by Gary Mintchell | Apr 6, 2020 | Asset Performance Management, Interoperability, Operations Management, Standards
My inbox has accumulated a plethora of news about open—open standards, open source, open interoperability. Open benefits implementers (end users) because so much thought and work have been done already defining models, data, messaging, and the like that integration time and complexity can be greatly reduced. Yes, integrators remain necessary. But time to production, one of the critical measures of product success, improves. Not to mention time to trouble shoot both during startup and during operation.
Without warning a short time ago, I received a call from Alan Johnston, president (and driving force for many years) of MIMOSA. I attended MIMOSA meetings for several years and served for a year as director of marketing. I was even part of the meeting that birthed the OIIE name and fleshed out the original model. I set up a number of meetings, but we were just a little premature. We needed a bit more momentum from industry and academia to get things going. The reason for Alan’s call was that momentum was growing again. Several organizations in Australia are interested, there is renewed interest from the ISA 95 committee, and the Open O&M Initiative gained new life.
So, I wound up sitting through most of four hours of introductory meeting as the various parties—old and new—talked about what they were working on and where it all needed to go to get the job done. And Alan was right. Progress has evolved. It’s time to talk about this again.
Benefits
The driving force for this work continues to be fostering interoperability and data/information flow among the major applications behind the design, construction, and operation & maintenance of a plant—engineering, operations, maintenance. Any of us who have ever searched for the current and correct information/specification of a piece of the process facing impending unplanned shutdown understand almost intuitively the critical nature of this work. (See the Solutions Architecture diagram.)
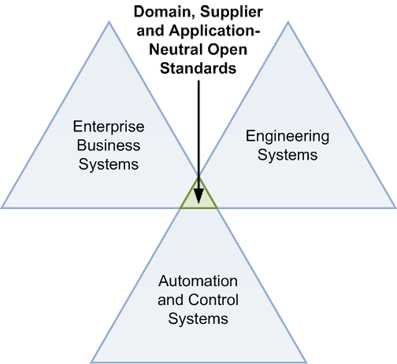
An executive summary of a white paper I wrote a few years ago still exists on my Dropbox here. The information remains relevant even though some of the organizations have changed and some technology has been updated.
OIIE
The Open Industrial Interoperability Ecosystem (OIIE) enables a shift from traditional systems integration methods to standards-based interoperability in asset intensive industries, including process industries, integrated energy, aerospace and defense and other key critical infrastructure sectors.
The OIIE digital ecosystem is a supplier-neutral, industrial interoperability ecosystem, which provides a pragmatic alternative to the status quo, enabling the use of Commercial Off The Shelf (COTS) applications from multiple suppliers, as well as bespoke applications. It is defined by a standardized Industry Solutions Architecture, which enables implementations of OIIE instances for both owner/operators and their major supply chain partners that are adaptable, repeatable, scalable and sustainable at substantially lower cost than traditional methods.
The OIIE is an outgrowth of several related industry standardization activities, each of which is addressing a part of the industries requirements for standards-based interoperability. The OIIE brings these individual efforts together, with the direct participation and support of multiple participating industry standards organizations. Major parts of the OIIE include standards associated with the OpenO&M Initiative and with ISO 15926. The OIIE uses these existing standards in combination with each other, to meet the identified systems and information interoperability requirements for use cases which are defined and prioritized by the industries which are served.
Articles I have written over the years:
Standard of standards model for asset data
Plethora of Protocols
Center Industrial Internet of Things
Oil and Gas Interoperability Pilot
Open O&M
OpenO&M is an initiative of multiple industry standards organizations to provide a harmonized set of standards for the exchange of Operations & Maintenance (O&M) data and associated context. OpenO&M is an open, collaborative, effort composed of diverse groups of relevant organizations and subject matter experts.
The original members of OpenO&M Initiative are ISA, MESA, MIMOSA, OAGi, and the OPC Foundation. ISA for the ISA 95 standard, MESA houses B2MML, MIMOSA has CCOM among other standards, and the OPC Foundation for OPC UA.
