by Gary Mintchell | Oct 21, 2020 | Asset Performance Management, Operations Management
If I receive a press release without either “partnership” or “AI” in it, it will be the featured news for a week. Of course, I’m all about digital. Now that we’re past all the releases about what technology companies are doing to help protect workers from Covid, those are the keywords. This news highlights an interesting partnership between AVEVA and Chemical Business SCG to promote something called “digital reliability.” And reliability is a key requirement for technologies ever since the invention of the plow.
Strategic collaboration between the organizations extends the Engineering Digital Twin and harnesses AI-Infused Asset Performance Management to prevent unplanned downtime
AVEVA and Chemicals Business, SCG, one of the largest petrochemical companies in Thailand and a key industry player in Asia, have announced their strategic partnership to develop a Digital Reliability Platform (DRP), a complete asset performance management (APM) solution to predict equipment health, monitor performance, and enable advanced maintenance across its operations to eliminate unplanned downtime. The DRP was completed through collaborative effort. This partnership matched the company’s broader digital transformation imperative to become a data-driven organization to advance its position as a leader in the petrochemical industry and to also take the DRP solutions to the market
Asset reliability is critical for asset intensive businesses such as petrochemicals. Unplanned shutdowns cause significant negative impacts on petrochemical value chains. Digital transformation initiatives enable businesses to address this risk by harnessing data to build and deploy an advanced APM solution to monitor critical assets and predict failure towards a goal of zero unplanned shutdowns. The solution integrates online and offline equipment data to visualize plant performance, enhance workforce efficiency, and apply artificial intelligence (AI) for predictive maintenance and resolution.
“This is a great achievement for Chemicals Business, SCG since reliability is a critical element to our business. With the innovative approach of the Digital Reliability Platform, we will ensure that we can eliminate the business risks posed by unplanned downtime. In our quest for a partner, AVEVA was the only company to provide an end-to-end solution spanning engineering, operations, and maintenance. With the DRP, we have successfully brought together big data, AI, machine learning, and predictive analytics into a practical solution that will empower our workers and improve our performance,” said Mr. Mongkol Hengrojanasophon, Vice President – Olefins Business and Operations, Chemicals Business, SCG.
“Moreover, this partnership will include launching the Digital Reliability Platform Solutions to the market. This would be the first complete and unique digital solutions which combine both breakthrough technology and industrial specific information,” added Mr. Mongkol.
“Our strategic partnership with Chemicals Business, SCG is a major milestone for us in leveraging the strength of our portfolio to deliver value through digital transformation. We are proud to be part of this collaboration that improves operational efficiency and reliability to achieve zero unplanned downtime by maximizing asset availability with predictive and prescriptive maintenance. The standardized systems and processes defined through this collaboration will also result in improved workforce efficiency,” said Ravi Gopinath, Chief Cloud Officer and Chief Product Officer at AVEVA
The Digital Reliability Platform will bring together digital innovations and practitioner knowledge to increase work efficiency and safety to establish a new competitive standard within the industry.
by Gary Mintchell | Jul 20, 2020 | Asset Performance Management, Manufacturing IT, Operations Management, Software
In brief: Three Organizations Combine Expertise to Bring Digital Twins to Life, Create Added Value, and Deliver Support Across the Asset Lifecycle
The idea of an open system for data flow from engineering through construction to startup to operation & maintenance, and perhaps even to decommissioning has intrigued me for years. I have worked with MIMOSA and its Open Industrial Interoperability Ecosystem for many years. Check it out.
For the most part, suppliers have been a bit slow to this game. The way of the world is that automation vendors never liked the “open” part, since their design emphasizes tight integration of as many parts as possible under their proprietary umbrella.
An ecosystem is one thing, and a partnership is another. Sometimes companies announce partnerships with great flourish and publicity only to see the great promise wither from neglect. Sometimes end users (owner/operators) reap significant benefit.
With that background, I approach the announcement of a partnership. I like the idea, but execution and sustainability will be proof of the strength of this partnership. Note that two of the companies are sort of like “conjoined twins” joined at the hip.
From the announcement:
DORIS Group, global Engineering and Project Management company in the energy industry, Schneider Electric, supplier of products and solutions for digital transformation of energy management and automation, and AVEVA an engineering and industrial software supplier, have agreed to develop a strategic partnership to deliver Digital Twin technology for the upstream oil and gas markets.
These new solutions will support the goals of oil & gas organizations to improve asset performance, increase sustainability and maximize return on capital on projects.
