by Gary Mintchell | Nov 12, 2018 | Manufacturing IT, Software
Wondering what Rockwell Automation is going to net out of its $1B investment in PTC that also netted John Genovesi a major promotion within the company? I have been. And here is the first release.
The companies have launched FactoryTalk InnovationSuite, powered by PTC, a software suite that enables companies to “optimize their industrial operations and enhance productivity by providing decision makers with improved data and insights.” The new suite delivers visibility of operations and systems status from one source of information inside the organization. The collaborative offering is the first to integrate technologies from both companies following the strategic partnership announcement in June.
FactoryTalk InnovationSuite, powered by PTC, improves connectivity to operational technology (OT) devices on the plant floor, natively supporting the rapid, scalable, and secure connection of the most commonly used industrial equipment. Combined with data from information technology (IT) applications and systems, decision makers can now gain a complete digital representation of their industrial equipment, lines, and facilities from anywhere in the enterprise.
“Our offering is unique in its ability to improve how companies capitalize on the IIoT by combining expertise from industry, technology, and plant-floor professionals,” said John Genovesi, incoming senior vice president, Enterprise Accounts & Software, Rockwell Automation. “Now we’re bringing innovative solutions from PTC together with leading analytics and Manufacturing Operations Management (MOM) from Rockwell Automation for a differentiated industry solution.”
“We’re moving the needle on how leading-edge technology is applied in industrial environments,” said Catherine Kniker, Head of Strategic Alliances, PTC. “Manufacturers have seen digital technology rapidly change, but their execution continues to follow practices established for the legacy business. This bundled offering will help organizations accelerate time to value and reinvent how they compete by breaking down barriers across their operations through a comprehensive approach to operational intelligence.”
Included in this collaborative offering are the FactoryTalk Analytics and MOM platforms, as well as PTC’s ThingWorx Industrial IoT Platform, which includes industrial connectivity from Kepware, and the Vuforia augmented reality solution.
Key features of applications within the new collaborative offering include:
Intuitive, user-friendly interfaces that give users a view of the operations by combining data from multiple IT and OT sources and tailored to their role. An operations manager, for instance, can view overall performance of a facility, or multiple facilities, before researching the performance of specific equipment or factors impacting OEE.
Automated advanced analytics of IT and OT sources transform massive amounts of raw data into actionable or proactive information to improve performance and reduce the impact of downtime. Leveraging powerful artificial intelligence (AI) technology to simplify complex analytical processes, users can now proactively respond to issues ahead of any critical failures.
Augmented reality (AR) delivers more efficient and effective ways of looking at digital information within the physical world. AR enables more efficient training, wider knowledge sharing, and better first-time fix rates. Through the bundled offering, maintenance, for example, can receive digitized work instructions containing real-time performance and service history information so technicians can better diagnose and fix equipment correctly the first time.
FactoryTalkInnovationSuite.com
by Gary Mintchell | Nov 9, 2018 | Automation, Industrial Computers, Internet of Things
Advantech has been appearing on a variety of lists of prominent Internet of Things suppliers. The Taiwanese computer company with a US office in Cincinnati, OH and intellectual leadership, supplies intelligent I/O, a variety of computing devices, and HMI devices.
Several years ago I was privileged to be invited to Suzhou, China to attend Advantech’s user conference. It was an impressive event. This year they called it the “first IoT Co-Creation Summit.”
More than five thousand Advantech clients and partners from around the world attended the summit. Here Advantech introduced its newest IoT platform structure WISE-PaaS 3.0 and 32 IoT solution ready packages (SRPs) co-created with software and industry partners.
The event in itself will aid in the software/hardware integration for various industries, connect and build a complete industrial IoT ecosystem and value chain, and allow Advantech and partners to officially step into the next IoT stage.
Advantech Chairman KC Liu stated that in view of IoT application characteristic’s diversity and fragmented market, Advantech has assisted industries in integrating and connecting existing hardware and software and regards creating a complete industry value chain as its primary task in IoT industry development.
Advantech is introducing new features for its WISE-PaaS 3.0 and sharing a number of IoT solution ready packages (SRPs), based on WISE-PaaS, developed with numerous co-creation partners. The company is also outlining future co-creation strategies and schedules for the upcoming year.
Allan Yang, Chief Technology Officer at Advantech said, “While IoT is currently flourishing and many companies have invested in connectivity and data collection equipment, we are still in the early stages of generating value from IoT data. Since WISE-PaaS launched in 2014, Advantech has continued its integration and improved connectivity with open source communities. Our IoT software modules are developed to create operational cloud platform services oriented around the commercial value generated by data acquisition. Data-driven innovation has thus become the main target for our WISE-PaaS evolution.
