by Gary Mintchell | Apr 24, 2018 | Automation, Manufacturing IT, Technology
Most of my time involves Hewlett Packard Enterprise (HPE) where I am devoting about 2.5 hours a day to interviews. As one person asked, what does HPE have to offer. Briefly described, HPE has a variety of compute devices, services, and partnerships.
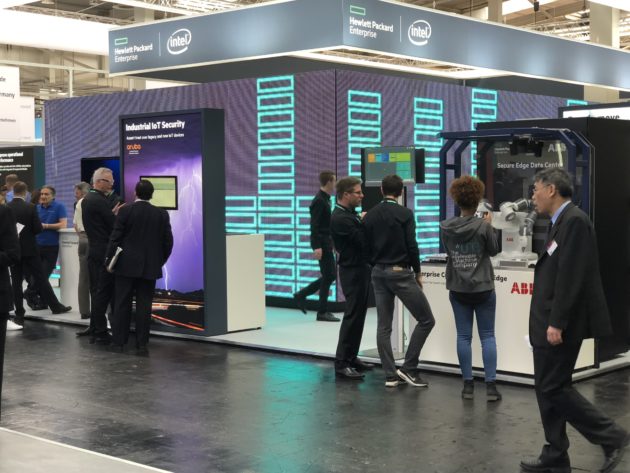
One application was a prescriptive maintenance solution where IoT data is analyzed and the CMMS is notified to initiate a work order. We are not in the era of self-healing machines, yet, but we are one step closer where the machine can begin a maintenance workflow with information about what to repair.
The SecureEdge Data Center combines enclosures from Rittal, I/O from ABB, and Edgeline edge computing hardware from HPE into a scalable industrial center to provide IIoT data to the enterprise from ABB robotics and automation.
As a former machine vision integrator, I loved the video analytics demo application showing Relimetrics software to analyze servers in manufacturing. In this case, the application read a 2D barcode to determine the build, discovered the bill of materials, and then checked that all the proper components were in the assembly, that everything was properly installed, and there were no other defects.
One application of Edgeline edge compute devices, for example, is in partnership with National Instruments to accomplish complex testing at the edge with communication to the cloud as necessary. Edge compute is also important in autonomous vehicles where decisions must be quickly executed locally, but large amounts of data must also be communicated to the cloud for further analysis.
Speaking of partnerships, HPE has forged significant partnerships in the industrial world with ABB, GE Digital, OSIsoft, PTC (Kepware and ThingWorx), Rittal, and Schneider Electric. Most of these involve a significant IT infrastructure including power at the Edge from HPE along with data and connectivity plus solutions targeted to various industrial applications.
by Gary Mintchell | Apr 20, 2018 | Internet of Things, News
Partnerships are huge. Especially with industrial automation and software suppliers extending their reach into the enterprise. Here, press releases from rivals Rockwell Automation and Siemens exemplify the pattern. Additionally, this week, I’ve also interviewed Cisco and Intel. Things are getting interesting this spring. We’ll see what I can report back from next week’s Hannover Messe.
Rockwell Automation and Cisco have released new network design guides and white papers to help companies connect mobile devices and deploy end-to-end cloud connectivity while maintaining security best practices. The guides give companies best practices for wired and wireless network architectures when deploying cloud and mobile industrial IoT solutions. The free resources are the latest addition to the Converged Plantwide Ethernet (CPwE) program.
Secure Mobile Connections
The new Identity and Mobility Services guide will help companies connect mobile devices in a way that manages security risks. The guide, based on the Cisco Identity Services Engine platform, supports industrial security by identifying, authorizing and posturing mobile connections at three levels: device, application and user. The guide also helps users establish unified and autonomous WLAN architectures and manage self-service wireless access.
“Mobile devices are changing how we see and manage production,” said Gregory Wilcox, global technology and business development manager, Rockwell Automation. “Workers are accessing analytics on tablets to make better production decisions, even when they’re away from equipment. And they’re using innovations like the FactoryTalk TeamONE app from Rockwell Automation to collaborate through their smartphones. The Identity and Mobility Services guide will help bring these capabilities to life in their facilities while maintaining a strong security stance.”