The three companies will combine offerings to bring engineering capabilities, an asset lifecycle software solution and digital specialization in order to create a fully formed digital twin to serve as a backbone for improving performance for the upstream sector. The new solution will:
- Bring new assets on stream faster through the use of cloud-enabled software that improves collaboration and increases engineering efficiencies
- Deliver enhanced safety leading to better business outcomes
- Improve traceability through a single point of accountability
- Enable remote operations and production assurance through a fully functional Living Digital Twin that mirrors all aspects of the operating asset
Oil & Gas owner operators have struggled to go digital due to the lack of a structured offering and orchestration as no single vendor currently delivers what is required to achieve this. Large amounts of data of various types, from different sources is another challenge they face, often leading to data inaccuracy and incompatibility, as well as difficulties in organizing that data and identifying trends.
Similarly, the oil & gas sector is under considerable pressure to quantify, track and reduce CO2 emissions as well as reduce overall pollution – this can be even more difficult with limited monitoring, no established method and no data-driven decision making.
Together, DORIS, AVEVA, and Schneider Electric will offer a structured digital and collaborative solution across the lifecycle of projects that will help oil & gas owner operators address many of these challenges.
Christophe Debouvry, CEO of DORIS Group, stated, “DORIS Group is excited to be strategically partnering with Schneider Electric and AVEVA in this unique venture which will allow us to accelerate the building out of our digital transformation strategy. Combining our complementary expertise will go a long way to providing a powerful enabler to offer our customers embarking on their digital transformational journeys with optimized solutions throughout their assets lifecycle.”
Craig Hayman, CEO AVEVA, also commented, “Leaders driving the next wave of transformation are moving quickly and that’s why this partnership with Schneider Electric and DORIS Group is so opportune. Our common aim is to support organizations on their digital journey especially in the current environment, helping them accelerate the use of digital technology, realize the value of a digital twin and also work towards a more sustainable future. It’s never been easier to begin a digital transformation program, as access to cloud computing, great connectivity, a merged edge and enterprise combined with analytics and machine learning, means that the ability to digitally drive productivity improvements into the industrial world is now unprecedented.”
Christopher Dartnell, President Oil & Gas and Petrochemicals at Schneider Electric, commented, “This partnership is in line with Schneider Electric’s objectives around Digitization and Energy Transition and we will bring our expertise in both energy and process efficiency to the industry. Our goal is to support customers looking to adopt a digital twin model, by offering our experience to facilitate the overall digital transformation for our clients enable them to improve lifecycle performance and safe operations while also making their operations more sustainable.”
by Gary Mintchell | Jun 22, 2020 | Asset Performance Management, Operations Management, Software, Technology
Emerson marketing called us together for a virtual press conference and demonstration of its take on Augmented Reality (AR) integrated with it Plantweb Optics asset performance platform. I’ve seen many demos of AR over the past many years. The technology inspires imaginative thinking, but somehow companies have just not managed to make it ready for prime time.
Emerson’s evidently is. Not only could they show a demo, it is due to be released later this summer with the next release of Plantweb Optics software. Better yet, it does not require glasses or other peripheral equipment other than the smart phone or device people are already using.
The tag line from Emerson: Analytics and live remote assistance improve productivity and safety.
What does it do, really? Well, it delivers enhanced access to real-time diagnostics and analytics, as well as live remote assistance, to industrial plant workers responsible for maintaining and optimizing plant equipment. With AR technology integrated into Plantweb Optics, companies can improve productivity, collaboration and operational performance, without being limited by shortages of skilled workers or travel restrictions.
“Successful digital transformation programs that lead to Top Quartile performance have people and work practices as a key focus. Adopting innovative technology like augmented reality and institutionalizing best practices enable workers to add more value than ever to operational and business performance,” said Stuart Harris, group president for Emerson’s digital transformation business. “With these new Plantweb Optics technologies, customers can experience significant improvements in equipment reliability and the safety of their facilities.”
Plantweb Optics leverages artificial intelligence, machine learning analytics, and data contextualization to provide real-time visibility into plant reliability and operational performance. Unlike standalone AR solutions that require custom engineering, AR is integrated into Plantweb Optics, providing immediate access to a wealth of data and translating into easier, less costly implementation and a faster return on investment. For use by manufacturers in the life sciences, food and beverage, chemical, metals and mining, power and water, pulp and paper and energy industries, Plantweb Optics is part of Emerson’s award-winning Plantweb digital ecosystem of technologies, software and services.