WISE-PaaS 3.0 offers four main function modules:
- WISE-PaaS/SaaS Composer: a cloud configuration tool with visible workflow. WISE-PaaS/SaaS Composer supports customized component plotting for simple and intuitive 3D modeling application and interaction. It updates views at millisecond rates and, together with WISE-PaaS/Dashboard, presents critical management data in a visually intuitive display to help extract valuable data and improve operational efficiency.
- WISE-PaaS/AFS (AI Framework Service): an artificial intelligence training model and deployment service framework. The WISE-PaaS/AFS provides a simple drag and drop interface that allows developers to quickly input industrial data. When combined with AI algorithms, the service builds an effective inference engine with automatic deployment to edge computing platforms. AFS offers model accuracy management, model retraining, and automated redeployment. It simultaneously controls multiple AI models in the application field; offering automated model accuracy improvements and life-cycle management services.
- WISE-PaaS/APM (Asset Performance Management): an equipment network connection remote maintenance service framework. WISE-PaaS/APM connects to a wide array of on-site industrial equipment controls and communication protocols. It supports the latest edge computing open standard, EdgeX Foundry, and includes built-in equipment management and workflow integration templates. Jointly with the AFS, APM accelerates Machine to Intelligence (M2I) application development.
- Microservice development framework: WISE-PaaS contains a micro service development framework to help developers rapidly create program design frameworks while reducing development requisites. Micro service functions, such as service finding, load balancing, service administration, and configuration center, all offer built-in flexible support mechanisms.
Advantech recently established a water treatment system, jointly developed with GSD (China) Co., Ltd., and a CNC equipment remote operation service, jointly developed with Yeong Chin Machinery Industries Co. Ltd. Both partnerships demonstrate how industrial digital transformations, led by Advantech and its partners through the co-creation model, offer innovative win-win IoT solutions.
Advantech’s IIoT iAutomation Group has launched a broad selection of rackmount GPU Servers from 1U to 4U. The SKY-6000 GPU server series are powered by Intel Xeon scalable processors and each of these highly scalable GPU-optimized servers support up to five NVIDIA Tesla P4 GPUs. IPMI management functions and smart fan control ensure better temperature control and thermal management environments. Every GPU pair includes one high-speed PCIe slot for highly parallel applications like artificial intelligence (AI), deep learning, self-driving cars, smart city applications, health care, high performance computing, virtual reality, and much more.
AI Deep Learning GPU Solution
With support for up to five pcs of half-length half-height (HHHL) GPU cards or one full-height full-length (FHFL) double deck card, plus one full-height half-length (FHHL) GPU card, the SKY-6100 series are designed for NVidia Tesla P4 HHHL GPU cards, making it the best choice for deep learning applications.
IPMI Server Management
With IPMI 2.0 support, the SKY-6000 series allows users to monitor, manage, and control servers remotely and receive alerts if any sensors detect device or component faults. In addition, event logs record important information about the server which can be controlled remotely using the IPMI KVM.
Smart Fan Control
The optimized thermal design separates the CPU and GPU fan zones, making sure the GPU card is not preheated or thermally affected by any other heat source. Also, with the smart fan control mechanism, fan speeds are controlled based on different CPU and GPU workloads and ambient temperature. This feature lowers the acoustic noise of GPUs that have heavy loading but not CPUs. Advantech’s SKY-6000 server series are available for order now.
by Gary Mintchell | Oct 24, 2018 | Automation, Process Control
Our schedules finally aligned and I was able to catch up with Ed Harrington, director of the Open Process Automation Forum for The Open Group. A few months ago I talked with Gary Freburger and Peter Martin of Schneider Electric’s process automation unit. We discussed the OPAF and what had been going on since the ARC Forum in Orlando last February.
OPAF has laid out an ambitious agenda moving automation toward an era of open connectivity and interoperability.
The original plan broached a couple of years ago at ARC Forum by representatives of ExxonMobil and Lockheed Martin was to prod suppliers into reducing the problem of upgrading systems in the field without the huge expense of rip-and-replace. Considerable industry jockeying ensued. Schneider Electric (Foxboro) eventually taking a leadership position in the effort with assistance from Yokogawa and to a degree Siemens. Other suppliers are watching and evaluating.
Smaller suppliers such as Inductive Automation have become involved along with some of the major automation systems suppliers.