The purpose of last week’s conference calls was to revitalize the work, introduce additional organizations, and (importantly) new and younger participants. I left the meeting with renewed optimism that the work will continue to fruition. I am personally a globalist, but as a citizen and resident of the US, I hope that our engineers wake up to the utility of standards. Most interest in general over the past several years has been found in Asia with Europe remaining strong.
ISBM
Perhaps the component that holds everything together is the ISBM. This was previously described as ws-ISBM as it was based on SOAP and web services. The March 2020 update to ISBM v2.0 added REST and JSON support.
ISBM is an implementation specification for ISA-95 Message Service Model. It provides additional specificity that is required to enable two or more groups to develop implementations of the MSM that will properly interoperate with each other without a priori knowledge of each other. The ISBM provides a consistent set of specifications supporting both intra- and inter-enterprise activities, where a combination of functionality, security, supplier-neutrality and ease of implementation are required for industry digital transformation.
by Gary Mintchell | Mar 12, 2020 | Asset Performance Management, Interoperability, Operations Management, Standards
Alan Johnston caught up with me yesterday to update me on progress MIMOSA has made toward updating and adoption of its asset information data and data flow models–described by the Open Industrial Interoperability Ecosystem (OIIE). I had been working with them a few years ago, but it was too early for the promotional work I could help them with.
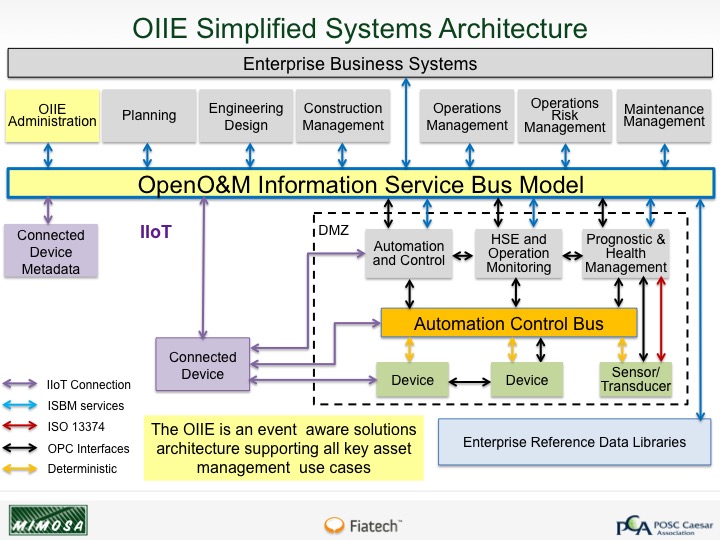
[Note: This is an old slide I had in my database. I don’t think Fiatech and POSC Caesar are still involved, but I cannot edit the slide. The ISA 95 committee is still involved.]
I did write an Executive Summary White Paper that has been downloaded many times over the years. This paper is four years old, but I think it still describes the ideas of interoperability, using standards, handing off from engineering to operations and maintenance of process plants.
Many operations and maintenance managers have expressed frustrations of handover and startup events. When I’ve described this system, they’ve all been receptive.
On the other hand, neither the large integration companies nor the large automation and control companies are thrilled with it out of concern about greatly reduced revenue generated by lock in.
I could reference the work of the Open Process Automation group attempting also a “standard of standards” approach to dissociating software from hardware for improved upgradability. Schneider Electric (Foxboro) and Yokogawa have seen the possibility of competitive advantage, especially with ExxonMobil, with this approach. But the view is not generally held.
Back to Alan. He has been making progress on the standards adoption front and getting some buy-ins. I’ve always seen the potential for improved operations and maintenance from the model. But the amount of work to get there has been staggering.
Looks like they are getting there.
by Gary Mintchell | Dec 17, 2019 | Asset Performance Management, Data Management, Internet of Things, Manufacturing IT, Software
Suppliers of manufacturing software, some from surprising places, are putting sizable investments into products that will help customers reap the rewards of digitalization. Today, I’m looking at both ABB and Emerson Automation Solutions. Previously I checked out GE Digital and Rockwell Automation. Each has taken a slightly different course toward the goal, but notice the common thread of enhancing software products to help customers prosper.