Augmented reality for Plantweb Optics transforms the way field technicians accomplish complex tasks through enhanced situational awareness, live remote assistance and analytics delivered in context of the plant. As a field technician walks an industrial plant with a mobile device, Plantweb Optics uses spatial computing technology to map assets and provide technicians with critical maintenance information relevant to their location. Plantweb Optics overlays real-time analytics, equipment health status and technical support documentation on their field of view, so technicians can safely resolve issues sooner.
The augmented and virtual reality market is projected to grow annually at 40% from 2017 through 2025, according to multiple research reports. Much of this spending will come from manufacturers around the globe using AR technology to help upskill their workforce for digitalized operations.
With live remote assistance, field technicians can be virtually shadowed by experts, either on-site or off-site, from Emerson, their own company or another service provider. Experts can talk, type or augment the technician’s mobile display with graphics to guide the next action. Live remote assistance enables technicians and experts to collaborate for safe troubleshooting and repairs, regardless of location and without travel costs. Live remote assistance sessions, best practices and notes from experienced engineers and step-by-step troubleshooting procedures can be logged into a knowledge library for use by all engineers at a site. The knowledge library is a resource for companies to standardize procedures and ensure engineers of all experience levels understand an asset’s history and are using best practices for safe, efficient operations.
by Gary Mintchell | Jun 19, 2020 | Asset Performance Management, Commentary, Manufacturing IT, News, Software
GE Digital had not updated me for a while. So, an invitation to a conversation with new GE Digital CTO Colin Parris was welcome—even if in the middle of several virtual user conferences. Naturally we talked about digitalization, something GE Digital was early to the game with. Also AI. Digital Twin continues to form the base of the company’s strategy.
Most welcome, there was no talk of optimization and Six Sigma. Instead business transformation through Lean plus Control plus Digital Twin was the focus of conversation.
As an example of the importance of digitization, he discussed a business that was so focused on optimization that it didn’t want to invest in digital. Then COVID came knocking. The company had been reluctant to digitize, but did it in five days when forced to when employees had to work from home. It then improved the system over the ensuing three months.
Here is another example Parris related.
The Prime Minister of India asked citizens to turn off their lights for nine minutes in a show of solidarity in the fight against COVID-19. With meticulous planning by India’s Power System Operation Corporation (POSOCO), national and state agencies, and supported by the GE Digital Grid Software team and Advanced Energy Management System (AEMS) solutions, the nation’s power grid withstood a 31- gigawatt drop and recovery.
When the request came down, POSOCO and its extended team of national and state agencies had less than 60 hours to prepare. For 1.3 billion consumers this would be a simple, yet powerful, way to unite with their fellow countrymen and the world, but it would also put tremendous stress on the nation’s power grid. A sudden decrease in demand could cause grid instability, leading to system collapse.
Due to national lockdowns associated with the pandemic, the normal daily peak demand of 160 GW had already fallen by 50 GW due to the significant reduction in demand from the commercial and industrial sectors. For the April 5 “lights out” event, POSOCO estimated a reduction in demand of 12 GW within two to four minutes. Power systems can handle gradual drops, but a sudden drop caused by lights switching off across the nation risked collapsing the world’s largest synchronous grid. Consumers would expect the power to return at full capacity at the end of the nine-minute vigil.
Preparations to meet the unprecedented reduction in load and recovery began in earnest on April 3 to create and test guidelines for reliable grid operations across POSOCO’s five regions. Hydro and gas generators, which require the least amount of time for ramp-up, were tested the morning of April 5. The Ministry of Power announced that the country’s electricity grid was robust, stable and ready to handle the demand.
At 9:00 pm on April 5, an estimated 80% of the nation’s citizens (approximately a billion people) turned off their lights and illuminated candles, lamps and flashlights in a show of national strength and unity. The resulting power drop and recovery was 31 GW – more than double the projections, but by connecting with control centers remotely, observing key parameters, and continuously monitoring system health, POSOCO was able to provide uninterrupted supply to consumers.
Given India’s strict lockdown response to COVID-19, the GE Digital teams were not able to hold in-person planning meetings, but by using GE Digital’s remote work capabilities, the team’s engineers were able to support POSOCO while working safely from their own homes.
I also received update information about GE Digital’s APM 4.4 (Asset Performance Management).