The OPAF specification is really a standard of standards. The group wishes to build upon existing standards, assembling them in such a way as to advance the cause of open automation.
Harrington told me that so far this year, the group has published three items (that are open to the public). One is a business guide, The Open Process Automation Business Guide: Value Proposition and Business Case for the Open Process Automation Standard.
The industrial control systems that manufacturers use to automate their processes are critical to the company’s productivity and product quality. To increase the business contribution from control systems, manufacturers need:
1. Increases in operational benefits from improved capabilities
2. Improvements in cybersecurity compared to currently available systems
3. Reductions in the system’s capital and lifecycle costs
The organization has also published The Open Group Snapshot—Open Process Automation Technical Reference Model: Technical Architecture and a white paper Requirements for an Open Process Automation Standard.
Harrington also told me to expect an announcement of further work at next week’s Open Group Quarterly Meeting in Singapore.
I have seen a number of these initiatives in my career. Few succeed in entirety. However, the thinking that goes into this work always moves industry forward. I don’t know if we’ll ever see a truly OPAF control system. Anything that brings more rationality to the market keeping in minds the goals of OPAF will do much for helping manufacturers and producers improve performance. And that’s what it’s all about.
by Gary Mintchell | Oct 19, 2018 | Internet of Things, News, Organizations
News from EdgeX Foundry including an open marketplace for IoT Edge Computing. This is an interesting extension to the platform. Also, Intel has joined the consortium.
At a glance:
- EdgeX Foundry Seeds an Open Marketplace for IoT Edge Computing with New Developer Kits and Smart Building Automation
- Community Demo at IoT Solutions World Congress
- Intel, Redis Labs, ZEDEDA and five other tech influencers commit to IoT interoperability and join EdgeX’s mission to create a unified edge ecosystem
EdgeX Foundry, an open-source, vendor-neutral project that enables an ecosystem of plug-and-play components to unify the IoT edge computing marketplace, announced the availability of EdgeX-enabled developer kits and a Smart Building Automation Community Demonstrator that will debut at IoT Solutions World Congress on October 16-18 in Barcelona.
Hosted by The Linux Foundation, the EdgeX platform is architected to run on any hardware or operating system and unify components coded in any programming language to accelerate time to market and simplify the deployment of secure IoT solutions. The framework serves as a de facto standard to bring together any mix of existing connectivity protocols with an ecosystem of heterogeneous value-add applications.
Developer kits are important tools for building new applications and solutions. A variety of dev kits are already on the market; however, the majority of these kits lock the developer into a particular back-end platform or cloud. In comparison, dev kits based on the EdgeX framework will provide developers with the freedom to choose from an ecosystem of components bound together by the EdgeX interoperability APIs.
“With the emergence of these dev kits, developers will have the opportunity to prototype with their choice of ingredients while taking advantage of plug-in components from EdgeX’s growing vendor-neutral ecosystem,” said Jason Shepherd, EdgeX Foundry Governing Board Chair and Dell Technologies IoT and Edge Computing CTO. “This allows them to focus on innovation rather than reinvention, in addition to being able to add and exchange components at any time to optimize their solution throughout the development and deployment lifecycle.”
There will be two different kinds of dev kits – community and commercial. For options in the community track, the bill of materials will be purchased independently online, the code will be downloaded straight from a special repository on the project GitHub, and questions will be answered through forums like the EdgeX Rocket Chat. The first kit is based on the Samsung Artik with Grove sensor, and options will grow through community contributions over time.
The commercial track for the dev kits will provide EdgeX members with the ability to seed the emergence of an open marketplace for IoT edge computing. These kits will offer end users with attractive options to get started with professional support so they can focus on their preferred value-add rather than supporting open source code. Commercial options will include kits based on supported versions of the EdgeX framework itself (neutral to any plug-in value add), kits based on specific IoT platforms, and microservice plug-ins for value-add such as analytics, data orchestration and security.
EdgeX Foundry is debuting a new community demo at IoT Solutions World Congress that will highlight the platform’s ability to bring together heterogeneous solution components. This first community demo showcases how EdgeX can bring together a real-world, smart flexible office space environment based on components from a variety of vendors leveraging numerous connectivity standards, operating systems and hardware types.
The growth and diversity of the EdgeX ecosystem over the last year has helped the technical community hit major milestones including the “California” release, which made the switch to Golang for the baseline reference implementation. Since the release in April, EdgeX Foundry unique code contributions from members and non-members alike have more than doubled to 70 on a regular basis.