Connect to the Cloud
The new Cloud Connectivity guide provides guidance for using the FactoryTalk Cloud gateway to establish a more secure connection from the plant floor to cloud-based applications, like FactoryTalk Analytics for Machines. This end-to-end connectivity is essential to deploying capabilities like remote monitoring and support. The design guide addresses the varying levels of security measures that should be considered for small to large companies.
“Industrial companies sometimes focus a lot of their attention on creating an information pathway to the cloud but overlook critical security needs,” said Todd Gurela, senior director, Industry Solutions Group, Cisco. “The Cloud Connectivity design guide will help companies establish end-to-end cloud connectivity while protecting both data paths and the plant network against cyber threats.”
Meanwhile Orange and Siemens
Orange Business Services and Siemens have joined forces to drive the adoption of the Internet of Things (IoT) in the industrial sector by simplifying integration and promoting IoT innovation. The initial focus will be to develop solutions around asset tracking and asset monitoring to optimize the supply chain and improve efficiencies, as well as to develop digitally enhanced products to increase customer satisfaction and create new business models.
The partnership will help businesses connect their machines and physical infrastructure to the digital world, allowing them to translate the wealth of data they produce into business results. Advanced analytics and digital services will help them increase productivity and efficiency across their business.
Orange Business Services brings its global cellular connectivity, consulting, system integration and application development skills to the partnership. The alliance is built around Siemens’ MindSphere, the cloud-based open IoT operating system, and Datavenue, the Orange IoT and data analytics modular offering.
Customers have the option of pre-packaged offerings such as asset tracking, or customized solutions and applications. Orange Business Services will initially provide connectivity components from Datavenue, including cellular and Low Power Wide Area (LPWA) networks. Other Datavenue components will follow.
The partnership will initially focus on Europe, starting with solutions to be rolled out in Germany and Austria.
by Gary Mintchell | Apr 19, 2018 | Asset Performance Management, Automation, Internet of Things, Operations Management
Artificial Intelligence, always known as AI, along with its sometime companion robots leads the mainstream media hype cycle. It’s going to put everyone out of jobs, destroy civilization as we know it, and probable destroy the planet.
I lived through the Japanese robotic revolution-that-wasn’t in the 80s. Media loved stories about robots taking over and how Japan was going to rule the industrialized world because they had so many. Probing the details told an entirely different story. Japan and the US counted robots differently. What we called simple pick-and-place mechanisms they called robots.
What set Japanese industrial companies apart in those days was not technology. It was management. The Toyota Production Method (aka Lean Manufacturing) turned the manufacturing world on its head.
My take for years based on living in manufacturing and selling and installing automation has been, and still is, that much of this technology actually assisted humans—it performed the dangerous work, removing humans from danger, taking over repetitive tasks that lead to long-term stress related injuries, and performing work humans realistically couldn’t do.
Now for AI. This press release went out the other day, “With AI, humans and machines work smarter and better, together.” So, I was intrigued. How do they define AI and what does it do?
Sensai, an augmented productivity platform for manufacturing operations, recently announced the launch of its pilot program in the United States. Sensai increases throughput and decreases downtime with an AI technology that enables manufacturing operations teams to effectively monitor machinery, accurately diagnose problems before they happen and quickly implement solutions.
The company says it empowers both people and digital transformation using a cloud-based collaboration hub.
“The possibility for momentous change within manufacturing operations through digital transformation is here and now,” said Porfirio Lima, CEO of Sensai. “As an augmented productivity platform, Sensai integrates seamlessly into old or new machinery and instantly maximizes uptime and productivity by harnessing the power of real time data, analytics and predictive AI. Armed with this information, every person involved – from the shop floor to the top floor – has the power to make better and faster decisions to increase productivity. Sensai is a true digital partner for the operations and maintenance team as the manufacturing industry takes the next step in digital transformation.”
By installing a set of non-invasive wireless sensors that interconnect through a smart mesh network of gateways, Sensai collects data through its IIoT Hub, gateways and sensors, and sends it to the cloud or an on-premise location to be processed and secured. Data visualization and collaboration are fostered through user-friendly dashboards, mobile applications and cloud-based connectivity to machinery.