- GE Digital’s APM 4.4 uses Digital Twins, Advanced Visualizations, and improved Connectivity to help Asset and Process Intensive Companies in Power Generation, Oil & Gas and Chemical Processing Industries to Rapidly Reduce Costs while Adapting to Changing Market Conditions
- Power Generation companies using existing APM solutions enjoy availability / uptime increases of up to 20%; with O&M Cost Reduction up to millions of dollars per year
- Oil & Gas and Chemical Processing companies using APM enjoy up to 6% improvements in availability, up to 40% reductions in reactive maintenance and up to 20% reduction in costs associated with Health, Safety and Environment issues
Available both as a cloud and on-premises solution, APM allows companies in asset and process intensive industries like Oil & Gas, Chemical and Power Generation to align key technologies with critical work processes and functions across their businesses.
This release has focused on driving tighter integration across capabilities within the APM solution as well as to existing systems such as Enterprise Asset Management / Computerized Maintenance Management System (EAM/CMMS) solutions. In addition, APM focuses on automating work processes with enhancements to allow users to automate tasks and provide a more seamless experience to have the right information at the right time to make critical business decisions.
“Our software helps customers to better operate, analyze and optimize their business processes with simplicity, speed and scale,” said Linda Rae, General Manager, GE Digital Power Generation and Oil & Gas. “APM helps industrial companies to efficiently and rapidly reduce costs while adapting to changing market conditions. With more than 30 years’ experience delivering software for our partners in industry, we’re always learning how to help them rise to today’s challenges.”
The latest APM release added more than 30 new Digital Twin blueprints for Oil & Gas, Chemical, Fossil and Nuclear Power Generation as well as Mining, to its catalog of more than 300 pre-configured analytic and diagnostic models for various equipment classes and systems across industries. Built by reliability subject matter experts, the blueprints monitor asset health by detecting degradation or performance loss across the asset or system to provide a diagnostic recommendation. This significantly reduces the time to value for our customers, with built-in detection and remediation information guidance.
Several new reports are also available for predictive diagnostic users including Sensor Health Reporting and the Predictive Diagnostic Coverage report. These help users understand diagnostic coverage relative to an asset’s designed capabilities.
For Predix APM cloud customers, Advanced Visualization capabilities are being introduced to enable rich dashboarding, analysis, and reporting on APM alerts, cases, and more. Dashboards are now available through the integration of a Business Intelligence (BI) tool for additional dashboarding capabilities.
GE Digital has also announced enhancements and unlimited availability of Predix APM for European customers via its Frankfurt, Germany operations center. In partnership with Amazon Web Services (AWS), GE has made technology investments to enhance customer experience and further support GDPR regulations.
The GE Digital APM Roadmap continues to advance the state of technologies for APM as well as features and functions. APM 4.4is now generally available from GE Digital. More information can be found here.
by Gary Mintchell | Jun 5, 2020 | Asset Performance Management, Internet of Things, Technology
Interact Analysis’s new report on the market for predictive maintenance highlights the potential for a new relationship between component manufacturers, OEM machine builders, and end users.
- By 2024, the market for predictive maintenance in motor driven systems is forecast to reach a valuation of $906.1 million
- Enhanced demand for remote monitoring as a result of COVID-19 means there will be no slowdown in market growth
- SaaS is likely to be the main business model for provision of predictive maintenance, and also eases concerns over data ownership
Interact Analysis, my new favorite market research firm, has announced an in-depth examination of the predictive maintenance market. It forecasts a boom in the sector, propelled by the emergence of smart sensors able to monitor crucial parts of a motor-driven system that are not covered by legacy maintenance devices and methods. Advanced smart sensors will allow delivery of viable cloud-based predictive maintenance service packages using a SaaS business model.
One reason I like Interact Analysis right now is methodology. In addition to 40+ hours of primary research interviews, Interact Analysis has utilized data from national manufacturing surveys, as well as data developed for other research areas. This data, combined with the information gathered from interviews, is the base at which estimates are developed.
The report shows that the market for predictive maintenance in 2019 was $117.5 million, largely made up from legacy predictive maintenance products such as portable monitoring devices. Many of these devices will maintain strong growth in the coming decade but will be used in tandem with new technologies such as smart sensors, the latter fueling an expected boom in market value of predictive maintenance technology, up to almost $1 billion in 2024. The significant fall in price of the capacitive based microelectromechanical systems (MEMS) found in Smart Sensors will be one of the drivers of this market.
I like their methodology and analysis—except for forecasting. Predicting future sales is so fraught with uncertainty that I take it as an interesting guide. Evidently sensor manufacturers reported doubling of sales over the two previous years. Look at the numbers and you can see that Interact assumed that doubling to continue through 2024.