These contributors have played a major role in the upcoming “Delhi” release, which offers major enhancements including the first management features, more security functionality such as access control and improved security bootstrapping, C and Golang-based Device Service SDKs and a reference GUI for demos and simple deployments. Projected to launch in November, the Delhi code will be well-suited for end users to begin developing commercial offers and production deployments. To find more details about Delhi or the EdgeX roadmap, visit the wiki here.
Intel joins the EdgeX Ecosystem
“Today’s announcement represents one more step in Intel’s open source journey and increased role in the advocacy, use and contribution across the ecosystem,” said Stacey Shulman, chief innovation officer for Retail Solutions at Intel. “Intel’s involvement in EdgeX Foundry will help drive scale and accessibility of solutions for both our customers and businesses of all sizes.”
Other new EdgeX Foundry project members include Basking Automation GmbH, Beijing University of Posts and Telecommunications (BUPT), DATA AHEAD, CertusNet, Redis Labs, the Federal University of Campina Grande (UFCG) /Embedded Lab, Windmill Enterprise and ZEDEDA.
“We’re standing at a critical point for digital transformation,” said Shepherd. “The massive volume of devices coming online represents a huge opportunity for innovation and is making edge computing a necessity. We need an open, cloud-native edge ecosystem enabled by EdgeX to minimize reinvention and facilitate building and deploying distributed, interoperable applications from the edge to the cloud. We’re thrilled to welcome these new member organizations into our already strong community that shares the same commitment to open collaboration and innovation.”
by Gary Mintchell | Oct 16, 2018 | Automation, Process Control, Technology
This week is another week on the road—five out of the last six—and now I’m in Chicago at Pack Expo. Much like IMTS, Pack Expo fills three halls of McCormick Place with machines. And machine components such as controls, drives, software, instrumentation, and the like.
Two weeks ago was Emerson Global Users Exchange. I wandered into the Emerson Automation Solutions booth not expecting much that was new. OK, got that one wrong.
If you want an indicator that Emerson has seriously expanded beyond oil & gas, keep on reading. It is now a serious player in this space, as well.
I once was an executive with a company that designed and built automated assembly machines. One interesting niche we had was an expert in helium mass spectrometry leak testing. I can give the sales pitch on the value of in-line, 100% testing of products.
Well, not as good as when Emerson explained its new food and beverage leak detection system.
Emerson’s RosemountTM CT4215 uses laser technology to detect leaks, reject defective packages with no production slowdown.
The Rosemount CT4215 is the first quantum cascade laser/tunable diode laser (QCL/TDL) continuous, inline detection system designed to help assure quality and safety, maximize production volume and decrease product waste for food and beverage products. The Rosemount CT4215 tests the seal and integrity of every bottle or package on a production line, detecting leaks at a sensitivity as low as 0.3 mm and automatically rejecting any defective bottle or package without slowing down production. This is in contrast to the traditional practice of testing occasional grab samples, which can leave a manufacturer vulnerable to low quality, unsafe food or beverages, reduced profitability and damaged reputation.
“In an industry being driven by an increasing consumer awareness of freshness and safety, manufacturers need solutions that allow them to assure these qualities while maintaining, or even increasing, efficiency,” said Peter Watmough, global leak detection product manager, Emerson Automation Solutions. “The Rosemount CT4215 provides packagers with an easy-to-install, easy-to-use assurance of freshness and safety. For the first time, food and beverage packagers can measure every package and bottle for leaks without having to compromise their production speed.”
Emerson further unveiled a new line of transmitters designed specifically for hygienic applications in the food and beverage industry with a compact form factor that will enable manufacturers to minimize downtime and lower production costs.
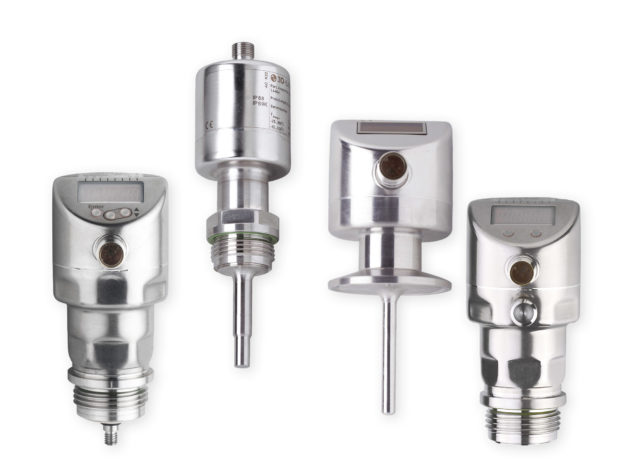
The new line of transmitters—Rosemount 326P Pressure, Rosemount 326T Temperature, Rosemount 327T Temperature and Rosemount 326L Level instruments—are designed to operate in the hygienic environments required by food and beverage manufacturers:
All comply with 3-A and FDA specifications, and are available with nine common industry process connections to ensure the right fit for new tanks and pipe fittings, as well as capability to be retrofitted on legacy systems. The new, small transmitters also can be mounted in tighter locations common on packaging machinery. Conventional 4-20 mA outputs and IO-Link connectivity make the transmitters easy to integrate with automation systems.