The AI part
Sensai’s differentiator is that it provides a full state of awareness, not only of the current status, but also of the future conditions of the people, assets and processes on the manufacturing floor. Sensai will learn a businesses’ process and systems with coaching from machine operators, process and maintenance engineers. It will then make recommendations based on repeating patterns that were not previously detected. Sensai does this by assessing the team’s experiences and historical data from the knowledge base and cross checking patterns of previous failures against a real-time feed. With this information, Sensai provides recommendations to avoid costly downtime and production shutdowns. Sensai is a true digital peer connecting variables in ways that are not humanly possible to process at the speed required on a today’s modern plant floor.
About the Pilot Program
Participation in Sensai’s pilot program is possible now for interested manufacturers. Already incorporated throughout Metalsa, a leading global manufacturer of automotive structural components, Sensai is set to digitally disrupt the manufacturing industry through AI, including those in automotive, heavy metal and stamping, construction materials, consumer goods and more.
Porfirio Lima, Sensai CEO, answered a number of follow up questions I had. (I hate when I receive press releases with lots of vague benefits and buzz words.)
1. You mention AI, What specifically is meant by AI and how is it used?
Sensai uses many different aspects of Artificial Intelligence. We are specifically focused on machine learning (ML), natural language processing (NLP), deep learning, data science, and predictive analytics. When used together correctly, these tools serve a specific use case allowing us to generate knowledge from the resulting data. We use NLP to enable human and computer interaction helping us derive meaning from human input. We use ML and deep learning to learn from data and create predictive and statistical models. Finally, we use data science and predictive analytics to extract insights from the unstructured data deriving from multiple sources. All of these tools and techniques allow us to cultivate an environment of meaningful data that is coming from people, sensors, programmable logistics controllers (PLCs) and business systems.
2. “Learn processes through operators”—How do you get the input, how do you log it, how does it feed it back?
Our primary sources of data (inputs) are people, sensors, PLCs, and business systems. In the case of people on the shop floor or operators, we created a very intuitive and easy to use interface that they can use on their cellphones or in the Human Machine Interfaces (HMIs) that are installed in their machines, so they can give us feedback about the root causes of failures and machine stoppages. We acquire this data in real-time and utilize complex machine learning algorithms to generate knowledge that people can use in their day-to-day operations. Currently, we offer web and mobile interfaces so that users can quickly consume this knowledge to make decisions. We then store their decisions in our system and correlate it with the existing data allowing us to optimize their decision-making process through time. The more a set of decisions and conditions repeats, the easier for our system is to determine the expected outcome of a given set of data.
3. Pattern? What patterns? How is it derived? Where did the data come from? How is it displayed to managers/engineers?
We create “digital fingerprints” (patterns) with ALL the data we are collecting. These “patterns” allow us to see how indicators look before a failure occurs, enabling us to then predict when another failure will happen. Data comes from the machine operators, the machines or equipment, our sensors, and other systems that have been integrated to Sensai’s IIOT hub.
We trigger alerts to let managers and engineers know that a specific situation is happening. They are then able to review it in their cellphones as a push notification that takes them to a detailed description of the condition in their web browser where they can review more information in depth.
4. What specifically are you looking for from the pilots?
We are not a cumbersome solution, for us is all about staying true about agility and value creation. We look for pilots that can give us four main outcomes:
– Learn more about our customer needs and how to better serve them
– A clear business case that can deliver ROI in less than 6 months after implementation and can begin demonstrating value in less than 3 months.
– A pilot that is easy to scale up and replicate across the organization so we can take the findings from the pilot and capitalize them in a short period of time.
– A pilot that can help Sensai and its customers create a state of suspended disbelief that technology can truly deliver the value that is intended and that can be quickly deployed across the entire organization.
by Gary Mintchell | Apr 17, 2018 | Automation, News
My latest email from The Information highlighted the woes and tribulations of Tesla. There are headlines in all the major media outlets—manufacturing problems at Tesla impacting stock price, profitability, and cash flow.