When I read through the report synopsis, I was struck by the reliance on smart sensing as a foundation to the market growth for predictive maintenance. I missed a point. They have detected the beginnings of a trend that I have not yet seen. Software-as-a-Service applied to these intelligent devices. Selling the data, not the sensor, so to speak. I’m interested in your feedback on this development. And whether it can drive this market to a billion dollars.
Back to the report:
Smart sensors, which typically monitor sound, temperature, and vibration, may not provide the depth of data offered by some legacy devices, but they have significant advantages. Whereas most legacy devices are attached to motors, IA predicts that only 53% of smart sensors will be attached to motors by 2024. The rest will be attached to other machine components which are also subject to the wear and tear of daily use. This means that the application of predictive maintenance will be far more widespread in the factories of the future.
Blake Griffin, lead analyst on predictive maintenance at Interact Analysis, says: “Smart sensor technology coupled with IIoT capabilities give component manufacturers and OEM machine builders the scope to offer end users an anticipatory service package. For most providers of predictive maintenance, the logical business model will be software as a service. A side benefit of SaaS is that it ties all technologies together under a single solution – thereby eliminating concerns regarding data ownership. Additionally, advancements in embedded machine learning will improve the ability for predictive maintenance to be installed in new or non-standard applications that are less well understood, further fueling growth.”
Adrian Lloyd, CEO of Interact Analysis, adds: “Modern predictive maintenance technology is currently at the beginning of an exponential growth trajectory. Now is a more important time than ever for suppliers to understand key trends at play so they may work at carving out their share of this market – forecast to be worth nearly $1 billion by 2024.”
Griffin further explained the background in a Blog Post. Following are some excerpts.
What are Smart Sensors?
Smart sensors are a fairly new technology that are placed on equipment to gather various data points, most commonly vibration and temperature measurements. Smart sensors then transmit this information wirelessly to a data collector or gateway. When analyzed, this data is particularly useful for assessing the health of equipment as usually the level of vibration and temperature increases as equipment becomes faulty.
How is this Different from Condition Monitoring?
In a traditional condition monitoring system, very little effort is made to determine when equipment will fail, instead relying on set parameters to determine when an asset is at risk of failing. The problem with this approach is that it limits the number of applications which can be monitored. If parameters must be set for an alarm to be triggered, those parameters must be well understood. This decreases the reliability of these systems in applications that are not well understood.
For predictive maintenance to be performed, a level of intelligence must exist somewhere in the plant infrastructure, whether in the form of software, hardware or even application expertise by an experienced operator. A historical log of how the equipment being measured has performed must be utilized to assess if it is trending towards a failure. Increasingly, machine learning algorithms are being utilized to enhance the understanding of the application being measured. This technology utilizes the historical data produced by the smart sensor to better understand and recognize patterns. Having an automated solution for pattern recognition allows for quicker and more reliable detection of anomalies within the data. This not only expands the number of applications able to be monitored beyond just well understood ones, it also increases the amount of time operation managers have to resolve a piece of equipment that is trending towards failure.
Key Driver: A Push for the Realization of Digitalization and IIOT
The most important trend impacting industrial automation is the digitalization of these systems and the equipment within. Over the last 6-7 years, remarkable breakthroughs in technologies that help improve plant efficiency, productivity and reliability have been developed, although uptake so far has been challenging due to the cautious nature of end users when it comes to adopting new technologies.
While these vendors have released software and services aimed at harnessing the benefits of IIoT, it is clear that in order to make use of these solutions, a substantial increase in the number of connected devices is needed. Smart sensors represent an important piece of this puzzle. Since the advent of smart sensors, major automation vendors like ABB, Siemens, WEG, and Nidec have all released their own versions, presumably recognizing the enabling behavior of this technology. We expect this trend to continue as the product is desperately needed in order for manufacturers to begin generating tangible benefits from IIoT technology.
by Gary Mintchell | Apr 6, 2020 | Asset Performance Management, Interoperability, Operations Management, Standards
My inbox has accumulated a plethora of news about open—open standards, open source, open interoperability. Open benefits implementers (end users) because so much thought and work have been done already defining models, data, messaging, and the like that integration time and complexity can be greatly reduced. Yes, integrators remain necessary. But time to production, one of the critical measures of product success, improves. Not to mention time to trouble shoot both during startup and during operation.