To give a sense of the breadth of Emerson Automation Solutions commitment to the space, following are some summaries of products.
Emerson’s ASCO G3 Fieldbus Electronics completely modular system plugs together via mechanical clips that allow easy assembly and field changes without dismantling the entire manifold, and its modules can be used in centralized or distributed applications.
One particular demonstration that will feature G3 Fieldbus Electronics is Emerson’s ASCO Bread Packing Machine. This state-of-the-art system provides full pneumatic automation control to ensure high-speed, repeatable packaging of food products. Its G3 Fieldbus integrates pneumatic control and provides real-time diagnostic data via an integrated webserver. It demonstrates flexible and energy-efficient design through proper sizing of pneumatic systems to fit any food packaging operation.
Emerson’s SolaHD Power Quality solutions remove limitations in the power architecture, allowing machine designers and operators to safely put power where they need it. These power supplies can be mounted directly on a machine, freeing packaging lines from design constraints; eliminating the complexity and cost of unnecessary enclosures and excess wiring; and providing the power for current and future automation capabilities.
Emerson’s Branson Ultrasonic Automated Cutting System provides precise food portioning with an almost frictionless cutting surface resulting in cleaner cuts, faster processing, minimal waste, longer blade life, higher productivity for greater throughput, and reduced downtime for cleaning.
Emerson helps packaging operations reduce process variation and decrease costly losses through technologies that deliver real-time insight into machine and process performance. With the accurate, relevant data in hand, packaging operations can achieve better reliability, reduce losses and contamination as well as ensure long-term performance.
With Emerson’s Micro Motion Filling Mass Transmitter (FMT), high-value packaging lines can accurately fill a wide range of container sizes and products with a single meter, eliminating the cumulative error associated with multiple-device measurement solutions. The Micro Motion FMT reliably measures fluids with entrained solids or gases or with changing viscosities, making it ideal for high-speed filling and dosing applications. Its Coriolis mass-based measurement is immune to variations in process fluid, temperature or pressure, and Automatic Overshoot Compensation (AOC) ensures repeatable fills even under valve performance changes. In addition, the Micro Motion FMT enables operators to track quality control and filling valve-performance data in real time to reduce filler maintenance and cost.
In addition, Emerson’s Micro Motion Multiphase Flow Meter technology can help complex process operations reliably log Gas Void Fraction and liquid density and concentration measurements. Utilizing Micro Motion Advanced Phase Measurement software, these meters also tolerate “real life” conditions of foaming, end-of-batch cavitation or slug flows to enable consistent measurements in challenging multiphase conditions. In addition, Smart Meter Verification delivers detection of coating or fouling within the meter for added clean-in-place efficiency and insight.
An interactive display illustrating pneumatics and IIoT features Emerson’s AVENTICS Smart Pneumatics Monitor, an IIoT hub allowing local data collection and analysis independent of the controller. The pick-and-place display illustrates “predictive maintenance” by showing the health and performance of valves, cylinders and shocks, which can minimize the risk of unplanned machine downtime to increase ROI.
To demonstrate how operators can protect personnel and reduce risk without impacting productivity. the Emerson booth will feature the Emerson ASCO 503 Series Zoned Safety Manifold (with G3 fieldbus electronics). It simplifies the design of a redundant pneumatic safety circuit with a manifold system that can be configured to shut down air and power only to the group of valves that controls the machine’s motion in the operator’s vicinity while the rest of the machine remains in operation. Multiple independent safety circuits can easily and cost-effectively be designed into a single pneumatic valve manifold, reducing the number of safety system components by up to 35 percent, requiring less plumbing, and shrinking the size of a safety system so that valuable real estate within the machine and manifold can be used for other purposes while still providing enhanced operator safety.