ABB enhances manufacturing management technology
The new version of ABB Ability Manufacturing Operations Management will offer new features including:
- Enhanced user experience based on new HTML 5 web client;
- A new smart interactive dashboard application that provides greater visibility and collaboration;
- A new statistical process control (SPC) application, to determine if each process is in a state of control;
- A new Batch Compare application – for advanced batch analysis.
“ABB Ability Manufacturing Operations Management is a comprehensive, scalable and modular software suite that optimizes visibility, knowledge and control throughout the operations domain,” said Narasimham Parimi, Head of Digital Products – Product Management, Process Control Platform. “This release provides a range of rich new functionality and a new enhanced user experience that enables operations to become more productive and responsive.”
ABB Ability Manufacturing Operations Management is designed to simplify production management by enabling performance monitoring, downtime management, and maintenance support, as well as providing statistical production analysis tools. It provides solutions and tools to facilitate the collection, consolidation and distribution of production, quality and energy information via the plant’s web-based reports, trends, and graphs.
A new, self-service dashboard application promotes increased collaboration, providing visibility from shop floor to top floor and spanning IT and OT environments. It increases data connectivity to all apps and modules within the MOM suite, combining historic and manufacturing data and providing the user with improved customization capabilities. Dashboards can be shared amongst users, further promoting collaboration between teams. Trends and events are displayed together, which enables customers to identify issues and opportunities enabling informed and timely decisions.
The new common services platform features an HTML 5 web platform that runs across all suites ensuring customers have a seamless user experience, so that applications can be viewed on different devices right down to a 10-inch tablet.
Statistical data process control (SPC) is used in manufacturing to determine if each process is in a state of control. The new SPC application works across all the different apps and modules and helps the user to improve quality and production related performance.
In addition to the existing Batch View and Batch Investigate features, a comparison option has been added to the platform’s batch analysis applications, allowing different types of comparison.
Cyber security remains one of the key issues in the advancement of Industry 4.0, and the new features in MOM include enhanced security.
Emerson Expands Analytics Platform
Plantweb Insight platform adds two new Pervasive Sensing applications that manage wireless networks more efficiently with a singular interface to the enterprise.
Emerson has added two new IIoT solutions to its Plantweb Insight data analytics platform that will enable industrial facilities to transform the way they manage their enterprise-level wireless network infrastructure.
As digitalization and wireless technology adoption continue to rapidly expand in industrial facilities throughout the world, the need for greater visibility of network infrastructure performance is key. These new Plantweb Insight applications provide a quick-to-implement, scalable IIoT solution that helps customers advance their digital transformation strategies and achieve greater operational efficiencies.
The new Plantweb Insight Network Management application provides continuous, centralized monitoring of WirelessHART networks. This first-of-its-kind application provides a singular, consolidated view of the status of all wireless networks in a facility, with embedded expertise and guidance for advanced network management.
A key feature of the Plantweb Insight Network Management application is a configurable mesh network diagram, providing visualization of network design and connections along with device-specific information. It also provides an exportable record of syslog alerts, network details outlining conformance to network best practices and more.
While the new network management application provides a holistic look at wireless networks, the Plantweb Insight Power Module Management application drills down to the device level, allowing facilities to keep their wireless devices appropriately powered so they can continuously transmit key monitoring data. By aggregating power module statuses, users can evolve traditional maintenance planning and implement more efficient and cost-effective practices.
“We were able to infuse a decade of experience with wireless technology into these new offerings,” said Brian Joe, wireless product manager with Emerson’s Automation Solutions business. “Our customers will now be able to manage and improve hundreds of networks through a singular interface, realizing significant efficiencies in individual network and wireless device management and maintenance.”
These new applications further enhance the Plantweb Insight platform, a set of pre-built analytics primarily focusing on monitoring key asset health. Other applications in the platform include pressure relief valve monitoring, heat exchanger monitoring and steam trap monitoring.
by Gary Mintchell | Nov 12, 2019 | Asset Performance Management, Data Management, Manufacturing IT, Operations Management, Software
Keynoters have a tough time with originality these Digital Days with everyone emphasizing Digital Transformation. Steve Lomholt-Thomson, chief revenue officer of AVEVA, took us on a Digital Journey this morning. Setting the tone of the three days of AVEVA World Congress (North America edition).