Without warning a short time ago, I received a call from Alan Johnston, president (and driving force for many years) of MIMOSA. I attended MIMOSA meetings for several years and served for a year as director of marketing. I was even part of the meeting that birthed the OIIE name and fleshed out the original model. I set up a number of meetings, but we were just a little premature. We needed a bit more momentum from industry and academia to get things going. The reason for Alan’s call was that momentum was growing again. Several organizations in Australia are interested, there is renewed interest from the ISA 95 committee, and the Open O&M Initiative gained new life.
So, I wound up sitting through most of four hours of introductory meeting as the various parties—old and new—talked about what they were working on and where it all needed to go to get the job done. And Alan was right. Progress has evolved. It’s time to talk about this again.
Benefits
The driving force for this work continues to be fostering interoperability and data/information flow among the major applications behind the design, construction, and operation & maintenance of a plant—engineering, operations, maintenance. Any of us who have ever searched for the current and correct information/specification of a piece of the process facing impending unplanned shutdown understand almost intuitively the critical nature of this work. (See the Solutions Architecture diagram.)
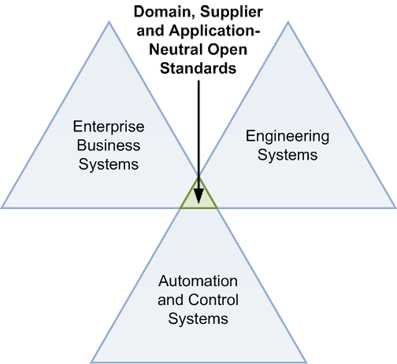
An executive summary of a white paper I wrote a few years ago still exists on my Dropbox here. The information remains relevant even though some of the organizations have changed and some technology has been updated.
OIIE
The Open Industrial Interoperability Ecosystem (OIIE) enables a shift from traditional systems integration methods to standards-based interoperability in asset intensive industries, including process industries, integrated energy, aerospace and defense and other key critical infrastructure sectors.
The OIIE digital ecosystem is a supplier-neutral, industrial interoperability ecosystem, which provides a pragmatic alternative to the status quo, enabling the use of Commercial Off The Shelf (COTS) applications from multiple suppliers, as well as bespoke applications. It is defined by a standardized Industry Solutions Architecture, which enables implementations of OIIE instances for both owner/operators and their major supply chain partners that are adaptable, repeatable, scalable and sustainable at substantially lower cost than traditional methods.
The OIIE is an outgrowth of several related industry standardization activities, each of which is addressing a part of the industries requirements for standards-based interoperability. The OIIE brings these individual efforts together, with the direct participation and support of multiple participating industry standards organizations. Major parts of the OIIE include standards associated with the OpenO&M Initiative and with ISO 15926. The OIIE uses these existing standards in combination with each other, to meet the identified systems and information interoperability requirements for use cases which are defined and prioritized by the industries which are served.
Articles I have written over the years:
Standard of standards model for asset data
Plethora of Protocols
Center Industrial Internet of Things
Oil and Gas Interoperability Pilot
Open O&M
OpenO&M is an initiative of multiple industry standards organizations to provide a harmonized set of standards for the exchange of Operations & Maintenance (O&M) data and associated context. OpenO&M is an open, collaborative, effort composed of diverse groups of relevant organizations and subject matter experts.
The original members of OpenO&M Initiative are ISA, MESA, MIMOSA, OAGi, and the OPC Foundation. ISA for the ISA 95 standard, MESA houses B2MML, MIMOSA has CCOM among other standards, and the OPC Foundation for OPC UA.
The purpose of last week’s conference calls was to revitalize the work, introduce additional organizations, and (importantly) new and younger participants. I left the meeting with renewed optimism that the work will continue to fruition. I am personally a globalist, but as a citizen and resident of the US, I hope that our engineers wake up to the utility of standards. Most interest in general over the past several years has been found in Asia with Europe remaining strong.
ISBM
Perhaps the component that holds everything together is the ISBM. This was previously described as ws-ISBM as it was based on SOAP and web services. The March 2020 update to ISBM v2.0 added REST and JSON support.
ISBM is an implementation specification for ISA-95 Message Service Model. It provides additional specificity that is required to enable two or more groups to develop implementations of the MSM that will properly interoperate with each other without a priori knowledge of each other. The ISBM provides a consistent set of specifications supporting both intra- and inter-enterprise activities, where a combination of functionality, security, supplier-neutrality and ease of implementation are required for industry digital transformation.