (OPC UA), as well as comprehensive Control and Web Services interfaces. With built-in security protecting valuable information and operating data, the FITS platform will enable cloud, enterprise, on-premise, and a single-user desktop deployment method meeting the needs of the process, hybrid and discrete manufacturing sectors.
“The FITS platform is the ‘game changer’ the automation industry has been anticipating,” said Glenn Schulz, managing director of FDT Group. “I’d like to thank our Architecture and Specification Working Group that worked behind the scenes investigating and prototyping the platform independence feature approved by our board.”
Schulz added, “The Architecture and Specification Working Group has been directed to immediately transition FDT Server Common Components to a pure .NET Core implementation, previously built on the Microsoft .NET Framework. This transition will result in a single FDT Server environment deployable on a Microsoft-, Linux-, or macOS-based operating system, which will empower the intelligent enterprise by bridging the current installed base with next-generation solutions supporting the IIoT and I4.0 era.”
The significant decision and direction allows nearly unlimited deployment and application scenarios. For example, cloud-based FDT Servers can enjoy the performance and cost benefits of a Linux operating system. Traditional control system vendors can offer the FDT Server embedded in their hardware, and machine builders can deploy a small Linux-based FDT Server offering a comprehensive preconfigured asset management system for their skid that can be securely accessed remotely or with smart phones or browsers.
MES applications can also incorporate an FDT Server to gain secure, direct access to production data and asset health and availability metrics through OPC UA. In addition, service providers can wrap services around an FDT Server delivered in an industrial hardened Linux box. The opportunities for cost savings and value creation goes on due to the highly flexible deployment options of the FITS standard.
Because of the security, scalability and the ease of deployment of an FDT Server, the solution will simplify entry into the IIoT marketplace as the only open platform standardized integration architecture providing a single interface with cloud-to-plant floor mobile access. The decision to migrate to platform independence will delay the launch of the FITS specification by approximately six months. With the launch planned for the latter half of 2019, alongside Common Components supporting the FITS standard, automation suppliers and service providers will immediately reap the benefits of a quick development and deployment strategy. Common Components create a library of FDT routines and will simplify compliant development of FITS-based solutions such as Servers, Device Type Managers (DTMs) and APPs.
The final standard will be delivered as three documents: the FDT 2.5 specification, which builds on FDT 2.1 to include HTML5 and JavaScript graphical user interface features; the FITS Web Services Technical Specification, which describes the Web Services interfaces and requirements for an FDT Server; and the OPC UA Annex detailing the OPC UA Server mapping for an FDT Server.
by Gary Mintchell | Nov 5, 2018 | Internet of Things, Manufacturing IT, Standards
OPC UA and TSN (Time Sensitive Network). A marriage I was beginning to think was never going to happen. I wrote a preliminary white paper following Hannover Messe 2017. Yes, more than a year ago. (Check it out by clicking the small ad on the sidebar.) This thing has been like a ball in a Rugby match—kicked, going different directions, downed and picked up. People wanting to move before thinking. Getting caught up in legal issues and “politics.” Postponed press conferences.
And, now…”The OPC Foundation launches an initiative to further enable OPC UA adoption throughout industrial automation by extending standardization and harmonization activities for OPC UA including TSN-enabled Ethernet networks.”
The goal of this initiative is to deliver an open, cohesive approach to implement OPC UA including TSN and associated application profiles. This will advance the OPC Foundation providing vendor independent end-to-end interoperability into field level devices for all relevant industry automation use-cases. The OPC Foundation vision of becoming the worldwide industrial interoperability standard is advanced by integrating field devices and the shop floor.
A new set of working groups will identify, manage and standardize the OPC UA relevant topics focused on industrial automation including,
• harmonization and standardization of application profiles e.g. IO, motion control, safety, system redundancy
• standardization of OPC UA information models for field level devices in offline e.g. device description and online e.g. diagnostics
• mapping of OPC UA application profiles related to real-time operations on ethernet networks including TSN
• definition of certification procedures
The working groups will closely align with the TSN Profile for Industrial Automation (TSN-IA-Profile) which will be standardized by the IEC/IEEE 60802 standardization group. This will help ensure that a single, converged TSN network approach is maintained so that OPC UA can share one common multi-vendor TSN network infrastructure together with other applications.
This initiative integrates well with existing joint working groups engaged in ongoing companion specification e.g. description of machines.
Stefan Hoppe, President of the OPC Foundation said “The benefit of membership in the OPC Foundation allows companies to actively engage and influence the direction of the OPC Foundation and includes early access to the specifications and technology. This initiative will grow OPC UA into new markets and I highly encourage all OPC Foundation members to contact the OPC Foundation to participate”.