Three technology trends to watch: an IoT boom; cloud/empowered edge; and, AI / ML. The theme is digital. The Digital Organization discovers its Digital DNA, figures out how to build that Digital DNA through people who challenge the status quo; and then figures out how to track talent flow.
Which all starts us on our Digital Journey. On this journey, we unify end-to-end data, connect data silos taking an wholistic view of the business, and then visualize our assets and supply chain. I believe implied in all this is the company’s product AVEVA System Platform. The company touted six customer stories with at least five of them (and probably the sixth) all leveraging System Platform.
Oh, and the only time the “W” word was used referred to past tense.
Other areas of the company were highlighted:
Focus on assets–asset performance management including how to use machine learning (ML) and artificial intelligence (AI) for predictive analytics (predictive maintenance.
How to combine it all into a Digital Twin–bringing the design lifecycle and physical lifecycle into congruence.
Recently hired head of North America business, Christine Harding, interviewed customers from Campbell’s (soup/snacks), Quantum Solutions (integration project at St. Louis/Lambert airport), and Suncor (Canadian oil sands).
I have the rest of today and then tomorrow to take deeper dives into many of these topics. If there is anything you want me to ask, send a note.
by Gary Mintchell | Oct 8, 2019 | Asset Performance Management, Manufacturing IT, Software
This announcement from Schneider Electric originated from the conference in Barcelona that I will be attending in Austin, Texas. It supports a trend we’re seeing of suppliers breaking software into specific-purpose chunks to make it easier for customers to purchase, install, and maintain. The EcoStruxure Plant Performance Advisors suite points toward food and beverage; mining, minerals and metals; oil and gas; water and wastewater; and other industrial enterprises.
These comprise a specialized suite of smart manufacturing apps and digital services, providing easy-to-understand, real-time analytics.
“The digital transformation vision is coming to life for industrial operations,” said Sophie Borgne, senior vice president, Schneider Electric Digital Plant. “Industry 4.0 has embraced digitalization but now must get out of ‘pilot purgatory’ and scale up. Respecting an industrial enterprise’s operational investment, the modular EcoStruxure Plant Performance Advisors make it easy for plants of all sizes—not just big corporations to modernize at a sustainable pace and accelerate their digital transformation in very simple, step by step manner.”
Data-driven Plant Performance Management
Schneider rightly contends that IIoT blurs the line between information technology (IT) and operational technology (OT) yielding great amounts of data. The Advisors enhance asset optimization, asset performance management, predictive maintenance, and real-time decision-making.
Schneider Electric utilizes digitalization in its own factories. Using technology, including EcoStruxure Plant Performance Advisors, its Smart Factory in Bantam, Indonesia is reporting a 44% reduction in machine downtime in one year. The Schneider Electric Smart Factory in Vaudreil, France also implemented EcoStruxure Plant Performance Advisors, which contributed to:
- 10% reduction in energy consumption
- 25% improvement in plant operations efficiency.
- 20% reduction in maintenance costs.
- 20% reduction in diagnosis and repair time.
EcoStruxure Plant Advisors are fully configurable, off-the-shelf solutions for easy integration into even the most advanced systems. By providing users with a familiar application theme and environment, an efficient plant can create synergies for processes and empower digital operators. This greatly reduces the user learning curve, saving time and money.
Schneider Electric’s modular and scalable EcoStruxure Plant Advisors suite includes:
- EcoStruxure Pumping Performance Advisor is a new digital service for the continuous improvement of water and wastewater pumping assets in 24/7 operations. By addressing challenges such as cost of water, plants can save up to 15% in OPEX through pump optimization.
- EcoStruxure Equipment Efficiency Advisor provides real-time efficiency root cause analysis. It then recommends appropriate action plans for increasing capacity while reducing unscheduled downtime and waste, which often results in immediate 5% to 10% OEE gains.
- EcoStruxure Augmented Operator Advisor uses augmented reality to slash the amount of time a worker spends looking for information to about a tenth of current levels. By superimposing real-time data and virtual objects (point of interest, documentation, procedures) onto cabinets or machines, this “contactless maintenance” model also increases safety. EcoStruxure Augmented Operator Advisor V2.4 is easy to customize; no special platform knowledge is required. Users can also easily add augmented reality into existing procedures and export notes and analysis to share with others.