How would you like to be the engineers who “over automated” the factory according to the boss (Elon Musk)? Want to be the Director of Manufacturing hung out to dry in the Wall Street Journal or The New York Times?
Just consider all this and see how you matter to the company—the employees, stockholders, customers.
From The Information quoting Reveal:
Tesla’s 2018 is starting to look like Uber’s 2017: Every week there is a new allegation or setback about workplace culture or business performance or the quality of its products. In this case, an investigative report by Reveal says that Tesla consistently under-reported ailments suffered by workers at its main production plant. “Everything took a back seat to production,” said a former safety manager, Justine White, who left at the start of 2017. “It’s just a matter of time before somebody gets killed.” Tesla, as is its custom, fired back by calling the report by Reveal, which is part of the nonprofit Center for Investigative Reporting, a tool of an “extremist organization” that is trying to unionize Tesla’s workers and that reporters misunderstood how injuries are reviewed. We suggest reading the Reveal report and Tesla’s response, and coming to your own conclusion. (the Reveal)
And another quote from The Information about a class action lawsuit where the former director of manufacturing is giving information to the plaintiffs.
It’s not common for a shareholder class-action lawsuit, typically filed after a stock’s value has fallen precipitously, to get buzz among reporters. But this one against Tesla and its CEO Elon Musk seems unique: No fewer than 11 former workers at Tesla, including an ex-director of manufacturing at the company’s main car-production plant, provided information to the plaintiffs’ lawyers who filed the suit, according to an amended filing from March 23. It alleges Musk knowingly made false statements to investors that Tesla would be able to make 5,000 Model 3 sedans per week by the end of 2017, despite being told by his subordinates that that would never happen and continued to do so in the face of mounting evidence. Tesla’s stock dropped in price by 20% between May 2017 and November of that year, after it became clear that production target would not be met—not by a long shot. Five months later, the production pace is about 2,000 per week, Tesla has said. A spokesman for the company didn’t immediately respond to a request for comment about the suit, which is worth reading.
We have an important role within our companies. We must always consider that. Sometimes even being required to tell overoptimistic executives the reality of manufacturing.
by Gary Mintchell | Apr 16, 2018 | Productivity
You know the stereotype of the creative genius who it spontaneous, keeps odd hours, disappears for a time. Let us blast that stereotype. This weekend I leave for Germany and another trip through the labyrinth of Hannover Messe. Typically at trade fairs, we are exposed to the fruits of a year’s labor developing new products. These will be touted with words such as creative, ground-breaking, unique, Few, in reality, will be that extreme. Many will be useful. Maybe a few will push a boundary. Maybe a couple will break new ground. I will be in search for the creative.
Curious about creativity, I read through Essentialism: The Disciplined Pursuit of Less by Greg McKeown Sunday morning. By the way, the pursuit of less (simplicity) is itself a fruitful discipline.
He quotes Charles Duhigg (The Power of Habit), “Routine…In fact the brain starts working less and less. The brain can almost shut down… And this is a real advantage, because it means you have all this mental activity you can devote to something else.”
Ah, routine. I glanced at the clock as I depressed the plunger on the French Press this morning. 5:51 am. That is plus or minus five minutes from every day as I prepare the morning’s coffee for Bev and me (except today it’s all mine–she’s traveling). Then I sit down with a light breakfast and gather my thoughts for a couple of posts.
Back to McKeown. He cites Mihaly Csikszentmihalyi in his classic Flow: The Psychology of Optimal Experience, said, “Most creative individuals find out early what their best rhythms are for sleeping, eating, and working, and abide by them even when it is tempting to do otherwise. They wear clothes that are comfortable, they interact only with people they find congenial, they do only things they think are important. Of course, such idiosyncrasies are not endearing to those they have to deal with… But personalizing patterns of action helps to free the mind from expectations that make demands on attention and allows intense concentration on matters that count.”
Maybe try:
- Get adequate sleep
- Rise, drink water, move a little
- Meditate, read something spiritually oriented, pray
- Light breakfast with some protein
- Exercise
- Get ready for the day
Go with the flow! Decide many things ahead of time so that more energy is available for real work–Deep Work as Cal Newport describes it.