Thomas Burke, Strategic Marketing Officer of the OPC Foundation, “We are very excited about the initiative to extend OPC UA including TSN down to the field level, and the number of companies that want to actively participate in this initiative bringing the technology into real world products. This set of working groups will pave the way for the broadest, easiest, and fastest market adoption of OPC UA over TSN.”
The OPC Foundation develops and maintains OPC UA as an open and secure communication platform comprised of an information model framework, communication models and underlying protocol bindings. As such, the OPC Foundation works non-exclusively with other organizations on various OPC UA related topics but continues to operate as a platform, technology, use case, and vendor agnostic standardization body.
by Gary Mintchell | Oct 31, 2018 | News, Organizations
Tom Burke stepped down as President and Executive Director of the OPC Foundation after 23 years of leadership. He will remain on the Board of Directors continuing his global evangelization for the standard.
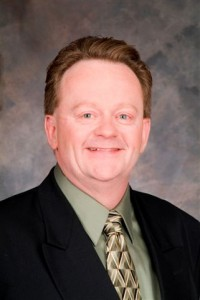
Stefan Hoppe, currently a vice president of the organization, becomes the new President and Executive Director. This follows on the recent news that the Board created a new Chair position and elected Veronika Schmid-Lutz of SAP to that position.
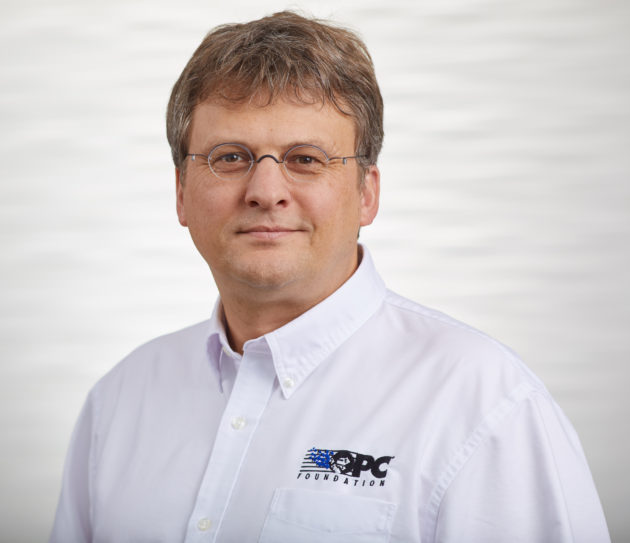
Hoppe is a familiar face in the community through his work as VP of Marketing for the past four years.
He joined BECKHOFF in 1995 where he developed OPC classic server and in 2006 the first OPC UA server integrated into an embedded controller. In 2008 he initiated and chaired the PLCopen OPC UA Companion working group. In 2010 Mr. Hoppe was elected President of OPC Foundation Europe. Since 2014, he is Vice President of the OPC Foundation and member of the OPC Board.
Hoppe said “It is truly an honor to be entrusted with the responsibility and exciting opportunity to lead this incredible global organization towards its full potential. While the OPC Foundation roots come from industrial automation and will always be grounded there, I believe it is our duty to greatly widen our horizons in multiple directions – inside industrial automation but also into other new markets.“
On the future adoption of the OPC technology Mr. Hoppe continued, “the value of the open, secure, vendor independent data interoperability the OPC UA standard introduces is universal and is as important to IoT applications across all markets as Ethernet was to connect computers and is to the Internet. My mission is to position and grow the OPC Foundation to work on this scale.”
Elaborating on his decision to change roles, Burke said, “After an amazing 23 years, I have decided it is time to turn over the reins of the day-to-day operations as the President and Executive Director of the OPC Foundation to the next generation. I believe Stefan Hoppe is the right person for this job as he has clearly demonstrated his commitment and strong leadership on many occasions. I look forward to him advancing the OPC Foundation and its OPC UA technology.”
Hoppe concluded “On behalf of the OPC Foundation I sincerely thank Thomas Burke for the vision, leadership, and tireless evangelism he provided all these years. It was great to work with Thomas Burke for the last 8 years and I appreciate his decision to continue his worldwide OPC UA evangelization and contribution of his deep valued insights and strategic advice.”
I am not surprised by the changes. I’ve worked closely with Tom for many years. I’ve also known Stefan since his days at Beckhoff Automation. His presentations for OPC UA have increasingly become less German-centric remaining a powerful statement of the value of standards for the successful implementation of Industry 4.0 and Digital Transformation.
I view this transition as a classic move from the entrepreneur to management. In the end it will be a positive step for the organization. I wish them all well.