- EcoStruxure Secure Connect Advisor with embedded cybersecurity provides a digitally secure and simple asset monitoring connection for remote diagnostic and maintenance that reduces plant downtime while saving time and travel costs to maintain critical assets. In some cases, this has resulted in a shortened time to solution from over 7 days to as little as 4 hours.
EcoStruxure is Schneider Electric’s open, interoperable, IoT-enabled system architecture and platform.
by Gary Mintchell | Oct 4, 2019 | Asset Performance Management, Manufacturing IT, Software
I guess I did attend the last GE software conference Minds + Machines. However, the reconstituted and independent GE Digital recently held a user conference where it announced a number of upgrades to its IIoT software. These are firmly within the current trends of connecting and mobility.
The product updates include:
- Predix Essentials, which makes it easier for industrial companies to connect, visualize and analyze their data
- Asset Answers, which helps customers to understand the competitive potential of Asset Performance Management (APM) software
- Webspace 6.0, a new HTML5 interface that seamlessly brings automation data to operators across any mobile device
Edge-to-Cloud Accessibility
Predix Essentials is an easy-to-use SaaS solution, helping companies connect to disparate data sources, monitor operations, and leverage edge-to-cloud predictive analytics–reducing time-to-value for operational teams looking to reduce waste, lower costs, and increase performance.
Developed in partnership with a number of customers, including silicon chip manufacturer Intel, Predix Essentials is a natural first step for industrial businesses looking to leverage the power of cloud-based Industrial IoT technologies, providing the connectivity, visualization and analysis capabilities that are the cornerstones of a digital transformation journey, regardless of vertical or maturity.
Suitable for industrial companies of all kinds, Predix Essentials is also the foundation of GE Digital’s APM and OPM application suites, providing core functionality and bridging the entire software portfolio by connecting GE Digital cloud-based solutions to on-premises data from its Automation, MES and Historian solutions.
Identifying Maintenance Strategies
Asset Answers is a benchmarking tool that helps customers quickly import and assess data to better understand how their asset maintenance compares with similar companies in their particular domain, or even against their own internal performance across sites.
With this intelligence, customers can determine where best to invest in updating maintenance regimes or capabilities, and ultimately provide a seamless path to products like APM to manage and optimize assets across their business. Asset Answers is available for many sectors, including power generation, oil and gas and chemicals.
Improving Operator Mobility
Webspace 6.0, a web and mobility solution, brings the full visualization and control capabilities from GE’s iFIX and CIMPLICITY HMI/SCADA software seamlessly across devices, including smartwatches, phones, tablets and desktops.
Offering enhanced encryption and new zero-install HTML5 client, Webspace 6.0 improves the way that operators receive and react to operational insights, whether they are in the field, on the plant floor or at a desk, providing them the flexibility to make informed decisions and share their expertise, regardless of location. By dynamically extending automation solutions, Webspace 6.0 increases information sharing across teams, speeds the right operator actions, and improves agility with real-time visualization and control anywhere, anytime.
Availability
“GE Digital continues to release innovations that forge the way for industrial customers working on transforming their operations,” said Pat Byrne, CEO of GE Digital. “By continuing to invest across our portfolio of industrial software, and by making it easier than ever for our customers to unlock the power of the Industrial IoT, GE Digital is strengthening its customers’ ability to become more productive, efficient and safe.”
Predix Essentials, Asset Answers and Webspace 6.0 are generally available today as part of GE Digital’s portfolio of industrial software products covering HMI/SCADA, Historian, Asset Performance Management and Manufacturing Execution System applications. Today’s announcements build on a strong thread of recent investments in product innovations, all designed to solve a broad range of industrial customer challenges, including iFIX 6.0; Historian 7.2, Plant Applications 8.0 and Predix Manufacturing Data Cloud for the manufacturing sector; Grid Analytics for the power transmission and distribution market; and APM Integrity’s Compliance Management for the O&G and Power Generation industries.